-
- News
- Books
Featured Books
- pcb007 Magazine
Latest Issues
Current IssueInventing the Future with SEL
Two years after launching its state-of-the-art PCB facility, SEL shares lessons in vision, execution, and innovation, plus insights from industry icons and technology leaders shaping the future of PCB fabrication.
Sales: From Pitch to PO
From the first cold call to finally receiving that first purchase order, the July PCB007 Magazine breaks down some critical parts of the sales stack. To up your sales game, read on!
The Hole Truth: Via Integrity in an HDI World
From the drilled hole to registration across multiple sequential lamination cycles, to the quality of your copper plating, via reliability in an HDI world is becoming an ever-greater challenge. This month we look at “The Hole Truth,” from creating the “perfect” via to how you can assure via quality and reliability, the first time, every time.
- Articles
- Columns
- Links
- Media kit
||| MENU - pcb007 Magazine
Estimated reading time: 3 minutes
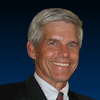
All About Flex: Volume Considerations
With any new electronic interconnection project, one immediate question the supplier will inquire about is program volume expectations. Customers often ask “What is your capacity?” with low-, medium- and high-volume having different meanings to different people. In the world of flexible circuit processing, this numerical question is complicated by the panel process manufacturing methods used to produce printed circuits. In reality, the volume capability of a PCB shop is probably best defined by panel capacity (continuous reel manufacturing of extremely high-volume flex circuitry is an immediate exception). The physical size of a large circuit may mean “high” volume is 500 parts/month, while manufacturing capacity to produce a small circuit could comfortably exceed 20,000 within the same factory footprint.
Flexible circuit construction types also significantly affect capacity and volume. Continuous or “dynamic” flexing applications often require multiple imaging processes to selectively electrodeposit copper to plated through-hole regions. This preserves bending regions with rolled annealed copper (by selectively avoiding additional electroplated copper). Producing flexible circuits with this process sequencing is known in the industry as “pads only plating” or “button plating.” Another significant factor in capacity consumption results from fabrication of multilayer circuits, produced from multiple panels subsequently laminated together to make the final product.
“Common” panel sizes in the U.S. are generally defined in inches (12” x 24” and 18” x 24” are most frequent) while Asia and Europe often define panels with metric dimensions. Widths of 250 mm and 300 mm are those I have seen most frequently. Oversized flex circuits (generally >22”) can be produced with specialized equipment, handling, and processes on non-standard panels. Lengths exceeding several feet are possible but construction lay-up options can limit producibility for a given part number.
Flexible circuits are produced in a myriad of constructions and sizes and in low- and high-volume quantities. Volume visibility is a key consideration during part number set-up. Options that may be cost effective at low quantities might not make sense for higher volume, and vice versa. The following are a few examples of volume considerations:
Panelization
Efficient material utilization through nesting parts on a panel can have a dramatic material cost influence. Reverse nesting and interlocking of circuits may add a significant quantity of parts to a panel. For high-volume applications, the number of circuits on a panel is a key cost driver, but the impact on component assembly, stiffener attachment, and required tolerances are also factors. Efficient material utilization should be a key consideration during design as folds in flexible materials add a degree of freedom when defining shapes…and this freedom can allow better material usage.
Tooling
Low-volume circuits will infrequently use physical tools such as dies, test fixtures and assembly fixtures. Instead optically aligned and numerically controlled (NC) processing equipment such as laser cutting, laser imaging, NC routing, flying probe testers, and NC dispensers. This “tool-less” manufacturing capability enables fast turn, inexpensive modification, and minimal set-up time.
For high-volume applications, special tooling can greatly improve the process through-put and attain a satisfactory return on the investment. Specifically, some of the investments could include:
Die Cutting
Cutline and internal features can be easily created using the automated NC controlled routing, drilling and punching equipment. These are more than adequate for lower to medium volume circuits, but as volumes increase, it may make sense to invest in soft or hard tooled dies.
Electrical Test
The flying probe tester consists of sets of probes that individually test each circuit net. The newer generation of flying probe equipment provides fast testing, requires no special tooling, and can be set up rapidly. A custom built “bed of nails” test fixture will probe all test points simultaneously and can test the entire part, or multiple parts, in seconds. As build volume increases, the economics often favor the bed of nails tester.
Assembly
The speed and accuracy of today’s pick and place equipment is fascinating. An investment return on this highly automated and capital intensive equipment is usually not justified at lower volumes. Less automated methods to assemble, including hand assembly, are preferred. Operators using magnification and hand soldering 0201 components is almost as fascinating as watching a high speed SMT line! These less automated methods can be accurate and reliable, and require less engineering set-up and programming.
The most cost effective way to set up a part number will be different depending on quantities. Investing in expensive tooling or using highly automated equipment normally requires adequate volume to justify the added expense or longer set up time. These considerations and many other cost tradeoffs are considerations when determining an optimal process and material construction for an individual circuit part number.
Dave Becker is vice president of sales and marketing at All Flex Flexible Circuits LLC.
More Columns from All About Flex
All About Flex: Terms and ConditionsAll About Flex: ISO 9001 Basics
All About Flex: FAQs on UL Listings for Flexible Circuits
All About Flex: Avoiding Trace Fracturing in a Flexible Circuit
Polyimide vs. Silicone for Flexible Heaters
All About Flex: Copper Thickness Requirements for Flex Circuits
All About Flex: Copper Grain Direction
All About Flex: Options for Purchasing Flexible Heaters