Rogers on the Booming Wireless Infrastructure Market
November 28, 2016 | Barry Matties, I-Connect007Estimated reading time: 8 minutes
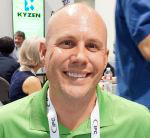
With the advent of 5G and next generation antennas, the already booming wireless infrastructure market is slated for continued growth through 2021, and as the primary material supplier for this sector, Rogers Corp. must continue to meet the technological demands of the Verizons and AT&Ts of world. In an interview with Barry Matties, Tony Mattingly reveals a new antenna grade laminate aimed at doing just that, and he also outlines the unique challenges posed by this thriving marketplace.
Barry Matties: Tony, I know everyone knows Rogers, but just in case they don’t could you give us a little overview?
Tony Mattingly: Rogers Corporation is a circuit board core laminate manufacturer for high-frequency applications. Some of our primary markets are in wireless infrastructure, like base station antennas and power amplifiers, and another is automotive radar systems. Defense and aerospace and high speed digital are markets for us as well, but our biggest markets are in wireless infrastructure.
Matties: That's what your brand is well-known for. When people talk about RF material, they always say Rogers, and they're willing to wait the cycle time to get it in because the OEMs spec it.
Mattingly: Absolutely. Rogers can be referred to as the Cadillac of circuit board materials out there. We've got a really vast portfolio of materials that have consistent and reliable electrical and mechanical properties.
Matties: Now the area we're talking about today is around the antenna area, and you were just telling me about some new specs?
Mattingly: Yes, we just launched a new product about two months ago called RO4730G3™ antenna-grade laminate.
Matties: What makes it an antenna-grade laminate?
Mattingly: It’s the specific dielectric constant and the copper that we use that makes it antenna-grade. The dielectric constant for this material is 3 Dk, which is a very popular and sought after dielectric constant for base station antenna designers. The laminate is built using our patented LoPro copper foil, which is required for good passive intermodulation. In the base station antenna world, passive intermodulation is a critical thing and a parameter that carriers like Verizon and AT&T specify. For example, the antennas need to perform at a negative 153 dBc or better. For passive modulation, the lower the number the better, and RO4730G3 material typically runs around −160 dBc or better.
Matties: Wow, so the market is huge.
Mattingly: Very huge.
Matties: And still growing, right? Especially with the RF market being so explosive.
Mattingly: Absolutely. Demand for mobile data has been growing at around a 53% CAGR year over year. That's going to continue through 2021 and this has put a lot of strain on the infrastructure that's already in place. Carriers are forced to add performance and capacity. A couple of ways they're doing that is through cell densification, like deploying small cells throughout a crowded area. Another way that they're doing that is by replacing some of the existing antennas on the macro base station towers with ones that are more complex yet add capacity, such as active antenna systems and what they call MIMO antennas, which is multiple input multiple output antennas.
Matties: When you look at the market, how do you make your projections and what do you see?
Mattingly: Maybe two to three years ago the most explosive growth was in South Korea and Japan. Last year it was China, which we’re starting to see growth in again. India is where a lot of the demand is today. The globe is just changing, right? More and more people want smartphones and inherent technology. Demand for video will account for 75% of mobile data by 2020. With 5G coming and the infrastructure required to support it we can anticipate explosive demand for our materials. Europe, North America, and South Korea will most likely be the first going to 5G.
Matties: How do you service that? You mentioned India, do you already have infrastructure in place to take care of those markets or what's that process like?
Mattingly: We have manufacturing sites in North America, in Suzhou, China, and in Belgium. Those sites supply the global demand. Additionally, we have a network of support made up of sales engineers, technical service engineers, and application development managers, and others, spread across the world, and in most cases local to our customer base.
Matties: You have enough capacity then? Because at one point the delivery time of your products was quite bad.
Mattingly: A couple of years ago it was.
Matties: With all this added growth, do you have enough capacity to handle that as well?
Mattingly: We do. There were a lot of capital expenditures over the past recent years to add capacity in our manufacturing facilities, such as installing additional lamination presses, for example. We’ve also qualified several product lines in some of our other manufacturing sites. That provides us the ability to run more efficiently and level load our factories when necessary.
Matties: From a designer's point of view, they don't care about the material because it's being spec’d in, right? Or is there an impact for the designer when they're designing a board?
Mattingly: We have direct customers, which are the fabricators, and we have indirect customers, which would be the designers, or OEMS. When you say that they don't care because it's spec’d in, that would be in most cases the direct customers or the fabricators. If the OEM is specifying a material then the fabricator would need to use our material.
Matties: In some cases do you have an OEM and then maybe a design house in-between, where a fabricator or the designer of the circuit may not be embedded in the OEM?
Mattingly: Yeah, there are design centers that can specify materials and feed the OEM the requirements. Those requirements will funnel down to the fabricator, and the demand then comes to us. We work very closely with each of those levels. Base station antenna is a little different than, let's say automotive, in that numerous materials may be specified and the decision is up to the fabricator to choose between them. In those cases we are in direct competition with other laminate suppliers that could threaten our share of the business for reasons such as supply, not just how the material performs out in the field.
Matties: Now from a technology point of view this material is for base station antennas, but will this be used in other markets like automotive as well? Or do you have other products that suit that?
Mattingly: We're really positioning this material for the base station antenna market. For automotive, we've got specific products more closely aligned with market needs that Rogers has or will launch.
Matties: That's a booming market as well, because these cars are turning into rolling computers.
Mattingly: Oh, absolutely. I was actually in the new Tesla not too long ago. It was pretty neat. The driver put the car in auto pilot and it made me nervous at first because I wanted to grab the wheel, but the car did well.
Matties: It's an exciting time to be in the electronics industry, that's for sure, with all the things that are going on. What challenges do you think the industry faces when it comes to materials?
Mattingly: For, let's say, antenna grade materials with the changing antenna designs, they're becoming more complex and multilayer board requirements are starting to increase. The challenges that many designers are facing today, if they're historically using a PTFE product for example, is that going to a multilayer board construction is quite costly on a PTFE-based material. There are not a whole lot of thermoset options out there that are 3 DK, low PIM, low loss and flame retardant.
Matties: All big issues.
Mattingly: Another thing that's becoming more of a need is a UL-rated material. A lot of these antennas are going on residential buildings or where flame retardant materials are mandated, and the RO4730G3 meets those needs. That's why we are expecting a lot of success with this material. It's a thermoset laminate that can easily be designed into a multilayer board construction and is a UL rated product.
Matties: It’s been out for two months you said, and how have sales been?
Mattingly: Good. We’ve had a very, very positive response from customers. There's already a large OEM in China that has adopted it and is using it for active antenna systems. There are numerous other OEMs that are sampling the material as well so we hope to have some more design wins soon.
Matties: That's really the challenge when you bring out a new product like this is to get the OEMs to approve it and spec it. How long does the cycle typically take for that?
Mattingly: It depends on how motivated they are. (Laughs)
Matties: Isn't it based on product performance, where there’s enough value for them to say, "Oh we need to do this?"
Mattingly: Yeah, it's cost and performance. Those are the things that drive the decisions, and ultimately, change. Cost is huge. It's a very competitive market for our customers; they're all under immense pressure to have the lowest cost antennas out there that also deliver performance and reliability.
Matties: I know Rogers isn't always the cheapest of materials, how are you coming in on the price point with this line?
Mattingly: Good. The pricing seems to be attractive to our customers. This material is an optimum blend of price, performance, and durability. RO4730G3 laminate is a very low loss material with consistent electrical-mechanical properties and it's a cheaper overall solution than PTFE multilayer board builds.
Matties: This kind of innovation is what will keep us going, and when you start looking at the wireless market, it's just everywhere. The new Apple headphones are wireless. Everything is just going to be wireless. It's crazy how big this market will continue to be.
Mattingly: The whole 5G thing will mean you have billions of devices talking to each other as well.
Matties: Tony, thank you so much for spending time with us. It’s been a pleasure.
Mattingly: Of course, thank you.
Testimonial
"Our marketing partnership with I-Connect007 is already delivering. Just a day after our press release went live, we received a direct inquiry about our updated products!"
Rachael Temple - AlltematedSuggested Items
How Good Design Enables Sustainable PCBs
08/21/2025 | Gerry Partida, Summit InterconnectSustainability has become a key focus for PCB companies seeking to reduce waste, conserve energy, and optimize resources. While many discussions on sustainability center around materials or energy-efficient processes, PCB design is an often overlooked factor that lies at the heart of manufacturing. Good design practices, especially those based on established IPC standards, play a central role in enabling sustainable PCB production. By ensuring designs are manufacturable and reliable, engineers can significantly reduce the environmental impact of their products.
50% Copper Tariffs, 100% Chip Uncertainty, and a Truce
08/19/2025 | Andy Shaughnessy, I-Connect007If you’re like me, tariffs were not on your radar screen until a few months ago, but now political rhetoric has turned to presidential action. Tariffs are front-page news with major developments coming directly from the Oval Office. These are not typical times. President Donald Trump campaigned on tariff reform, and he’s now busy revamping America’s tariff policy.
Global PCB Connections: Understanding the General Fabrication Process—A Designer’s Hidden Advantage
08/14/2025 | Markus Voeltz -- Column: Global PCB ConnectionsDesigners don’t need to become fabricators, but understanding the basics of PCB fabrication can save you time, money, and frustration. The more you understand what’s happening on the shop floor, the better you’ll be able to prevent downstream issues. As you move into more advanced designs like HDI, flex circuits, stacked vias, and embedded components, this foundational knowledge becomes even more critical. Remember: the fabricator is your partner.
MKS’ Atotech to Participate in IPCA Electronics Expo 2025
08/11/2025 | AtotechMKS Inc., a global provider of enabling technologies that transform our world, announced that its strategic brands ESI® (laser systems) and Atotech® (process chemicals, equipment, software, and services) will showcase their latest range of leading manufacturing solutions for printed circuit board (PCB) and package substrate manufacturing at the upcoming 17th IPCA Show to be held at Pragati Maidan, New Delhi from August 21-23, 2025.
MKS Showcases Next-generation PCB Manufacturing Solutions at the Thailand Electronics Circuit Asia 2025
08/06/2025 | MKS Instruments, Inc.MKS Inc, a global provider of enabling technologies that transform our world, today announced its participation in Thailand Electronics Circuit Asia 2025 (THECA 2025), taking place August 20–22 at BITEC in Bangkok.