Cadence Paper: Automating Inter-Layer In-Design Checks in Rigid-Flex PCBs
May 25, 2016 | Ed Hickey, Cadence Design SystemsEstimated reading time: 10 minutes
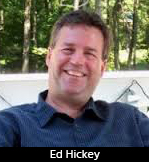
Flexible PCBs (flex/rigid-flex) make it possible to create a variety of products that require small, lightweight form factors such as wearable, mobile, military, and medical devices. As flexible PCB fabrication technology has matured in response to demands for smaller, lighter products, new design challenges have emerged. This paper discusses some of the key challenges to address and also introduces a new PCB design approach that enhances productivity through in-design inter-layer checks required to ensure correct-by-construction design.
Introduction
Inside a variety of small electronic devices—from earphones to smartphones, tablets, and laptops—are rigid-flex PCBs comprised of rigid and flexible substrates laminated together. Such circuits are considered reliable, versatile, and space efficient. As designs continue to shrink for a variety of applications, this type of flexible substrate for electronic circuitry keeps growing in popularity, particularly in consumer electronics (Figure 1). Because of the bending possible with rigid-flex circuits, designers can place much more circuitry into the space available, even stacking the board layers in a 3D format on the rigid side. Multiple stack-up zones contribute to lower cost. Traditionally, designers would integrate the flexible portion of their circuitry as a connector from one rigid board to another. However, flexible technology has matured substantially in recent years. Now, because of more stringent area requirements, designers are placing components on the flexible circuit area, using this area like a rigid substrate. PCB design technology to address rigid-flex design has been available for some time. However, utilizing both the rigid and the flexible areas for components introduces new fabrication challenges that require more sophisticated PCB design technology.
Accommodating New Materials and Design Rules
Rigid-flex PCBs consist of areas (zones) that differ in layer count and materials. Stiffeners bring rigidity to these PCBs, and are placed near or on the opposite side of components or near connector areas. They usually consist of a metal, such as stainless steel or aluminum, with the addition of dielectric material like a polymide build-up. The flexible portion of the design typically consists of a dielectric material with bend areas. The bend area must restrict the placement of components and vias; otherwise, these elements contribute to stress and cracking. Routing must cross perpendicular to the bend line to minimize material stress at this location.
Adjacent layer routing through the bend area should be offset to prevent what is called the I-BEAM effect. Traces routed in this manner can add stiffness to an area designed to be flexible. There’s also a transition zone—an intersection between the rigid and flex zones that may require overlap of material and also special spacing for holes and conductive materials. Consider the transition zone a stress-relief area. As a simple example, a design might have a four-layer rigid connected to a two-layer flex, which terminates on a four-layer rigid. More complex configurations are now common, and there are many possibilities. Figure 2 depicts the layers and zones of a rigid-flex design.
The traditional cross-section editor for a single stack-up has evolved to support multiple cross-sections representing the different PCB fabrics. Standard cross-section editors supporting conductor, plane, and dielectric layers have advanced to include mask and coating layers that exist above/below the surfaces of the flex PCB. Such layers include:
- A cover layer (coverlay) of adhesive-coated film pressed onto the stack-up to insulate the circuitry
- Material masks consisting of precious metals, adhesives, and paste masks
- Stainless steel or aluminum stiffeners that restrict flexing where components reside
- Special plating areas like ENEPIG
To meet customers’ requirements, the fabrication industry continues to innovate, increasing the number of conductive and non-conductive layers on flex and rigid-flex designs. There’s also been an increase in different types of materials and associated rules required in rigid-flex PCB design. As a result, designers have to do many more manual checks in order to benefit from the advantages of this technology—and to ensure that their designs can be fabricated according to their intent. To ensure correct-by-construction design, designers need in-design inter-layer checks to flag errors right when they are created. After all, fixing errors after the design is somewhat complete takes a lot longer than finding and then fixing the errors as they occur. Having this capability avoids two frustrating, time-consuming steps:
- Manual checks after the design is complete (prior to manufacturing hand-off)
- Iterations required when the designer has to check the design, make fixes, redesign, check again, and so onPage 1 of 4
Testimonial
"The I-Connect007 team is outstanding—kind, responsive, and a true marketing partner. Their design team created fresh, eye-catching ads, and their editorial support polished our content to let our brand shine. Thank you all! "
Sweeney Ng - CEE PCBSuggested Items
Koh Young Appoints Tom Hattori as President of Koh Young Japan
07/21/2025 | Koh YoungKoh Young Technology, the global leader in True 3D measurement-based inspection solutions, announced the appointment of Tom Hattori as President of Koh Young Japan (JKY).
Silicon Mountain Contract Services Enhances SMT Capabilities with New HELLER Reflow Oven
07/17/2025 | Silicon Mountain Contract ServicesSilicon Mountain Contract Services, a leading provider of custom electronics manufacturing solutions, is proud to announce a significant upgrade to its SMT production capability with the addition of a HELLER 2043 MK5 10‑zone reflow oven to its Nampa facility.
Knocking Down the Bone Pile: Addressing End-of-life Component Solderability Issues, Part 4
07/16/2025 | Nash Bell -- Column: Knocking Down the Bone PileIn 1983, the Department of Defense identified that over 40% of military electronic system failures in the field were electrical, with approximately 50% attributed to poor solder connections. Investigations revealed that plated finishes, typically nickel or tin, were porous and non-intermetallic.
SHENMAO Strengthens Semiconductor Capabilities with Acquisition of PMTC
07/10/2025 | SHENMAOSHENMAO America, Inc. has announced the acquisition of Profound Material Technology Co., Ltd. (PMTC), a premier Taiwan-based manufacturer of high-performance solder balls for semiconductor packaging.
KYZEN to Highlight Understencil and PCB Cleaners at SMTA Querétaro Expo and Tech Forum
07/09/2025 | KYZEN'KYZEN, the global leader in innovative environmentally responsible cleaning chemistries, will exhibit at the SMTA Querétaro Expo & Tech Forum, scheduled to take place Thursday, July 24, at Centro de Congresos y Teatro Metropolitano de Querétaro.