Advanced Printing for Microelectronic Packaging
March 11, 2015 | Kenneth H. Church, Xudong Chen, Joshua M. Goldfarb, Casey W. Perkowski, Samuel LeBlanc, nScrypt Inc.Estimated reading time: 16 minutes
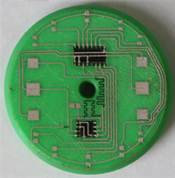
Electronic packaging has been a stable research topic since the vacuum tube era. These were physically large and fragile devices and typically the electronic connection was a mechanical socket that ensured good contact over a large surface area. The issues involved were both electrical contact and mechanical security or ruggedness. The evolution of electronics from vacuum tubes to semiconductors presented opportunities to shrink the electronic devices without reducing the performance. This dramatic change forced a change in connections as well and the idea of mechanically connecting electronics needed to be studied. Solder was a very old, literally thousands of years old [1], technology, but for electronics was a natural fit. A natural fit given two reasons, one was the obvious electrical attributes, but the second was the mechanical flex that solder could provide between two joining surfaces [2]. This became especially important with two dissimilar surfaces. Solder also became its own research topic and the growth and maturity of this process has proven to be one of the most important contributions to electronic packaging since the semiconductor; almost all electronic devices today have solder. The mechanical bond was important, but this alone was not enough given the rugged requirements of some of the electronic devices. The extra ruggedness would be provided using mechanical devices and if the electronics were too small, then another technology that was also thousands of years old was used, glue [3]. Adhesives primary contribution was to enhance ruggedness but adding features such as conductivity to adhesives provided additional value. Solders and adhesives are an important part of electronic packaging and the future of electronics is to increase functions per volume which implies tighter pitch and smaller traces, smaller pads, smaller solder dots and finer features in adhesive patterns. This requires improved methods for applying solder and adhesives. This paper will cover in part, advanced dispensing of fine resolution solder and adhesive dots and lines.
Additionally, just as electronic packaging has evolved from mechanical connections to solder, a future of monolithic electronic packaging will evolve. The idea of circuits in structures has been presented previously by Church et el [4]. Additional demonstrations of printed circuit structures will be shown and the concept of using similar technology to dispensing dots and lines of solder and adhesive will be explained. The concept of dispensing a wide range of materials in three dimensions presents a potential change in electronic packaging. This paper will cover the concept of combining dispensing technologies on a single platform to build integrated and monolithic electronic structural circuits.
Micro-dispensing
There are a number of technologies that can be utilized for micro-dispensing. The technology utilized for the results in this paper is from the standard company micro-dispenser. This has two distinct characteristics that have proven a significant advantage for dispensing very small volumes of solder and adhesive. The first is the specialty shaped pen tip that allows extremely high viscosities (greater than 10 Mcp) and the second is the valve in proximity to the pen tip for exceptional control. Very small volumes such as single digit nanoliter or even less than nanoliter volumes are dimensions of interest with respect to dot size. 300 micron pads are of interest for solder, but the future of solder pads will be much small than 300 microns; 100 microns and less. A 100 micron solder dot will be a need in the near future and it is even conceivable to move toward 50 micron solder dots. A 300 micron solder dot will have a volume of approximately 8 nanoliters (assuming a half sphere shape). An 80 micron solder dot will have a volume of approximately 130 picoliters, a fraction of a nanoliter.
Figure 1 below is a table showing ½ sphere shaped contours diameter versus volume. Controlling small volumes in a
repeatable manner will be important when considering small volumes.
Figure 1. Half sphere diameters converted to volumes.
In addition to dots, there is the need to print fine lines of adhesives or conductive adhesives and other materials. Adhesives can vary significantly in material attributes. These attributes are such properties as viscosity, thixotropy and particle loading. The ability to print adhesive materials consistently and also handle the wide range of diverse properties from the vast array of available materials can be important. The contribution this team has made is to do that with exceptional control for small volumes, provide finer features of 150 microns or less and to control the starts and stops of the dispensed lines and features.Page 1 of 3
Testimonial
"In a year when every marketing dollar mattered, I chose to keep I-Connect007 in our 2025 plan. Their commitment to high-quality, insightful content aligns with Koh Young’s values and helps readers navigate a changing industry. "
Brent Fischthal - Koh YoungSuggested Items
MacDermid Alpha Electronics Solutions Unveils Unified Global Website to Deepen Customer, Talent, and Stakeholder Engagement
07/31/2025 | MacDermid Alpha Electronics SolutionsMacDermid Alpha Electronics Solutions, the electronics business of Elements Solutions Inc, today launched macdermidalpha.com - a unified global website built to deepen digital engagement. The launch marks a significant milestone in the business’ ongoing commitment to delivering more meaningful, interactive, and impactful experiences for its customers, talent, and stakeholders worldwide.
KOKI to Showcase Analytical Services and New HF1200 Solder Paste at SMTA Guadalajara 2025
07/31/2025 | KOKIKOKI, a global leader in advanced soldering materials and process optimization services, will exhibit at the SMTA Guadalajara Expo & Tech Forum, taking place September 17 & 18, 2025 at Expo Guadalajara, Salón Jalisco Halls D & E in Guadalajara, Mexico.
Weller Tools Supports Future Talent with Exclusive Donation to SMTA Michigan Student Soldering Competition
07/23/2025 | Weller ToolsWeller Tools, the industry leader in hand soldering solutions, is proud to announce its support of the upcoming SMTA Michigan Expo & Tech Forum by donating a limited-edition 80th Anniversary Black Soldering Set to the event’s student soldering competition.
Koh Young Appoints Tom Hattori as President of Koh Young Japan
07/21/2025 | Koh YoungKoh Young Technology, the global leader in True 3D measurement-based inspection solutions, announced the appointment of Tom Hattori as President of Koh Young Japan (JKY).
Silicon Mountain Contract Services Enhances SMT Capabilities with New HELLER Reflow Oven
07/17/2025 | Silicon Mountain Contract ServicesSilicon Mountain Contract Services, a leading provider of custom electronics manufacturing solutions, is proud to announce a significant upgrade to its SMT production capability with the addition of a HELLER 2043 MK5 10‑zone reflow oven to its Nampa facility.