-
- News
- Books
Featured Books
- smt007 Magazine
Latest Issues
Current IssueSupply Chain Strategies
A successful brand is built on strong customer relationships—anchored by a well-orchestrated supply chain at its core. This month, we look at how managing your supply chain directly influences customer perception.
What's Your Sweet Spot?
Are you in a niche that’s growing or shrinking? Is it time to reassess and refocus? We spotlight companies thriving by redefining or reinforcing their niche. What are their insights?
Moving Forward With Confidence
In this issue, we focus on sales and quoting, workforce training, new IPC leadership in the U.S. and Canada, the effects of tariffs, CFX standards, and much more—all designed to provide perspective as you move through the cloud bank of today's shifting economic market.
- Articles
- Columns
- Links
- Media kit
||| MENU - smt007 Magazine
Living Up to Their Name at Alpha Assembly Solutions
November 18, 2016 | Judy Warner, I-Connect007Estimated reading time: 11 minutes
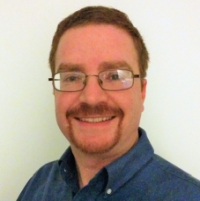
At SMTAI in October, I spent some quality time with Alpha Assembly Solutions' Jason Fullerton, who caught me up on Alpha's innovative new products. He also discussed a paper he was presenting, which compares two lead-free, silver-free alloys in a selective soldering application.
Judy Warner: Jason, it's good to see you.
Jason Fullerton: Thanks for having me.
Warner: What's new with Alpha? Are you exhibiting here?
Fullerton: We have a booth here and we're exhibiting on the assembly solution side. We have a couple of our newer products out to demonstrate and show to people. We also have some display information about our reclaim service where we take and refine solder waste and dross and turn that back into virgin metals, which gives some value to our customers. We pay them for the material. So we're turning their waste into value again, and they get reimbursed for that.
Our assembly customers, who can't do anything with the waste materials, pay companies to come in and take it away, especially the leaded materials because they're hazardous. We'll take it away, refine them back into virgin raw materials and then we'll pay them for the value of material recovered from that waste.
Warner: Wherever we can recoup some margin, right? That's great. What other products are you featuring here that you're sort of showing off?
Fullerton: We have two new products we introduced in the last year. One is a new variant of one of our cored wires. We have a cored wire called HF-850 and it's been available for a couple years now in a couple different alloys. It's in tin-lead and SAC lead-free, but we just introduced that into our silver-free, lead-free alloy. That's a new product for those who are concerned about cost, because the silver content in the alloy can drive up cost in the wire. It's really advantageous for people that are building low-cost products. It's also advantageous for people that are already using a silver-free alloy in their soldering processes. They can rework it with another low-cost alloy instead of having to use a silver-based alloy.
We also have a new flux gel material called HF-1 that we've introduced recently. That's a flux gel that's designed to be used in conjunction with other assembling materials such as SMT solder paste residues, wave solder fluxes, and cored wire fluxes. It can be used in conjunction with those for the rework processes without sacrificing anything on the reliability side. We've done some comparison testing and combinational testing of a variety and suite of materials for all the potential processes that could be applied to a circuit board with this material used on top of that to demonstrate the reliability is still there even when you use this secondary material.
Warner: Reliability obviously is a huge deal, especially on the mil/aero and medical side. It's becoming increasingly important across the board. Do you see that in your customer base?
Fullerton: Well, reliability has always been a key focus for our company. We recognize that the key to success for our customers is not simply providing the right material for the right problem today, but being able to put that into their product and service environments that can last as long as the customers need. We've been very strong in the military market, historically. We've been very strong in the automotive market as well. Those markets drive us to design products with the utmost reliability, both from the metal side and from the chemical side. In order to play in this market you have to have high-reliability products and those benefits trickle down to our customers that may not be as concerned or maybe aren’t sophisticated enough to test all of those aspects. They can be very confident in the materials we are selling.
Warner: I would think that would be a key asset to working with you, right? Is that trickledown effect and supporting high-reliability applications impacting all the products you support?
Fullerton: Absolutely. One of key core policies is in the strength of our technical service both from the R&D stand point, designing materials that meet today's challenges and future challenges, as well as our application support out in the field with a customer technical support (CTS) group that I'm a part of. We have five people in North America that are solely dedicated to working with our customers troubleshooting application problems, helping them select the right materials, identifying the key factors in their process and choosing the materials that are appropriate for those applications. It differentiates us from some of our other competitors that don't have such a strong R&D and technical side to them. All of these services come included in the price of business with us. If you're an Alpha customer, you have access to our CTS field service group that I'm a part of, as part of being a customer.
Warner: That's fabulous. Nothing beats a good technical marketing guy in your back pocket, right?
Fullerton: Absolutely, and I'm not even marketing. There are actually a couple differences. Technical marketing people tend to be more about how to market the products and explain the technical aspects. My job is to delve down into the actual applications and ensure I understand what our customers' challenges are, how to meet those challenges and how to help them recover in situations where they may have problems that are affecting their ability to meet their own challenges for their customer base. Our marketing people are very technical. Our field sales people are very technical. Obviously, our CTS and R&D groups are very technical. All around, our whole organization is full of technical people in different roles.
Warner: That's really unique.
Fullerton: It's one of the things that differentiates us from competitors in our field.
Warner: You have that full technical spectrum, which helps you to come along side and be a true partner I’d imagine.
Fullerton: Right. That's the way we look at it. We are partners with our customers, and when they are customers are successful, we're successful. We see that as our path toward success. We're not just trying to sell someone material and then walk away and wish them luck. We're going to have them pick the right material, help them implement the material, and help decide if what they're doing is the right thing to do with the materials we provided them. If not, then find the right material for the job or find the right way to process that material properly.
Warner: What do you see as the pain points in the EMS/CM industry as far as the different applications and how Alpha is specifically helping to stand in the gap with EMS companies?
Fullerton: One of the big challenges of EMS companies is they have a very high mix of product base because they have a large suite of customers, as opposed to an OEM that makes the same board all the time every day. In that field, they have different applications, different products and different challenges. We help them identify the right tool for the job when they try to meet those different challenges for their widely varied customer base. On top of that, EMS companies are in a very competitive market. They have to be cross competitive and provide quality and value to customers. We try to support our EMS customers in the same way. We may not be selling solely on price, but we look at the overall value and value in the process so that if there are problems that can be solved with the material, a small increment of cost in the material may reap big ROI on the back end when they reduce their manufacturing cost. That's where the big opportunities lie and that's how they remain competitive against their own competition in their field.
Everybody has SMT and wave solders and so on. We all have the same capabilities, but it's how you apply the abilities and how you choose your materials that ensures you're meeting your own customers’ objectives.
Page 1 of 2
Testimonial
"The I-Connect007 team is outstanding—kind, responsive, and a true marketing partner. Their design team created fresh, eye-catching ads, and their editorial support polished our content to let our brand shine. Thank you all! "
Sweeney Ng - CEE PCBSuggested Items
MacDermid Alpha Electronics Solutions Unveils Unified Global Website to Deepen Customer, Talent, and Stakeholder Engagement
07/31/2025 | MacDermid Alpha Electronics SolutionsMacDermid Alpha Electronics Solutions, the electronics business of Elements Solutions Inc, today launched macdermidalpha.com - a unified global website built to deepen digital engagement. The launch marks a significant milestone in the business’ ongoing commitment to delivering more meaningful, interactive, and impactful experiences for its customers, talent, and stakeholders worldwide.
KOKI to Showcase Analytical Services and New HF1200 Solder Paste at SMTA Guadalajara 2025
07/31/2025 | KOKIKOKI, a global leader in advanced soldering materials and process optimization services, will exhibit at the SMTA Guadalajara Expo & Tech Forum, taking place September 17 & 18, 2025 at Expo Guadalajara, Salón Jalisco Halls D & E in Guadalajara, Mexico.
Weller Tools Supports Future Talent with Exclusive Donation to SMTA Michigan Student Soldering Competition
07/23/2025 | Weller ToolsWeller Tools, the industry leader in hand soldering solutions, is proud to announce its support of the upcoming SMTA Michigan Expo & Tech Forum by donating a limited-edition 80th Anniversary Black Soldering Set to the event’s student soldering competition.
Koh Young Appoints Tom Hattori as President of Koh Young Japan
07/21/2025 | Koh YoungKoh Young Technology, the global leader in True 3D measurement-based inspection solutions, announced the appointment of Tom Hattori as President of Koh Young Japan (JKY).
Silicon Mountain Contract Services Enhances SMT Capabilities with New HELLER Reflow Oven
07/17/2025 | Silicon Mountain Contract ServicesSilicon Mountain Contract Services, a leading provider of custom electronics manufacturing solutions, is proud to announce a significant upgrade to its SMT production capability with the addition of a HELLER 2043 MK5 10‑zone reflow oven to its Nampa facility.