-
- News
- Books
Featured Books
- smt007 Magazine
Latest Issues
Current IssueWhat's Your Sweet Spot?
Are you in a niche that’s growing or shrinking? Is it time to reassess and refocus? We spotlight companies thriving by redefining or reinforcing their niche. What are their insights?
Moving Forward With Confidence
In this issue, we focus on sales and quoting, workforce training, new IPC leadership in the U.S. and Canada, the effects of tariffs, CFX standards, and much more—all designed to provide perspective as you move through the cloud bank of today's shifting economic market.
Intelligent Test and Inspection
Are you ready to explore the cutting-edge advancements shaping the electronics manufacturing industry? The May 2025 issue of SMT007 Magazine is packed with insights, innovations, and expert perspectives that you won’t want to miss.
- Articles
- Columns
- Links
- Media kit
||| MENU - smt007 Magazine
IPC-1782 Standard for Traceability Supporting Counterfeit Components
September 23, 2016 | Michael Ford, Mentor GraphicsEstimated reading time: 4 minutes
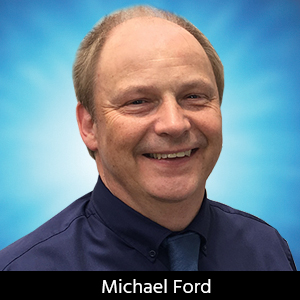
Traceability has grown from being a specialized need for certain safety critical segments of the industry, to now being a recognized value-add tool for the industry as a whole. The perception of traceability data collection however persists as being a burden that may provide value only when the most rare and disastrous of events take place. Disparate standards have evolved in the industry, mainly dictated by large OEM companies in the market create confusion, as a multitude of requirements and definitions proliferate.
The intent of the IPC-1782 project is to bring the whole principle and perception of traceability up to date. Traceability, as defined in this standard will represent the most effective quality tool available, becoming an intrinsic part of best practice operations, with the encouragement of automated data collection from existing manufacturing systems, integrating quality, reliability, predictive (routine, preventative, and corrective) maintenance, throughput, manufacturing, engineering and supply-chain data, reducing cost of ownership as well as ensuring timeliness and accuracy all the way from a finished product back through to the initial materials and granular attributes about the processes along the way.
Having the proper level of traceability will also help ensure counterfeit components do not end up in a product. Through effective policing in the use of any and all components, any material found to be counterfeit will be immediately traceable to source, and hence responsibility is assigned. IPC 1782 will work hand in glove with the U.S. Department of Defense’s current counterfeit component effort.
The goal of this project is to create a single flexible data structure that can be adopted for all levels of traceability that are required across the industry. The scope includes support for the most demanding instances for detail and integrity such as those required by critical safety systems, all the way through to situations where only basic traceability, such as for simple consumer products. A key driver for the adoption of the standard is the ability to find a relevant and achievable level of traceability that exactly meets the requirement following risk assessment of the business.
The wealth of data accessible from traceability for analysis can yield information that can raise expectations of very significant quality and performance improvements, as well as providing the necessary protection against the costs of issues in the market. Taking a graduated approach will enable this standard to succeed where other efforts have failed.
Scope of Standard
This standard establishes the requirements across different scenarios for supply chain traceability based on perceived risk as defined by the Purchaser and Supplier (AABUS). The standard will apply to all critical products, processes, assemblies, parts, components and items as defined by the Purchaser and Supplier of equipment used in the manufacture of printed wiring assemblies, as well as mechanical assemblies.
Traceability is defined as an unbroken record of documentation of materials, parts, assemblies, processes, measurements and associated uncertainties.
Minimum requirements are based on four levels of traceability for materials and processes. These levels correlate to the IPC Product Classification System (Class 1, Class 2, Class 3) and/or another set of categories of compliance (e.g., IPC-2610 Grades A, B and C) based on the business model/economic needs of the end-use market for the final product (telecom, aerospace, automotive, medical device, and/or consumer electronics) or a subassembly within that product.
Purpose of Standard
This traceability information is expected to improve operational efficiency and productivity, quality and reliability as well as enable activities such as predictive maintenance in the manufacturing environment. Current implementations of traceability have typically followed a hazy set of requirements often driven directly between customer and manufacturer for example in an EMS scenario. Requirements are based on quality expectations, limitation of responsibility, and management standards such as those defined by ISO. As such, the current definition of traceability differs from sector to sector, company to company, customer to customer and even from order to order.
Figure 1: Determination of traceability level.
When negotiating the levels of traceability that is required, the key concern is the cost and accuracy of the traceability data collection. When it comes to the need to use the traceability data, the concern is the completeness and accuracy of the data. On many occasions, the data that is needed is found to be omitted from the agreed specification on cost grounds. The feeling for traceability then is a double negative, in that there is cost and effort the collect the data which may end up being useless. The lack of a uniform component traceability standard has caused an unnecessary consumption of resources (e.g., time, people, money, etc.) to track down and remedy any quality, reliability, etc., issue and has made it difficult to uniformly create and appropriately enforce the necessary contracts. IPC-1782 identifies criteria for tracking components on or in a specific assembly and creates a means to specify different levels of traceability to accommodate different economic and business models/needs.
The purpose of the IPC-1782 standard then is two-fold. It sets out the definitive standard to control what data should be collected, and through the standardisation opens up the capability to introduce the automated collection of traceability data from processes that can support it. In so doing, it drives down the cost overhead. With this achievement in place, traceability can then be applied in a broader sense throughout the industry, for example, the application of traceability to counterfeit components in an organization’s supply chain.
This standard helps organizations more easily ensure end-users/consumers will receive products and services that meet or exceed their expectations and in the timeliest and economically viable method.
To read this entire article, which appeared in the September 2016 issue of SMT Magazine, click here.
Suggested Items
S&K Aerospace Awarded Major Contract Under DLA Maritime Acquisition Advancement Program
07/02/2025 | BUSINESS WIRES&K Aerospace, LLC has been awarded a significant contract under the Defense Logistics Agency’s (DLA) Maritime Acquisition Advancement Program, managed by the U.S. Naval Supply Command - Weapon Systems Support (NAVSUP WSS) in Mechanicsburg, PA.
Green Circuits to Exhibit Full-Service Electronics Manufacturing Solutions at 2025 SMD Symposium
07/02/2025 | Green CircuitsGreen Circuits, a full-service Electronics Manufacturing Services (EMS) partner to leading OEMs, is pleased to announce its participation in the 2025 SMD Symposium, taking place August 5-7 at the Von Braun Center in Huntsville, Alabama.
I-Connect007 Editor’s Choice: Five Must-Reads for the Week
06/27/2025 | Nolan Johnson, I-Connect007While news outside our industry keeps our attention occupied, the big news inside the industry is the rechristening of IPC as the Global Electronics Association. My must-reads begins with Marcy LaRont’s exclusive and informative interview with Dr. John Mitchell, president and CEO of the Global Electronics Association. For designers, have we finally reached the point in time where autorouters will fulfill their potential?
Knocking Down the Bone Pile: Tin Whisker Mitigation in Aerospace Applications, Part 3
06/25/2025 | Nash Bell -- Column: Knocking Down the Bone PileTin whiskers are slender, hair-like metallic growths that can develop on the surface of tin-plated electronic components. Typically measuring a few micrometers in diameter and growing several millimeters in length, they form through an electrochemical process influenced by environmental factors such as temperature variations, mechanical or compressive stress, and the aging of solder alloys.
RTX, the Singapore Economic Development Board Sign MOU Outlining 10-year Growth Roadmap
06/20/2025 | RTXRTX and the Singapore Economic Development Board (EDB) have signed a Memorandum of Understanding (MoU) which outlines a 10-year roadmap to further long-term strategic collaboration in Singapore.