-
- News
- Books
Featured Books
- pcb007 Magazine
Latest Issues
Current IssueInventing the Future with SEL
Two years after launching its state-of-the-art PCB facility, SEL shares lessons in vision, execution, and innovation, plus insights from industry icons and technology leaders shaping the future of PCB fabrication.
Sales: From Pitch to PO
From the first cold call to finally receiving that first purchase order, the July PCB007 Magazine breaks down some critical parts of the sales stack. To up your sales game, read on!
The Hole Truth: Via Integrity in an HDI World
From the drilled hole to registration across multiple sequential lamination cycles, to the quality of your copper plating, via reliability in an HDI world is becoming an ever-greater challenge. This month we look at “The Hole Truth,” from creating the “perfect” via to how you can assure via quality and reliability, the first time, every time.
- Articles
- Columns
- Links
- Media kit
||| MENU - pcb007 Magazine
A Conversation (and Day) with Joe Fjelstad, Part 1
May 3, 2015 | Barry Matties, I-Connect007Estimated reading time: 7 minutes
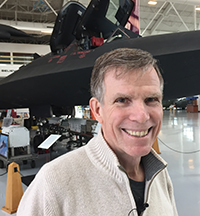
Joe Fjelstad spent a day with me recently as we toured the Evergreen Aviation & Space Museum (home of the Spruce Goose), located in the Oregon community of McMinnville. Our conversation ebbed and flowed between a wide variety of topics, from the electronics industry, to political shenanigans and the “war against failure.” In Part 1 of this multi-part series, Fjelstad introduces his “war against failure” idea, and what went terribly wrong in the advent of lead-free manufacturing.
Barry Matties: Joe, you’ve mentioned to me recently that you are changing your approach to the world—that your message is different. You said, “the war is against failure.” What do you mean by that?
Joe Fjelstad: Ah yes, the war on failure. It is a recent epiphany of mine that failure is the true enemy of electronics. It is the disease, not the symptom, which must be attacked. To date, the industry has largely focused attention on trying to make something reliable using materials and processes that are intrinsically weak. It is a Sisyphean task that will never end. It's like the arcade game Whack-a-Mole. You bang down one problem and a new problem pops up in its place somewhere else.
Much of the challenge and most of the problems are related to solder, which has gotten worse with the introduction of lead-free, a movement that I and others rallied against for several years without success, having seen that the science did not support the claims of the proponents. On the bright side, that failure was what led to the inspiration for manufacturing electronics without solder. That said, I continue to pursue that goal. However, truth be told, I would be perfectly satisfied, and I've said this on more than one occasion publicly, if the only thing that came out of my effort was that the EU reversed the ban on lead in tin-lead solder. A lot of lead has been used in electronics over the last several decades and nobody was ever harmed by it. Well I take that back. An uncounted number of people in Asia and South Asia have been harmed by leaded solder in reclamation activities there. However, that failure and onus rests at the feet of unscrupulous businesspeople in the West, who were shipping electronic waste to those areas without giving people education and training as to what the hell they were doing and what the risks were. It was a case of capitalism gone awry and innocents victimized in the process. Elimination of lead from paint and gasoline were excellent decisions relative to human health; the elimination of lead from solder, except in the case just mentioned, was, at the end of the day, an expensive and wasteful exercise with ongoing expensive ramifications.
Matties: I was listening this morning on the news about the lead-free exemption for the military and they were talking about how that may even disappear. What do you think of that as a possibility?
Fjelstad: I would say that fundamentally it has already disappeared.
Matties: Is that because components just aren't available?
Fjelstad: Yes, and that's the great irony. I made a point of that in my recent talk at the IEEE Aerospace conference in Big Sky, Montana. Here's the scenario: Presently the military is exempt and can use tin lead solder. However, the military transitioned to commercial-off-the-shelf (COTS) parts because it was going to be cheaper to make their electronics. It makes a good deal of sense. In fact, when I worked on the Land Warrior project with Pacific Consultants, we built the entire soldier-of-the-future system out of COTS. Colonel Jette, the Pentagon’s project manager overseeing this whole development made very clear his desire to use COTS. At the time, Pacific Consultants, which consisted of 35 to 40 scientists and engineers, went up against General Dynamics, Raytheon, and Motorola for the contract, and we beat them. The reason we beat them is because we actually made what the Pentagon asked for in its procurement spec. When it came to delivery, the product had the right look and feel as well as performance. In contrast, some of the competitive solutions delivered were quite bizarre. The military industrial complex got that name for a reason. It's because the military is so interwoven with the aerospace and weapons industries.
Anyway, we beat them and built the system completely out of commercial, off-the-shelf hardware. That makes sense to try and control your budgets and we built it with success and within budget, but did not win the production contract. That was given to one of the big boys. Now fast forward to what you have today with lead-free. Who drives the electronics industry? It’s not the military. They had their turn—back in the '60s and '70s; now they're just the caboose at the end of the train.Page 1 of 2
Testimonial
"We’re proud to call I-Connect007 a trusted partner. Their innovative approach and industry insight made our podcast collaboration a success by connecting us with the right audience and delivering real results."
Julia McCaffrey - NCAB GroupSuggested Items
ZESTRON Expands Capabilities with Addition of the EPS by i-Tech AG 75 Pallet Cleaning System
08/26/2025 | ZESTRONZESTRON, the global leader in high-precision cleaning solutions and services, is excited to announce the addition of a new capability in its Technical Center in Manassas, VA:
Pick and Place Machine Innovator - NECTEC Launches Next-Gen SMT Line Solution With LED and X-ray Technology
08/26/2025 | Globe NewswireNECTEC PTE. LTD., a leading provider of SMT electronics manufacturing equipment, announced the official launch of its next-generation SMT solutions, featuring newly upgraded pick and place machine, specialized LED pick and place machines, enhanced Reflow Oven technology, advanced X-ray Inspection, high-speed X-ray Counter, and premium Solder Paste
MS2 Technologies, LLC/P. Kay Focuses on Central America with First Installation in Honduras
08/24/2025 | P. Kay Metal, Inc.This year MS2 Technologies has turned their focused to the growing electronics market in Central America. With that focus came the adaptation of MS2 and the Akila System from a Honduras-based corporation with manufacturing plants in both Honduras and Mexico.
BEST Inc. Provides High-Reliability BGA Reballing and Component Rework Services
08/22/2025 | BEST Inc.BEST Inc., a leader in electronic component services, is pleased to announce its component rework services are available for all types of area array devices including ball grid array, land grid array and quad flat no-lead SMT packages.
Indium Corporation Promotes Two Leaders in EMEA (Europe, Middle East, and Africa) Markets
08/05/2025 | Indium CorporationWith its commitment to innovation and growth through employee development, Indium Corporation today announced the promotions of Andy Seager to Associate Director, Continental Sales (EMEA), and Karthik Vijay to Senior Technical Manager (EMEA). These advancements reflect their contributions to the company’s continued innovative efforts with customers across Europe, the Middle East, and Africa (EMEA).