-
- News
- Books
Featured Books
- pcb007 Magazine
Latest Issues
Current IssueInventing the Future with SEL
Two years after launching its state-of-the-art PCB facility, SEL shares lessons in vision, execution, and innovation, plus insights from industry icons and technology leaders shaping the future of PCB fabrication.
Sales: From Pitch to PO
From the first cold call to finally receiving that first purchase order, the July PCB007 Magazine breaks down some critical parts of the sales stack. To up your sales game, read on!
The Hole Truth: Via Integrity in an HDI World
From the drilled hole to registration across multiple sequential lamination cycles, to the quality of your copper plating, via reliability in an HDI world is becoming an ever-greater challenge. This month we look at “The Hole Truth,” from creating the “perfect” via to how you can assure via quality and reliability, the first time, every time.
- Articles
- Columns
- Links
- Media kit
||| MENU - pcb007 Magazine
Estimated reading time: 4 minutes
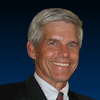
All About Flex: Packaging Flexible Circuits and Assemblies
There are many facets involved in designing, fabricating and delivering a flexible circuit. During the quote and design phase, requirements are reviewed relating to the function, reliability and dimensions of the flex circuit. So assuming the relevant product documentation was gathered, the salesperson turned around the quote, and the customer placed an order and parts were built, it’s all over, right? Not quite. One critical aspect that often does not get much discussion until there is a problem is packaging and shipping.
Packaging and shipping is usually taken for granted, yet if the flexible circuits are damaged or misrouted, the end-result is the same as not shipping the product.
The key function of packaging and shipping is to deliver the product to the correct location without damage. Taking the proper steps to package the product and ensure an “event-free” shipment is just as important as any other circuit fabrication step. The following are some considerations for packaging a flex circuit product.
Labeling
Correct transit will only result if the package is accurately labeled. This minimally consists of the part number and the quantity. In some cases, the customer may require the manufacturer’s Commercial and Government Entity Code (CAGE Code), shipping date and the customer PO number along with other information. The location of the label on the package is also important so the carrier’s labeling does not cover the circuit fabricator’s label. The carrier must know where to deliver the product. A package that arrives at the customer’s dock without proper labeling will cause delays, added cost, and perhaps a black mark on a supplier’s performance scorecard.
Corrosion Protection
The degree to which a flexible circuit is susceptible to corrosion depends on the surface finish and components assembled to it. Many customers request some degree of corrosion protection as part of the packaging. Products can be sealed in moisture-proof bags with a desiccant pouch to inhibit moisture build-up. Desiccants consist of silica that readily absorbs moisture and thereby keeps the product dry. Desiccants are effective for most packaging situations since moisture is the main catalyst for corrosion. VpCI or vapor pressure corrosion inhibitors will emit protective vapors inside a package and are added for corrosion protection. The vapors consist of ions that attach to metal surfaces and form a corrosion inhibiting layer. There are corrosion inhibiting products specifically designed for sensitive electronics, including implantable medical applications.
ESD Protection
It is a standard packaging practice for circuit fabricators to use moisture-proof ESD bags with conductive surfaces for packaging flexible circuits, especially when parts are shipped with populated and ESD sensitive components. A metalized or conductive surface will help prevent ionic build-up that could result in a static discharge when the package is handled or open.
Physical Damage
The risk of mechanical damage during shipment is dependent on the fragility of the components and the configuration, size, and shape of the flexible circuit or flexible circuit assembly. Sometimes enclosing the circuit or stack of circuits in a properly sized poly bag is all that is needed to assure damage free shipments. In other cases, the use of low density foam pouches or bubble wrap is needed to protect the part.
Another option for damage protection is to ship circuits in specially molded packaging trays. These trays are designed to tightly hold the flexible circuit assembly in place during shipment and storage. Caution with customized packaging is required as bulky containers may result in inordinately high shipment costs. Paying to ship a lot of air can generally be avoided with thoughtful packaging design.
Special molded or formed packaging trays can enhance productivity when parts are properly presented to subsequent assembly processing. Small, thin and unusual shaped flexible circuits can introduce added labor when wrapped in a poly bag as un-packaging can be cumbersome. Parts neatly stacked in a tray can improve the material handling efficiency at the customer’s location. Trays might also be designed in conjunction with automated handling equipment.
Many times, flexible circuits remain in a panel form where partially cut and scored circuits are held in place with small notches that allow for easy removal after multiple-up assembly. In other situations, a low tack film can be laminated to the panel allowing mass depaneling of the circuits onto a clean poly film with parts precisely positioned for handling by the end customer or contract assembler.
Customers may desire to monitor the environment and handling a package has endured during shipping. There are a variety of handling indicators and monitors to signify if the product was exposed to excess moisture, temperature extremes, vibration or impact. Many of these products are threshold indicators. For example, a humidity coupon will have dots that change color when the moisture level exceeds a certain level. Some of the more sophisticated monitors will provide actual data over time, so it can be determined when and for how long a product was exposed to a certain condition. Flexible circuits usually stand up very well to temperature extremes seen during shipping, high impact, or even extreme humidity. However, in cases when sensitive components have been assembled to the circuit, extra handling precautions can be a requirement.
Packaging and shipping requirements are rarely discussed in the design phase, but being proactive in the determination of the packaging requirements can help prevent shipping damage or delays and ultimately save time and money. Getting the paperwork and packaging right seems like a simple task, especially compared to building an 8-layer, fine line, buried via, flexible circuit. It does seem so. But as I was once told, “It is difficult to make things fool-proof because fools are so ingenuous.” Enough said.
Dave Becker is vice president of sales and marketing at All Flex Flexible Circuits LLC.
More Columns from All About Flex
All About Flex: Terms and ConditionsAll About Flex: ISO 9001 Basics
All About Flex: FAQs on UL Listings for Flexible Circuits
All About Flex: Avoiding Trace Fracturing in a Flexible Circuit
Polyimide vs. Silicone for Flexible Heaters
All About Flex: Copper Thickness Requirements for Flex Circuits
All About Flex: Copper Grain Direction
All About Flex: Options for Purchasing Flexible Heaters