-
- News
- Books
Featured Books
- pcb007 Magazine
Latest Issues
Current IssueThe Growing Industry
In this issue of PCB007 Magazine, we talk with leading economic experts, advocacy specialists in Washington, D.C., and PCB company leadership to get a well-rounded picture of what’s happening in the industry today. Don’t miss it.
The Sustainability Issue
Sustainability is one of the most widely used terms in business today, especially for electronics and manufacturing but what does it mean to you? We explore the environmental, business, and economic impacts.
The Fabricator’s Guide to IPC APEX EXPO
This issue previews many of the important events taking place at this year's show and highlights some changes and opportunities. So, buckle up. We are counting down to IPC APEX EXPO 2024.
- Articles
- Columns
Search Console
- Links
- Events
||| MENU - pcb007 Magazine
Estimated reading time: 2 minutes
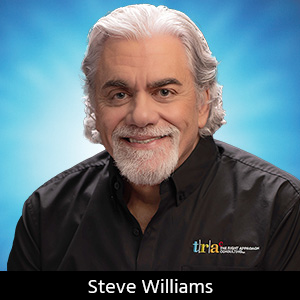
Best Practices 101: Part 6
One roadblock to achieving the true benefits of best practices is that traditional improvement efforts have always focused on reducing the time of value-added steps; in other words, reducing the amount of time it takes to do something to a product, or touch time. Let’s take a look at a drilling operation, for example, where the run time of this operation is 19½ minutes per part. Much effort is placed on fixturing, training, spindle feed and speed, etc., to reduce the run time. While this is obviously an important activity, we fail to attack the greatest opportunity for improvement: eliminating waste from this process. For example, zero effort has been expended to reduce the average two days of queue time this product waits before it can be drilled, the 25 minutes of transportation time to move this order to the next department located at the opposite end of the building, the two weeks added to the product’s lead-time waiting for raw material to arrive, or the four days of various inspections throughout the process due to inferior quality and/or process control.
Contrast this to Figure 1, which graphically represents the results of a recent best practices project done by Calumet Electronics Corporation, a company that really gets it. Calumet is a printed circuit manufacturer that could have literally 100 process steps, so travel and motion is a big deal. By focusing on motion waste, this company was able to reduce one department’s functional motion by 45%, taking it from 162’ down to 88’. Saving seconds at the expense of minutes, hours, days or even weeks is saving a penny where you could be saving a dollar, and as I have said a thousand times before, “It’s always about the dollars.”
Where Do You Spend Your Money?
Now, let’s take a macro look at where companies spend their money in terms of the cost of quality. The cost of quality refers to costs related to prevention, appraisal (inspection), rework, and scrap (customer returns are factored into either rework or scrap).
The traditional business will spend about three times the amount of money on appraisal (inspection) than they do on prevention. When you combine appraisal costs with the exponential amount of dollars that are being wasted on rework and scrap, it is clear that this is not an effective model. Now, contrast that with the lean best practice business model. By spending a majority of their expenditures on prevention, appraisal costs can be greatly reduced and rework and scrap are maintained at minimal levels.
Not only are the dollars being spent in the right places, consider the order of magnitude of total cost. All the costs in the best practice business model, combined, amount to less than the money a traditional company is wasting in scrap alone. Talk about financial metrics; these savings transfer directly to the bottom line.
Editor's Note: This article originally appeared in the April issue of The PCB Magazine.
More Columns from The Right Approach
The Right Approach: I Hear the Train A Comin'The Right Approach: Culture Change is Key to a QMS
The Right Approach: Leadership 101—Be a Heretic, Not a Sheep
The Right Approach: Leadership 101—The Law of Legacy
The Right Approach: Leadership 101: The Law of Explosive Growth
The Right Approach: Leadership 101—The Law of Timing
The Right Approach: The Law of Sacrifice
The Right Approach: The Law of Priorities