-
- News
- Books
Featured Books
- pcb007 Magazine
Latest Issues
Current IssueInventing the Future with SEL
Two years after launching its state-of-the-art PCB facility, SEL shares lessons in vision, execution, and innovation, plus insights from industry icons and technology leaders shaping the future of PCB fabrication.
Sales: From Pitch to PO
From the first cold call to finally receiving that first purchase order, the July PCB007 Magazine breaks down some critical parts of the sales stack. To up your sales game, read on!
The Hole Truth: Via Integrity in an HDI World
From the drilled hole to registration across multiple sequential lamination cycles, to the quality of your copper plating, via reliability in an HDI world is becoming an ever-greater challenge. This month we look at “The Hole Truth,” from creating the “perfect” via to how you can assure via quality and reliability, the first time, every time.
- Articles
- Columns
- Links
- Media kit
||| MENU - pcb007 Magazine
Estimated reading time: 3 minutes
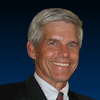
All About Flex: Considering a Flexible Heater?
Custom flexible heaters are available in an infinite variety of sizes, shapes and materials. The most common flexible materials are polyimide and silicone rubber. While silicone rubber has traditionally been thought of as the higher temperature flexible heater option, recent advances in polyimide-based materials have allowed high performance heater constructions to operate successfully at temperatures that exceed 250°C. But few customers are really interested in the temperature of the heater. They are using a heater to elevate the temperature of a “heat sink” (i.e., the device the heater is attached to). So, a discussion of engineering considerations for use of a flexible heater is often useful.
The wattage of a heater is the overall watts the heater generates based upon the input voltage and resistance of the heater (assuming sufficient amperage at that stated voltage is available from the power supply). You could have a 100-watt heater that is a 4” X 4”, or another heater delivering 100 watts but is two square feet in size. The heat (thermal output) generated by the 100 watts in the 4” X 4” example pushes heat out through 16 square inches of area. The second example spreads that same wattage over 288 square inches. So, what we really look at is watt density, or watts per area. In these two examples, each are 100-watt heaters, but the first has a watt density of 100/16 or 6.25 watts per square inch. The second example is 288/100 or 2.88 watts per square inch.
In a pure state, the first heater example will get much hotter compared to the second example, however, everything depends upon how the individual heater is used in its application. If each heater was suspended in still open air, the first will get much hotter than the second. But in an application, the first heater might realistically be mounted onto a thick aluminum plate which serves as the door of a freezer. The aluminum plate is normally cold to the touch and will “absorb” heat quickly. We could take the first ‘hotter’ heater and stick it onto the aluminum plate and the heat will be quickly extracted from the heater and into the cold plate using thermal conduction. No matter how long the heater is stuck there, the high mass door rises in temperature modestly, perhaps an increase of 10 degrees as it transitions from a cold to semi-cold state. In addition, the heater itself, even though it may get hot if it was hung in the air, no longer gets hot. It is still generating 100 watts but the heat is rapidly transferred from the heating element into the aluminum.
Another example is in an application where the starting temperature is very cold, like -50°C, and the application needs to heat it to +150°C. This would require a high watt density heater to provide that type of thermal rise. Similarly, an application may have a requirement to heat quickly then shut off. In these situations, the heater is likely to require a high wattage/thermal output. But the heater itself never gets above 150°C. In this example a heater could work well provided the heat from within the heater can be transferred before the heater itself gets too hot to maintain structural integrity.
Customers generally need three key pieces of information for each individual application: 1) how hot they want their “product,” (i.e., the eventual stabilization temperature); 2) how fast they want that heating to occur; and 3) at what temperature the device will be when it begins heating. These multi-dimensional factors can drive the heater design and material construction. Finite Element Analysis (FEA) software can be used to model an accurate estimate of thermal performance in complex scenarios. Other times, sample heaters are used with a variable power source to define watt density required through empirical testing. This information can then be used to define a custom part.
In a nutshell, specific applications drive whether an individual heater can survive or not. A very high watt density heater might be sandwiched between two cooling plates and the heater will survive just fine at a high watt density. But the same heater, if wrapped around a glass tube, might burn up because the heater is unable to handle the heat generated since the glass effectively insulates and slows thermal transfer. When considering ultra-hot heating applications (250°C+), the application may require the heater to achieve 300°C and not degrade. New materials are allowing successful designs at this elevated temperature.
Dave Becker is vice president of sales and marketing at All Flex Flexible Circuits LLC.
More Columns from All About Flex
All About Flex: Terms and ConditionsAll About Flex: ISO 9001 Basics
All About Flex: FAQs on UL Listings for Flexible Circuits
All About Flex: Avoiding Trace Fracturing in a Flexible Circuit
Polyimide vs. Silicone for Flexible Heaters
All About Flex: Copper Thickness Requirements for Flex Circuits
All About Flex: Copper Grain Direction
All About Flex: Options for Purchasing Flexible Heaters