-
- News
- Books
Featured Books
- pcb007 Magazine
Latest Issues
Current IssueSales: From Pitch to PO
From the first cold call to finally receiving that first purchase order, the July PCB007 Magazine breaks down some critical parts of the sales stack. To up your sales game, read on!
The Hole Truth: Via Integrity in an HDI World
From the drilled hole to registration across multiple sequential lamination cycles, to the quality of your copper plating, via reliability in an HDI world is becoming an ever-greater challenge. This month we look at “The Hole Truth,” from creating the “perfect” via to how you can assure via quality and reliability, the first time, every time.
In Pursuit of Perfection: Defect Reduction
For bare PCB board fabrication, defect reduction is a critical aspect of a company's bottom line profitability. In this issue, we examine how imaging, etching, and plating processes can provide information and insight into reducing defects and increasing yields.
- Articles
- Columns
- Links
- Media kit
||| MENU - pcb007 Magazine
Estimated reading time: 4 minutes
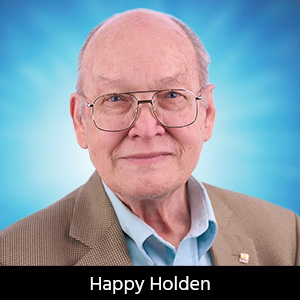
Contact Columnist Form
Happy’s Essential Skills: Computer-Aided Manufacturing, Part 2 - Automation Examples
In Part 1, I explored currently existing automation protocols and some new ones just coming on the market. Here, I will present some examples from my own projects.
Semiconductor Productivity Network at HP: PC-10[6]
Semiconductor fabs like to avoid writing custom software to fit all of the idiosyncrasies of individual processing systems. So HP developed PC-10 to handle IC process equipment by separating it into general classes. SECS II was a mandatory prerequisite of the equipment before an interface to PC-10 could be developed. (Figure 9 and Figure 10.)
Figure 9: Real-time monitoring of equipment status. (Source: Sematech Generic Equipment model)
HP's approach to interfacing was to survey a representative number of processing systems within a class to develop a generic model. A class is a group of equipment systems that operate similarly and perform the same general functions so that the communications requirements look the same to PC-10. The assumption is that each piece of equipment in an equipment class supports a subset of the SECS II data streams and functions that PC-10 supports for that class. HP also assumed that the order of the messages, which is not defined by SECS II, is generally the same for all equipment in that class. In the July, 1985 HP Journal article[6], the author reported:
To date they have encountered batch, metrology, serial, and material handling equipment, systems, such as diffusion furnaces, process wafers in large quantities (batches). The primary characteristic is that once a batch has started processing, no more wafers can be added until the process sequence has run to completion. PC-10 will download only one recipe to the batch station when the batch is tracked in and no other batches will be allowed in until the first batch is done.
Metrology systems are classified separately because they provide certain measurement data to PC-10. PC-10 supports SECS II stream 6 messages, which handle the transfer of measurement data to the host system for this class of equipment. Examples are line width, film thickness, and defect measuring devices. Wafers passing through these stations are not processed, but are merely measured to determine the effectiveness or accuracy of previous process steps.
Serial processing handles wafers one at a time. Wafers from one lot may be entered into the equipment for processing before the preceding lot has been completed. Photolithography wafer track systems are a prime example of serial equipment. PC-10, to ensure that the proper recipe is executed for each lot, must check to see if the recipe already executing is the proper recipe for the next lot. If not, it must download the new correct recipe at the proper time for beginning processing of the new lot.
Material handling requires an entirely different set of messages, since material handling systems are responsible only for transporting the wafers from one station to another. PC-10 instructs the material handling system to take a lot or a group of lots to a particular piece of equipment. Examples of material handling systems include robots or tracks used to move the wafers through the fabrication area. The challenge we face when we address a new class of equipment to develop our models is to perform an adequate survey of such equipment on the market and develop an accurate, yet general model of how these pieces of equipment operate.
Figure 10: PC-10 process control and process supervision including recipes’ downloading. (Source: Sematech Generic Equipment model)
Figures 10 and 11 are simple schematics of the CIM hierarchy in wafer fab using PC-10 as the equipment controller.
Page 1 of 3
More Columns from Happy’s Tech Talk
Happy’s Tech Talk #40: Factors in PTH Reliability—Hole VoidsHappy’s Tech Talk #39: PCBs Replace Motor Windings
Happy’s Tech Talk #38: Novel Metallization for UHDI
Happy’s Tech Talk #37: New Ultra HDI Materials
Happy’s Tech Talk #36: The LEGO Principle of Optical Assembly
Happy’s Tech Talk #35: Yields March to Design Rules
Happy’s Tech Talk #34: Producibility and Other Pseudo-metrics
Happy’s Tech Talk #33: Wet Process Management and Control