-
- News
- Books
Featured Books
- pcb007 Magazine
Latest Issues
Current IssueSales: From Pitch to PO
From the first cold call to finally receiving that first purchase order, the July PCB007 Magazine breaks down some critical parts of the sales stack. To up your sales game, read on!
The Hole Truth: Via Integrity in an HDI World
From the drilled hole to registration across multiple sequential lamination cycles, to the quality of your copper plating, via reliability in an HDI world is becoming an ever-greater challenge. This month we look at “The Hole Truth,” from creating the “perfect” via to how you can assure via quality and reliability, the first time, every time.
In Pursuit of Perfection: Defect Reduction
For bare PCB board fabrication, defect reduction is a critical aspect of a company's bottom line profitability. In this issue, we examine how imaging, etching, and plating processes can provide information and insight into reducing defects and increasing yields.
- Articles
- Columns
- Links
- Media kit
||| MENU - pcb007 Magazine
Estimated reading time: 3 minutes
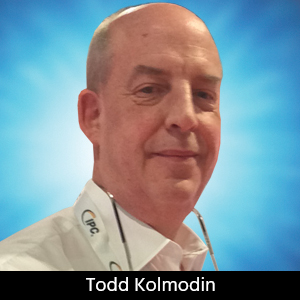
Testing Todd: Preparing Employees for the Long Haul
Rebuilding our workforce after the COVID-19 pandemic has been a challenge. Nationwide, we downsized to combat market conditions and ultimately lost good employees due to either the virus or them finding new work elsewhere. That has left some rather large gaps in our manufacturing workforce. Human resource departments are scrambling to find new employees, while the manufacturing base struggles to educate and bring new employees up to speed. If not handled correctly, this scenario could create even greater problems for manufacturers.
While automating menial or repetitive tasks is one way to quickly fill the gaps at low- or entry-level positions in the workforce, filling more complex roles can be more challenging, and is where many companies fall short.
Companies find new candidates, send them into the workplace jungle, and assign them a supervisor who instructs them on their tasks or duties. Realistically, new employees are often overwhelmed and may struggle to master the assigned tasks. In many cases, the supervisor is also over-tasked with other duties and responsibilities and cannot provide the over-the-shoulder experience that is required for good oversight.
Employees learn in different ways. Some of them are visual learners, grasping new tasks and instructions on the fly, while others need to read instructions and commit them to memory. This is why long-term success for employees relies on a robust training system that connects to different types of learners.
Those involved in quality management systems will see that this is nothing new. They know that having a truly functional training system is essential to guaranteeing the long-term success of employees. An effective training system must do more than just satisfy a requirement.
Developing strong, documented processes is a must. They must be “ready for pickup” by new employees so that they can learn and understand the process in which they will be involved. Furthermore, the work instructions associated with the tasks must be mature and bulletproof.
The overall training process can break down when a supervisor, who may not be well versed in the process, assigns another employee the task of showing the ropes to new hires. In my experience, this is not a good practice. This is when missed steps or manufacturing-floor “voodoo” may come into play, setting up the new employee to fail or become the fall guy.
Here are some tips that can help you achieve long-term success in filling either vacant or new positions as workforce conditions improve.
- Document your processes and, at a minimum, review them annually.
- Designate trainers for each department and, if necessary, for each task level.
- Train the trainers. Make sure they know the process inside out. Be sure to document employees’ knowledge.
- Train new employees; don’t just show them the ropes. As I mentioned, effective training that utilizes different ways of learning will ensure long-term success of new employees. Document their knowledge level and then review (and document) it again 60 to 90 days after hiring as a way to validate their progress. Finally, discuss with them any concerns you may have.
- Review an employee’s knowledge retention at least annually. This ensures that no irregular habits have been introduced into the process and that employees are progressing well. Perhaps they have mastered the tasks and are ready for a new challenge. You can backfill their current position and move them into a more challenging role in the company.
Summary
The post-pandemic years have been challenging. Effectively rebuilding the workforce for the long haul requires some fundamental steps, such as training new employees and reviewing their knowledge over time. Whether this is new to you or just a review of standard practice, I hope you now have some tools to help your organization grow effectively as you face challenges ahead.
This column originally appeared in the April 2023 issue of PCB007 Magazine.
More Columns from Testing Todd
Testing Todd: Why 4-wire Kelvin?Testing Todd: Why TDR?
Testing Todd: Positivity Boosts Employee Morale
Testing Todd: Where Can We Improve?
Testing Todd: Turning Into the Wind
Testing Todd: Coming Back to Life—Design Recovery
Testing Todd: Decision Time—Invest or Delegate?
Testing Todd: Induction Junction, What’s Your Function?