-
- News
- Books
Featured Books
- pcb007 Magazine
Latest Issues
Current IssueSales: From Pitch to PO
From the first cold call to finally receiving that first purchase order, the July PCB007 Magazine breaks down some critical parts of the sales stack. To up your sales game, read on!
The Hole Truth: Via Integrity in an HDI World
From the drilled hole to registration across multiple sequential lamination cycles, to the quality of your copper plating, via reliability in an HDI world is becoming an ever-greater challenge. This month we look at “The Hole Truth,” from creating the “perfect” via to how you can assure via quality and reliability, the first time, every time.
In Pursuit of Perfection: Defect Reduction
For bare PCB board fabrication, defect reduction is a critical aspect of a company's bottom line profitability. In this issue, we examine how imaging, etching, and plating processes can provide information and insight into reducing defects and increasing yields.
- Articles
- Columns
- Links
- Media kit
||| MENU - pcb007 Magazine
Estimated reading time: 1 minute
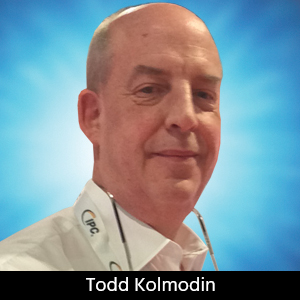
Testing Todd: Plating and Surface Finish—The Challenges to Electrical Test
Plating
Plating and surface finish applications are not without their own set of challenges but these manufacturing processes also effect the electrical test theatre. Microvias, high-aspect ratio plate quality, and surface finish all have their own challenges in ET.
Let’s face it, the largest challenges regarding plating involve the detection of voids. Whatever type they may be is insignificant in ET as the detection is foremost the main focus. Unfortunately, with standard ET detection processes many partial voids go undetected. This also can be said for a barrel that is voided outside of the electrical test signature.
The undetected partial void is usually the “taper plate” or “narrowing” void. These defects usually have adequate plating near the annular rings towards the outer layers but then narrow as they reach the center of the barrel. Figure 1 shows a typical taper plate defect.
This type of defect usually will not fail the standard ET continuity test. There is sufficient plating in the barrel to pass the electrical signal within the continuity threshold (usually 10–20 ohms depending on performance class). For the capture of anomalies such as this it is recommended that a 4-wire Kelvin sampling test be performed. This type of continuity test is designed to capture minute fluctuations in barrel resistivity. These measurements are in the milliohm (mO) range.
To read the full version of this article which appeared in the Jannuary 2017 issue of The PCB Magazine, click here.
More Columns from Testing Todd
Testing Todd: Why 4-wire Kelvin?Testing Todd: Why TDR?
Testing Todd: Positivity Boosts Employee Morale
Testing Todd: Preparing Employees for the Long Haul
Testing Todd: Where Can We Improve?
Testing Todd: Turning Into the Wind
Testing Todd: Coming Back to Life—Design Recovery
Testing Todd: Decision Time—Invest or Delegate?