-
- News
- Books
Featured Books
- pcb007 Magazine
Latest Issues
Current IssueInventing the Future with SEL
Two years after launching its state-of-the-art PCB facility, SEL shares lessons in vision, execution, and innovation, plus insights from industry icons and technology leaders shaping the future of PCB fabrication.
Sales: From Pitch to PO
From the first cold call to finally receiving that first purchase order, the July PCB007 Magazine breaks down some critical parts of the sales stack. To up your sales game, read on!
The Hole Truth: Via Integrity in an HDI World
From the drilled hole to registration across multiple sequential lamination cycles, to the quality of your copper plating, via reliability in an HDI world is becoming an ever-greater challenge. This month we look at “The Hole Truth,” from creating the “perfect” via to how you can assure via quality and reliability, the first time, every time.
- Articles
- Columns
- Links
- Media kit
||| MENU - pcb007 Magazine
Estimated reading time: 4 minutes
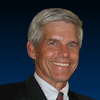
All About Flex: Creating a Flexible Circuit Cutline
The perimeter dimensions of a flexible circuit are often referred to as the cutline. While rigid printed circuits are often rectangular and generally a less complex outline, the requirement for a flexible circuit to be an integrated part of the product packaging often involves unusual sizes, shapes and features in the circuit perimeter. The cutline can be created with several processing techniques and tooling options. The following are considerations in determining techniques for creating a flexible circuit cutline:
- Size and shape: Some parts could be less than an inch in length while having a complex shape. Other parts could be narrow strips that are 10 feet long. Techniques that would work well for the former, would not work for the latter.
- Material stack-up: A single-sided 1-mil polyimide flexible circuit will handle and cut differently than a 6-layer circuit with FR-4 stiffeners laminated to the back side. Cutting very thin flimsy material will involve different tools and processes vs. a thicker circuit.
- Tolerances: Dimensional changes in the panel are considerations when determining process steps and tooling needed to meet feature requirements. Tolerances between cutline features or from cutline to internal features vary with material constructions and thicknesses. Tight tolerances between and within features may be possible but can involve added tooling and processes resulting in higher cost fabrication costs.
- Volume and budget: Investments in tooling to improve productivity are often justified for high volume programs. Hard tools may be an option for serial production volume while numerically defined and controlled tooling is more appropriate for lower volume.
- Component assembly: Component assembly is often more efficient if done while parts remain multiple-up and in panel form. Special tooling and techniques are often required to create the cutline on assembled panels.
The following are common techniques for defining a flexible circuit cutline:
- Routing: The outline is routed using an NC drill with special routing bits.
- Advantages: No special tooling is needed as the perimeter is defined by a CAM file. Routing is flexible in terms of shapes, sizes and even material stack up. The cutline pattern on the panel can be scaled to accommodate dimensional changes during processing.
- Disadvantage: Routing bits create a cutline that may be a little ragged, especially for thin materials. In many applications, this is mostly a cosmetic issue.
- The circuitry is often mechanically aligned to the drill while the internal features are created. Registration tolerances may be an issue.
- Laser Ablation: An NC-controlled, high intensity laser beam will create the cutline. The beam is XY controlled with optical alignment based on panel fiducials.
- Advantages: No special tooling is needed, as the perimeter is defined by CAM files. The edge definition is precisely defined and smooth. Optical alignment, combined with scaling for panel dimension changes, provides very accurate cutline to feature tolerances. Lasers can also define extremely precise and unusual features that may not be possible with other tooling methods.
- Disadvantages: While this technique will work well with most materials, laser ablation may not be ideal for thick materials or flexible circuits with multiple layers or pressure sensitive adhesives. More energy is required as parts become thicker. Costs are higher as expensive capital equipment time is consumed. This method may require circuit cleaning post processing as carbon char residue can remain on the cutline.
- Steel Rule Die: Steel rule die cutting has been compared to cookie dough cutting. Sharpened blades are accurately held in position with a high-density wood or aluminum base plate. The die blades are “pushed” against the material until it is cut. Special backer materials are used to enhance the cut and lengthen the die life.
- Advantages: A rule die is normally low cost and has good die life. Manufacturers will build the die to +/- .005” tolerances, but resulting cutline dimensions require slightly larger tolerances. This is a fairly efficient process as several circuit parts can be punched in a few seconds.
- Disadvantages: The quality of cut and rule die life are highly dependent on type of press, technique and materials to be cut. Once a die is fabricated, it cannot be adjusted to accommodate dimensional changes in the panel. If cutline tolerances need to be less than +/- .005”, hard tooling or laser profiling should be considered instead of a rule die.
- Hard Tool Die: A typical hard tool die has “male” and “female” plates that mesh together to punch the material. These are sometimes called “zero clearance” dies since the male punch is built slightly oversized and from a harder metal. The initial punch cycle shears the tool to create a clearance free punch receptacle.
- Advantages: Cutline to cutline dimensions can be very accurate and the cut is normally very smooth. A well-designed tool in a good press can last thousands of impressions with very little maintenance.
- Disadvantage: Hard tools can be heavy and bulky and take up more storage space than a rule die. Once a die is fabricated, it cannot be adjusted to accommodate dimensional changes in the panel. The cost for a hard tool can be significant depending on configuration and size. Hard tools are generally the most expensive tooling options.
- Combination Methods: Sometimes a cutline can be defined by 2−3 process steps instead of one tool. For example, critical areas such as a ZIF connector end can be defined with a highly accurate optically controlled punch while the rest of the cutline might be created with a less accurate method.
There are multiple options and considerations when determining the method and tooling for creating the cutline. Each option can have an impact on cost and yields. Early consultation with a flex circuit applications engineer is a good vetting practice to properly balance requirements for performance and cost.
Dave Becker is vice president of sales and marketing at All Flex Flexible Circuits LLC.
More Columns from All About Flex
All About Flex: Terms and ConditionsAll About Flex: ISO 9001 Basics
All About Flex: FAQs on UL Listings for Flexible Circuits
All About Flex: Avoiding Trace Fracturing in a Flexible Circuit
Polyimide vs. Silicone for Flexible Heaters
All About Flex: Copper Thickness Requirements for Flex Circuits
All About Flex: Copper Grain Direction
All About Flex: Options for Purchasing Flexible Heaters