-
- News
- Books
Featured Books
- pcb007 Magazine
Latest Issues
Current IssueIn Pursuit of Perfection: Defect Reduction
For bare PCB board fabrication, defect reduction is a critical aspect of a company's bottom line profitability. In this issue, we examine how imaging, etching, and plating processes can provide information and insight into reducing defects and increasing yields.
Voices of the Industry
We take the pulse of the PCB industry by sharing insights from leading fabricators and suppliers in this month's issue. We've gathered their thoughts on the new U.S. administration, spending, the war in Ukraine, and their most pressing needs. It’s an eye-opening and enlightening look behind the curtain.
The Essential Guide to Surface Finishes
We go back to basics this month with a recount of a little history, and look forward to addressing the many challenges that high density, high frequency, adhesion, SI, and corrosion concerns for harsh environments bring to the fore. We compare and contrast surface finishes by type and application, take a hard look at the many iterations of gold plating, and address palladium as a surface finish.
- Articles
- Columns
Search Console
- Links
- Media kit
||| MENU - pcb007 Magazine
Estimated reading time: 4 minutes
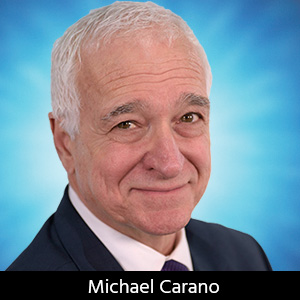
Contact Columnist Form
Trouble in Your Tank: Metalizing Difficult-to-Plate Substrates
Introduction
Metalizing materials such as polyimide used for flexible circuitry provides a significant challenge for process engineers. Conventional electroless copper systems often required pre-treatments with hazardous chemicals or have a small process window to achieve a uniform coverage without blistering. It all boils down to enhancing the adhesion of the thin film of electroless copper to these smooth surfaces. In addition, internal stress in the copper deposit is a significant factor with respect to adhesion of the plated metal to the substrate. This process of plating on polyimide flexible materials is very much POP (plating on plastics). Electroless copper has been adapted for metalization of difficult to plate substrates and materials such as polyimide, POP and molded interconnect devices (MID). The author will present MID in a future column.
The Challenge of Metalizing Smooth Surfaces
One significant concern with metaliizing thin films over substrates is the concept of deposit stress. Hydrogen gas is a by-product of the electroless copper deposition process. Consequently, hydrogen may be incorporated into the thin deposit with a negative influence on internal stress. The hydrogen gas issue has been attributed to blister formation in the copper deposit. In addition, a challenge typically encountered on smooth surfaces such as polyimide-based flexible circuit materials is ensuring good adhesion of the electroless copper to the substrate. Adhesion of a thin film deposit to a substrate that lacks sufficient microroughness is compromised. To mitigate this issue, one solution is to reduce the internal stress of the copper deposit as much as possible.
Now, one remedy to minimize hydrogen gas effects on the deposit is to lower the surface tension of the electroless copper electrolyte. By lowering surface tension using specific wetting agents, the hydrogen gas bubbles are less likely to remain on the plated surface. The hydrogen gas issue not withstanding, one must also be concerned with electroless copper deposit stress. Excessive deposit stress will cause the copper plated deposit to blister or pull away from the substrate. Essentially this is a stress relief phenomenon.
Figure 1: Hole wall after desmear with alkaline permanganate (rigid circuit board with epoxy resin-high Tg 170°C material). Source: RBP Chemical Technology
It is well known that polyimide materials for flexible circuit fabrication have a rather smooth texture even after plasma desmear. Unlike most of the epoxy-based resin systems, polyimide for flex remains void of the micro-roughened surface texture generally experienced with alkaline permanganate chemical desmear. With these “anchoring” sites (Figure 1), one can see that there is ample surface area for which the thin film of electroless copper can adhere to epoxybased resin systems.
Another limiting factor with respect to adhesion of copper to flexible polyimide is the low surface energy of polyimide films. Surfaces with low surface energy tend to repel chemical interactions, making it more difficult for process chemistry to effect good adhesion properties. In addition, flexible circuits are by design flexed and bent during their useful service life. Therefore, creating excellent adhesion of the plated copper to the substrate is critical to the functioning of the circuit. Certainly, plasma treatment of the polyimide material provides an improvement to the low surface energy of polyimide. However, such treatments often do not go far enough to insure long-term adhesion by relieving internal stress.
Figure 2: Polyimide flexible circuit after plasma desmear—note the smooth topography. (Source IPC 9121 Process Effects Handbook)
The Influence of Stress
Stress in the electroless copper deposit can be either compressive or tensile. The copper deposit can be thought of as a spring that is either under tension (stretched), which is tensile stress, or compressed, which is compressive stress. Compressively stressed copper deposits lift or blister off smooth surfaces that lack anchoring sites such as adhesive-less polyimide flexible materials.
The spiral contractometer as shown in Figure 3 utilizes a strip of metal wound into a coil or helix. The unit is attached to the plating cell and the metal is then deposited on one side of the coil only. Depending on the type and extent of the internal stress, the coil will either expand or contract. If the deposit is compressively stressed, the coil will tighten. If the stress is tensile, the coil will expand. The contractometer is equipped with a gauge to measure quantitatively whether the stress is compressive or tensile.
Figure 3: Spiral contractometer for measuring internal stress in the plated deposit.
So it is somewhat obvious that excellent plating adhesion to the substrate is necessary for a circuit that will experience potentially many flexures over the course of its life. In addition, low to no stress in the copper deposit is preferred. It is important to keep in mind that adhesion of a thin film to a substrate is a complex mechanism. Internal deposit stress is just one factor. Additional factors affecting adhesion are:
- Ionic bonding between two surfaces
- Adsorption: adhesion is based on interatomic and intermolecular interactions such as van der Waals and perhaps Lewis Acid interactions
- Mechanical interlocking
The last bullet point depends on the contribution from a roughened surface. In the case of flexible polyimide, a roughened topography is not achievable.
With respect to flexible polyimide, optimum adhesion of the electroless copper deposit is heavily dependent on internal deposit stress and adsorption of the palladium catalyst to a plasma desmear treated surface. Please keep these factors in mind when troubleshooting an adhesion issue.
Michael Carano is VP of Technology and Business Development at RBP Chemical Technology. To read past columns or to contact Carano, click here.
Editor's Note: This article originally appeared in the February 2017 issue of The PCB Magazine,
More Columns from Trouble in Your Tank
Trouble in Your Tank: Yield Improvement and ReliabilityTrouble in Your Tank: Causes of Plating Voids, Pre-electroless Copper
Trouble in Your Tank: Organic Addition Agents in Electrolytic Copper Plating
Trouble in Your Tank: Interconnect Defect—The Three Degrees of Separation
Trouble in Your Tank: Things You Can Do for Better Wet Process Control
Trouble in Your Tank: Processes to Support IC Substrates and Advanced Packaging, Part 5
Trouble in Your Tank: Materials for PWB Fabrication—Drillability and Metallization
Trouble in Your Tank: Supporting IC Substrates and Advanced Packaging, Part 5