-
- News
- Books
Featured Books
- pcb007 Magazine
Latest Issues
Current IssueSales: From Pitch to PO
From the first cold call to finally receiving that first purchase order, the July PCB007 Magazine breaks down some critical parts of the sales stack. To up your sales game, read on!
The Hole Truth: Via Integrity in an HDI World
From the drilled hole to registration across multiple sequential lamination cycles, to the quality of your copper plating, via reliability in an HDI world is becoming an ever-greater challenge. This month we look at “The Hole Truth,” from creating the “perfect” via to how you can assure via quality and reliability, the first time, every time.
In Pursuit of Perfection: Defect Reduction
For bare PCB board fabrication, defect reduction is a critical aspect of a company's bottom line profitability. In this issue, we examine how imaging, etching, and plating processes can provide information and insight into reducing defects and increasing yields.
- Articles
- Columns
- Links
- Media kit
||| MENU - pcb007 Magazine
Estimated reading time: 3 minutes
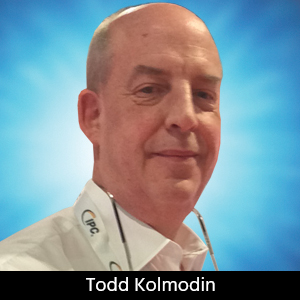
Testing Todd: Coming Back to Life—Design Recovery
Although iconic, when I say “coming back to life,” I’m not talking about a Pink Floyd song, but rather about printed circuits. Bare boards have been in production for decades—from single- and double-sided breadboards to the impressive multilayer designs of today—and we all agree that the PCB is here to stay.
With today’s technology, designs are archived and realistically available forever. However, much of the legacy product of decades past is long forgotten. These rugged PCBs have been in service for years; their spare parts are full of dust on a forgotten shelf, ultimately obsoleted and scrapped.
In consumer electronics, this is less of an issue because technology is advancing almost daily and new designs and enhancements are continuously evolving. But what about those rugged, hidden, non-consumer products that are keeping important infrastructure plugging along? Some of these high-reliability products are not thought about—until they fail. Then frantic calls for a replacement lead someone to discover that the dusty part on that long-forgotten shelf was obsoleted last Friday and is sunbathing in the landfill now. Farfetched? Unfortunately, truer than you think.
Now, as for what to do in such a situation: If you’re lucky, the PCB manufacturer may have a bare PCB in archive with an intact service agreement for long-term support. Or, they may have the phototools archived and can readily reproduce the PCB. But more likely, you’ll find yourself answering “no” when checking whether you have these options available to you—and then you’re stuck. You’re forced to look for an updated model or part for your historic equipment that likely doesn’t exist or does not have the necessary certification for the duty it must perform. However, all is not lost.
The design can be recovered. Currently, there are two main options available to reverse engineer or recover the PCB: netlist extraction and destructive scanning. Both options provide solutions to recovering the PCB.
- Netlist extraction: If all phototools and design data are lost but a bare PCB remains, this is a lower-cost recovery option. A “golden” PCB is preferred but not necessary. If the bare PCB has a known fault, it can be dealt with post-process. In this process, the bare PCB is scanned utilizing a high-resolution flatbed scanner. This provides the “footprint” of the PCB. The two sides are then combined using CAM software and a “dumb” netlist as output. This file is taken to a flying probe with self-learn capability. The bare PCB is put on the machine and the machine is instructed to learn the electrical intelligence of the PCB. When this is complete, the information is then taken back to the CAM system where an IPC netlist or neutral net can be created. This can be sent back to the customer or design bureau to recreate the phototools to remanufacture the PCB.
- Destructive scanning. Here we are using the principles of the first option to create the phototools for the customer. Just as in the first example, we are scanning the outer surfaces of the PCB; once the outer layers are completed, we will use precision sanding and/or milling equipment to either mill or sand the PCB to expose the next layer. This layer will then be scanned. The process will continue until all layers have been captured. Each layer is scrutinized and carefully re-created electronically. Edits may include increasing trace widths to industry/customer requirements, fixing angles and terminations, or guaranteeing connections from the scanned images. Comparing the netlist created by the self-learn to the netlist created by the destructive scanning process is an important step to remember. This can identify a discrepancy between the scanning and the raw self-learn. If there are issues, design engineering can be consulted to identify the proper signature. Once this is complete, the layers can be electronically combined, and the IPC or neutral net created. In addition, the phototools, drill file(s), and other manufacturing-related files are created. This final package can then be sent back to the manufacturer/customer for remanufacturing.
All is not lost just because a manufacturer has obsoleted a legacy design. With some time, patience, and the right partner, the design can be recovered and that forgotten (but reliable) infrastructure can continue plugging along. No design is lost forever.
Happy holidays to all of you and your families.
This column originally appeared in the December 2022 issue of PCB007 Magazine.
More Columns from Testing Todd
Testing Todd: Why 4-wire Kelvin?Testing Todd: Why TDR?
Testing Todd: Positivity Boosts Employee Morale
Testing Todd: Preparing Employees for the Long Haul
Testing Todd: Where Can We Improve?
Testing Todd: Turning Into the Wind
Testing Todd: Decision Time—Invest or Delegate?
Testing Todd: Induction Junction, What’s Your Function?