-
- News
- Books
Featured Books
- smt007 Magazine
Latest Issues
Current IssueSpotlight on India
We invite you on a virtual tour of India’s thriving ecosystem, guided by the Global Electronics Association’s India office staff, who share their insights into the region’s growth and opportunities.
Supply Chain Strategies
A successful brand is built on strong customer relationships—anchored by a well-orchestrated supply chain at its core. This month, we look at how managing your supply chain directly influences customer perception.
What's Your Sweet Spot?
Are you in a niche that’s growing or shrinking? Is it time to reassess and refocus? We spotlight companies thriving by redefining or reinforcing their niche. What are their insights?
- Articles
- Columns
- Links
- Media kit
||| MENU - smt007 Magazine
Defect Features Detected by Acoustic Emission for Flip-Chip CGA/FCBGA/PBGA/FPBGA Packages and Assemblies
October 11, 2016 | Reza Ghaffarian, Jet Propulsion Laboratory, California Institute of TechnologyEstimated reading time: 4 minutes
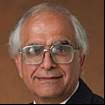
The C-SAM (C-mode scanning acoustic microscopy) is the preferred method for finding "air gaps" such as delamination, cracks, voids, and porosity. This paper presents evaluations performed on various advanced packages/assemblies especially flip-chip die version of ball grid array/column grid array (BGA/CGA) using C-SAM equipment. For comparison, representative X-ray images of the assemblies were also gathered to show key defect detection features of the two non-destructive techniques.
Acoustic Emission Technology
Electronic Packaging Trend
Previous generations of microelectronic packaging technology aimed mostly at meeting the needs of high-reliability applications, such as the ceramic leaded quad flat package (CQFP). Nondestructive wire bond pull at the package level and subsequent visual inspection for solder joint integrity at the board level were adequate for ensuring the quality of CQFPs. Consumer electronics are now driving miniaturization trends for electronic packaging and assembly; they introduce a vast number of area array packages. The array packages initially only had hidden solder joints under the bottom area of the package; now the flip-chip die within package also have hidden joints.
The hidden joints—both at package and assembly levels—added significant challenges to the inspectability and certainty of assuring integrity at the various microelectronics hierarchy levels. Another added complexity is the transition to using only Pb-free solder alloys. Suppliers of electronics packages either have or will soon transition to using Pb-free alloys in order to enforce restrictions on hazardous substances (ROHS) for electronic systems. The solder joint appearance for the Pb-free solder alloys is dull rather than shiny, as it is for the tin-lead eutectic solder, which will add confusion even if visual inspection is used inadvertently as a criterion for the quality of joint acceptance or rejection of a Pb-free solder joint.
Inspection of ball grid array (BGA) and column grid array (CGA) package/assembly, especially their flip-chip versions is challenging1, 2, 3, 4, 5. Nondestructive X-ray inspection became a new approach for ensuring the quality of area array packages and assemblies. Even though X-ray can detect the level of voids and bridges of solder joints hidden under packages, it become of less value for detecting solder attachment and underfill integrity of higher I/O (>1000 I/Os) packages with flip-chip die technology (such as FCBGA and FC-CGA; Figure 1). Ceramic substrates considered for high-reliability applications are heavier and less penetrable to X-ray radiation than plastic, making them even more difficult to inspect for this category of packages and assemblies.
Figure 1: Microelectronic trends for single packaging technologies including flip-chip BGA and CGA.
Acoustic Micro-imaging, C-SAM, and X-ray
Acoustic microscopes emit ultrasounds ranging from 5 MHz to more than 400 MHz, so that micrometer size resolution can be achieved6. Ultrasound that penetrates a sample may be scattered, absorbed or reflected by the internal features of the material itself. These actions are analogous to the behavior of light. Ultrasound that is reflected from an internal feature has traveled through the entire thickness of the sample, and is used to make acoustic images. At least three basic types of acoustic microscope have been developed. These are the scanning acoustic microscope (SAM), scanning laser acoustic microscope (SLAM), and C-mode scanning acoustic microscope (C-SAM).
C-SAM uses the same transducer to pulse ultrasound and receive the return echoes, meaning that the acoustic image can easily be constrained to a depth of interest. It has the ability to create images by generating a pulse of ultrasound focused to a pinpoint spot. The pulse is sent into a sample and reflected off of interfaces. The frequency of the pulse and design of the lens are chosen to optimize spot size resolution and depth penetration for each application. In the reflection mode of operation, the same transducer is used to send and receive the ultrasonic pulse. Return echoes arrive at different times based upon the depth of the reflecting feature and the velocity of sound in the materials. The operator positions an electronic gate to capture the depth of interest. The amount of ultrasound reflected at the interface is based on the differences in the materials at the interface. The more different the materials the more ultrasound reflected.
Similar to X-ray, acoustic microscopy is a non-destructive technique for visualization of defects, widely used in the production of electronic components and assemblies for quality control, reliability and failure analysis. Usually the interest is in finding and analyzing internal defects such as delaminations, cracks and voids, although an acoustic microscope may also be used simply to verify (by material characterization or imaging, or both) that a given part or a given material meets specifications or, in some instances, is not counterfeit. Acoustic microscopes are also used to image printed circuit boards and other assemblies.
The ultrasonic frequencies pulsed into samples by the transducers of acoustic microscopes range from a low of 10 MHz (rarely, 5 MHz) to a high of 400 MHz or more. Across this spectrum of frequencies there is a trade-off of penetration and resolution. Ultrasound at low frequencies (such as 10 MHz) penetrates deeper into materials than ultrasound at higher frequencies, but the spatial resolution of the acoustic image is less. On the other hand, ultrasound at very high frequencies does not penetrate deeply, but provides acoustic images having very high resolution. The frequency chosen to image a particular sample will depend on the geometry of the part and on the types of materials.
To read this entire article, which appeared in the September 2016 issue of SMT Magazine, click here.
Testimonial
"The I-Connect007 team is outstanding—kind, responsive, and a true marketing partner. Their design team created fresh, eye-catching ads, and their editorial support polished our content to let our brand shine. Thank you all! "
Sweeney Ng - CEE PCBSuggested Items
Absolute EMS: The Science of the Perfect Solder Joint
09/05/2025 | Absolute EMS, Inc.Absolute EMS, Inc., a six-time award-winning provider of fast turnaround, turnkey contract electronic manufacturing services (EMS), is drawing attention to the critical role of 3D Solder Paste Inspection (SPI) in ensuring the reliability of both FLEX and rigid printed circuit board assemblies (PCBAs).
Indium Corporation to Highlight High-Reliability Solder Solutions at SMTA Guadalajara Expo
09/04/2025 | Indium CorporationIndium Corporation, a leading materials refiner, smelter, manufacturer, and supplier to the global electronics, semiconductor, thin-film, and thermal management markets, will feature a range of innovative, high-reliability solder products for printed circuit board assembly (PCBA) at the SMTA Guadalajara Expo and Tech Forum, to be held September 17-18 in Guadalajara, Mexico.
Dr. Jennie Hwang to Present on ‘Solder Joint Reliability’ at SMTA International 2025
09/03/2025 | Dr. Jennie HwangDr. Jennie Hwang to address “Solder Joint Reliability” at the 2025 SMTA International Conference on Monday, October 20. Leveraging her decades of extensive real-world experiences and deep knowledge,
Indium to Highlight Energy-Efficient, High-Reliability Solder Solutions for EV and Electronics at Productronica India
09/03/2025 | Indium CorporationIndium Corporation, a leading materials refiner, smelter, manufacturer, and supplier to the global electronics, semiconductor, electric vehicle (EV), thin-film, and thermal management markets, will feature a range of sustainable, high-reliability solder products at Productronica India, to be held September 17-19 in Bengaluru, India.
Altus Supports Datalink Electronics with Advanced Selective Soldering Solution to Boost Manufacturing Efficiency
09/02/2025 | Altus GroupDatalink Electronics has partnered with Altus Group to integrate a cutting-edge automated soldering solution, enhancing its production capabilities and reinforcing its strategic focus on quality, automation, and scalability.