-
- News
- Books
Featured Books
- smt007 Magazine
Latest Issues
Current IssueIntelligent Test and Inspection
Are you ready to explore the cutting-edge advancements shaping the electronics manufacturing industry? The May 2025 issue of SMT007 Magazine is packed with insights, innovations, and expert perspectives that you won’t want to miss.
Do You Have X-ray Vision?
Has X-ray’s time finally come in electronics manufacturing? Join us in this issue of SMT007 Magazine, where we answer this question and others to bring more efficiency to your bottom line.
IPC APEX EXPO 2025: A Preview
It’s that time again. If you’re going to Anaheim for IPC APEX EXPO 2025, we’ll see you there. In the meantime, consider this issue of SMT007 Magazine to be your golden ticket to planning the show.
- Articles
- Columns
Search Console
- Links
- Media kit
||| MENU - smt007 Magazine
SMTA Tech Expo Panel Session: It Takes a Village to Discuss Proper Cleaning Solutions
December 6, 2016 | Judy Warner, I-Connect007Estimated reading time: 23 minutes
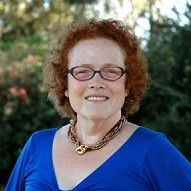
Recently, I attended the SMTA Tech Expo in Long Beach, California. I was delighted to meet with the unflappable Barbara Kanegsberg, of BFK Solutions Consulting. An expert in cleaning processes, Barbara is also known as “The Cleaning Lady.” She moderated a group of panelists for a technical session entitled “Ask the Experts: Meeting the Challenges of Effective Cleaning, Defluxing in Southern California.” Here Barbara discusses the myriad of challenges regarding cleaning PCBs (particularly in the heavily regulated state of California) and what transpired during the open forum technical session.
Judy Warner: Barbara, it’s a pleasure to be with you. I understand that you hosted a technical panel session today. Tell me a little bit about yourself and the members who were on your panel today.
Barbara Kanegsberg: Absolutely. We did a totally unscripted “ask the experts” panel. What I love about this format is that it's not death by PowerPoint. It's focused on the audience and the questions that they have about manufacturing, the challenges that they have, and not what I think I want to tell them, or any of the other panelists.
For panelists, we had Gilbert Roberge from Inventec Performance Chemicals, Julie Fields from Technical Devices, Paul Petruna from Sirco Industrial, and Naveen Ravindran from ZESTRON High Precision Cleaning. Basically, what we had were people representing manufacturers of cleaning agents, cleaning equipment, fluxes, water purification systems, etc. It's a lot of what people need to know about in California, where we have very strict air regulations and do very high-end manufacturing.
We asked people to bring their questions about cleaning, minimizing costs, maximizing quality, avoiding regulatory hassles, and we just introduced everybody and got right to it. There were a lot of good questions. Globally, we have issues in electronics assembly of miniaturization and population of the electronics assemblies, high-end performance requirements, and increasing environmental regulations. What I was impressed with in this particular program is that there were many, many questions about how to get the board assembled technically and how to do a good job in the assembly. I think one question, if I could paraphrase it, discussed the issue of meeting customer requirements which were above and beyond the usual test requirements.
Warner: When you say test requirements. does that include IPC standards that are in place, or do you mean issues that exceed the standards that are in place?
Kanegsberg: Actually, you have it there, Judy. They're exceeding IPC's standards, and there are standards that we may not have thought about classically at IPC. I've been involved in helping to put together the cleaning and coating handbook, so I realized that there were so many issues even a few years ago. Those issues have only grown.
Warner: Do you think that is because of miniaturization? My understanding is that miniaturization and the failure to get boards pristinely clean at the micron level can cause issues, right?
Kanegsberg: You can have all kinds of issues. Let's start with soil. Soil is matter out of place. It's often stuff that we needed for manufacturing, but we don't want to have in the final product. In the case of electronics assembly, the first thing everyone thinks about is flux. You want the flux to either go away or be encapsulated in a form that it doesn't interfere anymore. Critical cleaning is removing matter out of place in the right way at the right point in the process. With electronics assemblies if we just consider standoff, when you get below I would say three to 5 mil standoffs, there will be cleaning problems. That has to do with the chemistry and physics of molecules, cleaning agents, and soils.
If you have closely spaced components, it's very hard to get wettability and to get the cleaning agents in contact with the soil so that the soil can be removed. You have these very small, densely populated assemblies, and you have customers that are using those assemblies in ways that maybe the suppliers never anticipated and maybe the IPC never planned for.
Warner: Let's talk about what some of those applications are, because technology waits for no one. Are we talking military, medical, RF? Are we talking applications with heat or thermal concerns? What stressors and what applications are really driving these issues?
Kanegsberg: We see a lot of applications in military/aerospace, NASA, medical devices, and sensors.
Sometimes the client explains that the customer rejects the product even though the standards have been met. Classically in IPC the issue is ionics. We don't want ionics, that's obvious. What we're gradually realizing is that residues of concern are not just ionics. For example, residue of metal working fluid and residue of particles can interfere with the performance of the assembly. Sometimes there's a problem right away and the assembly is rejected. That’s annoying. However, what’s worse is when you see the problem later. Depending on the product, field failures can be catastrophic.
Warner: So, what do we need to do in testing?
Kanegsberg: That's the challenge. We can do ionics testing on the electronics assembly. We can look at the electronics assembly using ion chromatography. Are those the right tests? It depends on the how the final product is used. The electronics assembly is usually not an end in itself; the assembly goes into the final product. Selecting the right tests depends on what soils can damage the final product. In addition to ionic contamination, you can have non-ionic or fat-like contamination. You might have particles. Contamination can lead to all sorts of performance problems. For example, suppose you have non-ionic contamination or particles and then do conformal coating. If you have a high-value product or a product that has to last a long time, even non-ionic contamination or particles can spell trouble. The conformal coating protects the electronics from the outside environment, but it also traps residual soil. Soil that’s trapped under the conformal coating can damage the assembly and compromise product performance. So back to testing. The tests depend on what the customer needs. Maybe at IPC we need to take a fresh look at application-specific requirements.
Warner: Let’s get back to the panel discussion. What other questions did you get?
Kanegsberg: People asked about how to save money on cleaning equipment. My answer was that the best way to save money on cleaning equipment was to purchase quality equipment. Several of the panelists expressed similar sentiments.
Another questioned complained that the company had purchased cleaning equipment that was supposed to be good enough, and it wasn't. One panelist opined that, in the future, testing the equipment before purchasing could be time well spent. Other suggestions included modifying the fixturing and perhaps adding another dryer. It becomes a matter of optimizing and managing the cleaning system.
I thought the question about drying was interesting; and the answer involves purchasing the correct quality of cleaning equipment. In cleaning, be it water-based or organic solvent-based cleaning, you have washing, rinsing, and drying. It's just like when you take a shower only it's an electronics assembly. When you wash, you bring the cleaning agent, the cleaning chemistry, in contact with the part. You remove the soil, and keep it away from the part. When you rinse, you remove the cleaning agent. When you dry, you remove the residual water or solvent. I’ve noticed that some manufacturers sort of run out of steam in terms of process design and money for capital equipment when they get to the drying step.
Several people asked the panel about the right water quality for the process. Water quality is important. Generally, tap water is not good enough. I
Warner: Well, isn't that why most cleaning systems use deionized water? I thought removing ions was a good thing.
Kanegsberg: Deionized water contains very few ions, so that's the point. You want the deionized water in one sense. You must have clean water to achieve good cleaning, but if you have total deionized water that water is looking for ions. Where is it going to find the ions? From the part you're trying to clean. That can then cause destructive surface modification.
Warner: What else did they ask about?
Kanegsberg: People asked questions about using organic acid flux versus no clean. That's a complex answer. It depends on what you're trying to accomplish, on what kind of assembly you are working with, and on the soldering process. All fluxes leave some sort of residue; no clean means low residue. Sometimes, you have to remove the residue left by no-clean fluxes. OA flux can be rinsed with water, but the OA residue tends to be more active. So, in hand-soldering work or under close spacing, you must plan the flux removal process carefully.
Warner: How refreshing it must have been for the attendees to go into a technical session and participate in a conversation with experts, that directly addressed their real-world concerns.
Kanegsberg: I think they enjoyed it, because the lunch was set out, and no one left! I kept saying, "Would people like to leave and go get some food?" They didn't want to leave. I finally said, "Go away and have lunch!" That was really refreshing. We live in an age of not communicating, but pontificating. I speak a lot. Sometimes improv is the right way to go. I love it. I personally like it because it's a great way to find out what people are interested in, which is not necessarily what we the panelists want to talk about.
We're consultants. BFK Solutions is a consulting company, and we help people either fix, improve, or setup better and more effective cleaning processes. One that lets them make high quality product and make lots of money. That's how we get paid. But we also teach. We do a lot of courses both for individual clients and sometimes for professional conferences and professional programs, that kind of thing. It's nice to know what people want to learn instead of just guessing what they want. The spontaneity of just having the audience speak up is fun. I think in this election year I was really happy that everyone was very well behaved. That was a relief.
Warner: Yes, because the EPA issues here in California can be a chokehold for EMS companies to sort out, right?
Kanegsberg: I would be really happy to do an entire separate interview with you at another point other than to say yes, you're absolutely right. Certainly, it's very confusing, and each air district uses its own approach to regulation. I must say that's always bothered me, because we all live in the same world, so I would love to see more standardization.
Warner: Wouldn’t that be nice? Going back to current market conditions, in the electronics manufacturing industry we see increasing demand for complexity and reliability from OEMs with a concurrent demand to lower costs. I assume you see that as well?
Kanegsberg: Of course.
Warner: From a cleaning standpoint, how do you encourage manufacturers to buy the best equipment when you know that they're being so hard pressed from their customers to keep their costs down? There's a huge tension there.
Kanegsberg: That's a great question Judy. There is immense tension associated with equipment selection. In fact, there were quite a few questions for the panel about cleaning equipment costs. We ended up discussing cleaning process costs. It gets into issues of the cleaning agent, filtration, waste disposal, management, permitting and so on. It's quite complex.
Clients often ask me how to get really cheap cleaning equipment and the best way to do a really cheap process. I always just say buy quality, and they usually open their eyes and they're skeptical, but they're generally pretty accepting of it. I should add by the way that we're not reps, so we don't do commissions or fees.
Warner: Meaning you don't have a stake in the advice you’re giving?
Kanegsberg: Well we don't do consultant appreciation day and all that stuff, but we accept lattes and we treat people to lattes.
Because the client pays us, we don’t necessarily aim at recommending more and more cleaning. For example, one client was able to get away from doing very much cleaning in their own plant because they were able to verify that their supplier gave the assemblies to them in a condition that was clean enough for their application. They didn’t need the cleaning machine or the fairly expensive cleaning solvent; and they could avoid the costly environmental permits. Is that talking us out of a job? Sure, but that's okay. The goal is not to keep cleaning for its own sake, but to do critical cleaning, which is the right amount of cleaning in the right place at the right parts of the process.
Page 1 of 2
Suggested Items
From DuPont to Qnity: A Bold Move in Electronics Materials
05/14/2025 | Marcy LaRont, I-Connect007DuPont has announced the intended spinoff of a public independent electronics company, Qnity, which will serve as a solutions provider to the semiconductor and electronics industries to enhance competitiveness and innovation in advanced computing, smart technologies, and connectivity.In this interview, Jon Kemp, Qnity CEO-elect and current president of DuPont’s Electronics business, shares his insights on the strategic separation from DuPont.
Legislative Update – The SEMI Investment Act: Inclusive of PCB and Substrates?
05/13/2025 | I-Connect007 Editorial TeamIn response to yesterday’s news around new U.S. legislation being put forth by SEMI to support our domestic electronics supply chain–The SEMI Investment Act, or the Strengthening Essential Manufacturing and Industrial Act– I reached out to IPC’s Richard Capetto, chief lobbyist and a principal member of IPCs Global Relations and Advocacy team.
The Test Connection Inc. Appoints USM Reps as Exclusive Sales Representative in Mexico
05/13/2025 | The Test Connection Inc.The Test Connection Inc. (TTCI), a leading provider of electronic test and manufacturing solutions, is pleased to announce the appointment of USM Reps as its exclusive sales representative in Mexico.
Top 10 OSAT Companies of 2024 Revealed—China Players See Double-Digit Growth, Reshaping the Global Market Landscape
05/13/2025 | TrendForceTrendForce’s latest report on the semiconductor packaging and testing (OSAT) sector reveals that the global OSAT industry in 2024 faced dual challenges from accelerating technological advancements and ongoing industry consolidation.
Delta Builds First IPC-CFX Demonstration Line in Asia-Pacific
05/14/2025 | Chuck Li, IPC North AsiaAs a key standard in the global electronics manufacturing industry, IPC-CFX has been implemented in various regions worldwide, providing the foundation for digital factory solutions. In the Asia-Pacific region, IPC actively promotes this standard, helping enterprises enhance efficiency and competitiveness through digital transformation.