-
-
News
News Highlights
- Books
Featured Books
- pcb007 Magazine
Latest Issues
Current IssueSales: From Pitch to PO
From the first cold call to finally receiving that first purchase order, the July PCB007 Magazine breaks down some critical parts of the sales stack. To up your sales game, read on!
The Hole Truth: Via Integrity in an HDI World
From the drilled hole to registration across multiple sequential lamination cycles, to the quality of your copper plating, via reliability in an HDI world is becoming an ever-greater challenge. This month we look at “The Hole Truth,” from creating the “perfect” via to how you can assure via quality and reliability, the first time, every time.
In Pursuit of Perfection: Defect Reduction
For bare PCB board fabrication, defect reduction is a critical aspect of a company's bottom line profitability. In this issue, we examine how imaging, etching, and plating processes can provide information and insight into reducing defects and increasing yields.
- Articles
- Columns
- Links
- Media kit
||| MENU - pcb007 Magazine
Fire Retardancy: What, Why, and How
April 14, 2015 | Alun Morgan, European Institute of Printed CircuitsEstimated reading time: 2 minutes
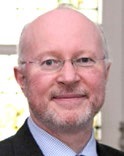
I. What are flame retardants?
Flame retardants are compounds, which when added to materials during or after manufacture, inhibit or suppress the combustion process.
They interfere with combustion at various stages of the process, e.g., during heating, decomposition, ignition or flame spread. Their primary function is to suppress the spread of fires or delay the time of flashover so that people can escape.
Flame retardants used in plastic materials fall broadly into two categories, namely additive and reactive. Additive flame retardants are incorporated and dispersed into the plastic prior to, during, or most commonly following polymerisation. If they are chemically compatible with the plastic they act as plasticisers, otherwise they are considered as fillers. Reactive flame retardants are chemically bound to the polymer molecule by incorporating them into the polymer backbone or by grafting them onto the backbone as branches. As reactive flame retardants are chemically bound to the host polymer they are prevented from bleeding out and thus generally exert greater flame retardancy than additive compounds due to their greater availability throughout the life cycle of the polymer into which they are incorporated.
II. Why do we need flame retardants?
On average there are more than 4,500 fatalities annually in the EU-27 as a result of fires; this accounts for 2% of all fatal injuries. Fires develop from inception through build-up until a stage where the total thermal radiation from the fire-plume, hot gases and hot compartment boundaries cause the radiative ignition of all exposed combustible surfaces within the compartment. This sudden and sustained transition of a growing fire to a fully developed fire is called flashover.
At this point the radiation of energy to the contents of the room raises all the contents to their ignition temperature whereby the contents of the room suddenly and simultaneously ignite. It is estimated that in a domestic dwelling fitted with working fire alarms on all levels where the occupants are asleep upstairs and a fire starts on the main level of the residence the occupants have about three minutes to escape if they are to have any chance of survival. The presence of flame retardants in otherwise combustible materials has two possible effects;
- The flame retardant may prevent the fire from developing altogether or;
- The flame retardant may slow down the build-up phase of the fire thus delaying the onset of flash over thus extending the escape time window.
In either case, the flame retardant serves its primary purpose of reducing the risk of fire related fatalities.
The efficacy of the use of appropriate flame retardants can be seen by way of example from the introduction of “The Furniture and Furnishings Fire Safety Regulations" in the UK in 1988. These imposed a fire resistance requirement on all upholstered furniture supplied in the UK. Between 1988 and 2002 a Government commissioned report estimated that the "Furniture and Furnishings Fire Safety Regulations" played a direct role in saving 1,150 lives and preventing 13,442 injuries.
Editor's Note: This article originally appeared in the March 2015 issue of The PCB Magazine
Testimonial
"In a year when every marketing dollar mattered, I chose to keep I-Connect007 in our 2025 plan. Their commitment to high-quality, insightful content aligns with Koh Young’s values and helps readers navigate a changing industry. "
Brent Fischthal - Koh YoungSuggested Items
Top Investment Certification on 2nd Anniversary Boosts ESCATEC’s European Presence
06/09/2025 | ESCATECTwo significant milestones in recent days by ESCATEC’s business unit in Bulgaria adds much momentum to the EMS provider’s strategy to nearshore cost-effective and high-quality electronics assembly and plastic moulding services for its customers in the European Union.
Altus, Danutek Expand Partnership with LPKF to Offer Laser Plastic Welding Solutions
05/21/2025 | Altus GroupAltus Group, a leading supplier of capital equipment and service support for the electronics manufacturing sector in the UK and Ireland, and its sister company Danutek, which serves Central and Eastern Europe, are expanding their technology offering through an enhanced partnership with LPKF, a specialist in laser-based manufacturing solutions.
Pusan National University Develops One-Step 3D Microelectrode Technology for Neural Interfaces
02/28/2025 | PRNewswireNeural interfaces are crucial in restoring and enhancing impaired neural functions, but current technologies struggle to achieve close contact with soft and curved neural tissues. Researchers at Pusan National University have introduced an innovative method—microelectrothermoforming (μETF)—to create flexible neural interfaces with microscopic three-dimensional (3D) structures.
In-mold Electronics: The Convergence of Innovative Materials and Manufacturing Techniques
08/07/2024 | Linda Stepanich, IPCPaavo Niskala, a noted expert in in-mold electronics (IME) at TactoTek, recognized the need for an industry-wide standard when one of his automotive OEM clients asked him how to test a prototype TactoTek had developed. That question led to the creation of the first-ever IPC standard of this type, IPC-8401, Guidelines for In-Mold Electronics, to be released later this year.
Delvitech’s Cutting-Edge Technology Overcomes the Conventional Boundaries of Optical Inspection at SMT Connect
05/29/2024 | DelvitechNot only does Delvitech offer an innovative solution aimed at revolutionizing automatic 3D optical inspection through seamless integration of artificial intelligence, but it stands out as the sole provider to deliver exceptional results in inspecting electronic components previously deemed challenging to assess.