-
- News
- Books
Featured Books
- smt007 Magazine
Latest Issues
Current IssueSpotlight on India
We invite you on a virtual tour of India’s thriving ecosystem, guided by the Global Electronics Association’s India office staff, who share their insights into the region’s growth and opportunities.
Supply Chain Strategies
A successful brand is built on strong customer relationships—anchored by a well-orchestrated supply chain at its core. This month, we look at how managing your supply chain directly influences customer perception.
What's Your Sweet Spot?
Are you in a niche that’s growing or shrinking? Is it time to reassess and refocus? We spotlight companies thriving by redefining or reinforcing their niche. What are their insights?
- Articles
- Columns
- Links
- Media kit
||| MENU - smt007 Magazine
Estimated reading time: 7 minutes
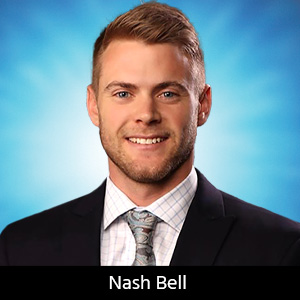
Knocking Down the Bone Pile: Gold Mitigation for Class 2 Electronics
In electronic assemblies, the integrity of connections between components is paramount for ensuring reliability and performance. Gold embrittlement and dissolution are two critical phenomena that can compromise this integrity. Gold embrittlement occurs when gold diffuses into solder joints or alloys, resulting in mechanical brittleness and an increased susceptibility to cracking. Conversely, gold dissolution involves the melting away of gold into solder or metal matrices, potentially altering the electrical and mechanical properties of the joint. Understanding the mechanisms and effects of both processes is essential for engineers seeking to enhance the durability and functionality of electronic devices in demanding environments.
There are advantages and disadvantages to gold finishes on electronic components. Gold doesn’t tarnish, provides a highly solderable surface, boasts a long shelf life, and resists oxidation. However, as illustrated in Figure 1, gold is porous and can dissolve in eutectic tin-lead solder, leading to embrittlement and weakened solder joints.
Gold embrittlement poses a considerable reliability challenge in electronic assemblies. The risk of embrittlement depends on several factors, including the amount of gold that leaches from plated surfaces, the volume of the resulting solder joint, and whether the solder comes from an unlimited source, such as wave or selective soldering processes, or a limited source, such as solder paste. For surface mount technology (SMT) components, the small volume of solder paste applied to the pads can increase the concentration of gold in the molten solder. This heightened concentration raises the likelihood of gold dendrites forming within the solder joint, which can act as catalysts for crack propagation.
Gold has a relatively low melting point and dissolves quickly during the soldering process. When excessive gold dissolution occurs during the solder alloy’s liquidus phase, it can change the composition and mechanical properties of the resulting solder joint, leading to further gold embrittlement when combined with other metals during solder joint formation. Typically, this stems from gold-plated component leads, not from contributions from PCB finishes, such as Electroless Nickel Immersion Gold (ENIG) or Electroless Nickel Electroless Palladium Immersion Gold (ENEPIG). These board finishes, averaging around 0.10 µm, are typically too thin to contribute significantly to gold embrittlement, as the threshold associated with potential issues is 0.25 µm.
Manual soldering of SMT or through-hole solder joints, with their limited solder, results in a gold-rich environment, making them more prone to crack propagation. Using gold-finished components exacerbates this issue, causing embrittlement and voids in solder joints, thereby weakening the mechanical bond strength in PCB assemblies. Under certain conditions, gold-plated components can fail because of excessive remnant gold.
Embrittlement in tin-lead (SnPb) solder joints is a known failure mechanism caused by excess gold. Meanwhile, lead-free solder alloys, such as SAC305, offer improved mechanical properties when combined with gold, mainly because of their higher tin content. However, SAC305 solder joints are not immune to degradation from increased gold levels. Studies show a lack of defined acceptable gold thresholds in SAC305 solder joints, suggesting gold removal is the best practice.
The 2014 release of Revision F of IPC-J-STD-001 addressed persistent gold embrittlement issues faced by end users, particularly due to insufficient turbulence during the wave soldering process in plated through-holes. IPC-J-STD-001 Rev F marked a significant shift in the Class 2 electronics manufacturing sector by making it mandatory to remove gold for many electronic components in Class 2 printed circuit board (PCB) assemblies.
The IPC defines criteria with specific classifications: "N" indicates no requirement, "A" denotes acceptable, "P" signifies a process indicator, and "D" denotes a defect. For example, an "A1P2D3" classification means acceptable for Class 1, a process indicator for Class 2, and a defect for Class 3.
Before Revision F, the “N1P2D3” classification applied to the gold removal requirement. This meant no requirement for Class 1, a process indicator for Class 2, and a defect for Class 3. With Rev F, the requirements were altered to "N1D2D3," indicating no requirement for Class 1 and defects for both Class 2 and Class 3. This change necessitated gold removal for all high-reliability applications, affecting a broad spectrum of the electronics manufacturing industry.
Under the current J-STD-001 Rev J requirements, gold must be removed from at least 95% of soldered surfaces on through-hole component leads with a thickness of 2.54 µm (100 micro-inches), all hand-soldered through-hole leads regardless of thickness, all soldered surfaces of surface mount components, and solder terminals plated with 2.54 µm(100 microinches) gold thickness, along with all solder cup terminals regardless of thickness.
IPC-J-STD-001 Rev J specifies that a double tinning process or dynamic solder wave may be employed for gold removal before soldering components onto an assembly. It also emphasizes that gold embrittlement in solder connections can occur regardless of gold thickness, especially when the solder volume is low or the dwell time during the soldering process is insufficient for the gold to dissolve throughout the solder joint. For through-hole components, as illustrated in Figure 2, it is essential to remove the gold plating from their surfaces before soldering them into a PCB to prevent gold embrittlement and maintain the integrity of the solder interconnection.
Improper removal of gold from component leads and terminations before PCB assembly can cause solder cracks and field failures. Therefore, the recommendation is to remove the gold to ensure that the solder establishes an electromechanical and metallurgical bond with the base metal beneath the gold—typically nickel or copper.
The ideal method for removing gold plating from surface mount and through-hole components is a robotic hot solder dip process. This re-tinning operation should be performed using a lead tinning machine that incorporates controlled flux application, convection preheating, dual dynamic solder pots with a built-in dross skimmer, nitrogen inerting, and defined process controls. This approach is preferable to manually dipping components into a static solder pot, as it helps reduce solder contamination, minimize non-wetting issues, and enhance solderability.
Re-tinned pins processed via robotic hot solder dipping typically exhibit a smooth, gold-free finish, as shown in Figure 3. This finish indicates a fully controlled lead-tinning process, free from impurities, excessive dross, or flux residues, with optimized parameters for immersion dwell time and extraction speed.
When evaluating a gold removal or tinning process, consider the type of solder pots being used. Dynamic solder pots are superior to static pots because they can circulate molten solder, resulting in minimal dross accumulation. Additionally, the number of solder pots matters; using two pots is typically recommended over one. The dynamic action in the first pot effectively removes gold plating, oxidation, and other residues, while the second pot is used to apply the new finish to the leads. There is usually a nitrogen shroud surrounding the solder pot, which minimizes icicles and dross buildup, resulting in a smooth finish.
Consistent results with the re-tinning process rely heavily on precise control of speed, time, depth, and temperature. Without control of these factors, issues with contamination, termination coverage, inconsistent solder thickness, and component damage become more prevalent. GEIA-STD-0006— Requirements for Using Solder Dip to Replace the Finish on Electronic Piece Parts— states that a robotic hot solder dip apparatus shall have:
- Dynamic solder waves or other method, which removes dross before solder dipping
- Controlled dwell time in preheat and solder pot within ±0.1 sec
- Controlled depth of immersion to within ±0.1 mm
- Controlled exit speed out of solder pot to within ±0.3 cm/sec
- Piece parts shall be preheated to less than 71⁰C prior to solder dipping
- Total immersion time shall be less than 5 seconds per component side
Solder pot contamination can occur easily, especially if using a single solder pot system. Tinning component leads with contaminated solder can result in issues other than gold embrittlement such as poor solderability and reduced electrical performance. Reduce the chances of these issues by testing solder pots regularly via X-ray fluorescence (XRF) to ensure the solder purity stays within acceptable ranges.
In conclusion, mitigating excessive gold plating is crucial for enhancing the reliability of Class 2 electronic assemblies. While traditional manual methods using a single static solder pot may appear cost-effective, they present challenges that can negatively impact the transfer of gold and other contaminants, leading to gold-rich and de-wetted solder joints. For optimal results, use advanced techniques, such as the robotic hot solder dip process. This method improves control over the gold mitigation process, safeguards against contamination, and ensures a consistent, high-quality intermetallic bond. By adhering to industry standards and using the right equipment, manufacturers can enhance solderability and reliability, ultimately producing more dependable electronic components and assemblies.
Future columns will explore various aspects of the robotic hot solder dip process, with further insights and best practices to improve quality and performance in electronic device assembly.
This column originally appeared in the May 2025 issue of SMT007 Magazine.
More Columns from Knocking Down the Bone Pile
Knocking Down the Bone Pile: Addressing End-of-life Component Solderability Issues, Part 4Knocking Down the Bone Pile: Tin Whisker Mitigation in Aerospace Applications, Part 3
Knocking Down the Bone Pile: Basics of Component Lead Tinning
Knocking Down the Bone Pile: Package on Package Rework—Skill Required
Knocking Down the Bone Pile: 2023’s Top Challenges in BGA Rework
Knocking Down the Bone Pile: Eliminating Solder Balls in Hand Soldering
Knocking Down the Bone Pile: Opening a Trace on the Surface of a PCB
Knocking Down the Bone Pile: Soldering for QFPs and Other Gull Wing Leaded Parts