The Wide World of Flex
March 23, 2017 | Dave Becker, All FlexEstimated reading time: 7 minutes
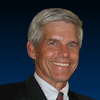
Earlier this week, I saw my name in the company newsletter announcing my 10-year anniversary with All Flex. This wouldn’t be so bad if the anniversary wasn’t preceded by almost 30 years at my previous employer, who also happened to be a manufacturer of flexible circuitry. In other words, I have become an industry “greybeard.” If I were honest with myself, I’d admit the nickname was probably appropriate several years ago, but it does allow me membership in a dwindling club who have witnessed the dramatic industry changes over the past four decades. But first, what are flex circuits?
The industry segments flexible circuits into three classes (per IPC-6013, an industry standard document).
- Class 1 circuits are used in applications with the fewest reliability requirements and minimum inspection. In reality, almost no one calls out inspection at Class 1.
- Class 2 circuits have moderate inspection, testing, and performance requirements and are typically found in consumer applications such as cellphones or cameras.
- Class 3 circuits are found in the highest-reliability applications, require the highest inspection and test standards, and are often specified by in military and crucial medical electronics.
Flexible circuits are also categorized in IPC-6013 by “Types.” There are five Types defined but only four (Type 1, 2, 3 and 4) are common. Although the insulating material and copper trace access also defines the circuit type, in general, Type 1 flex circuits are defined as those with a single conductive layer. These are known as single-sided circuits. Type 2 flex circuitry has two conductive layers and are referred to as double-sided circuits. These parts have plated through-holes connecting copper layers. Type 3 circuits are multilayers and have 3+ conductive layers with plated through-holes. Type 4 are rigid-flex, a combination of rigid and flexible circuit boards characterized by plated interconnect holes through both flex and rigid materials. Frequently confused with rigid-flex are flexible circuits with selective rigid stiffeners. These are more appropriately termed “rigidized flex” and might be any of the first three circuit types.
In one sense the flexible circuit industry has remained amazingly stable. Things I learned on my first day at work are still relevant. Polyimide remains the workhorse dielectric film; imaging is done by exposing a pattern on a photosensitive film; copper is subtractively removed from a patterned substrate; and crylic adhesive is commonly used to laminate polyimide coverlay as an insulation. But there have also been some rather dramatic changes...
So Big!
Flexible circuitry was launched in the United States as a commercial product about 50 (!) years ago. Minnesota remains a focal point for the technology, along with New England and California. The Minnesota nexus occurred as G.T. Schjeldal (the entrepreneur who founded Sheldahl Inc.) built equipment to handle thin flexible films in continuous reels. Automated equipment could cut and heat-seal polyester and was used to fabricate plastic bags. This technology foundation evolved and was adopted to produce electrical laminates. Value was then added through roll-to-roll electroplating, imaging, and etching continuous reels as part of the process of fabricating printed circuits. It was a very high-volume process targeting the automotive and communications markets. This technical heritage expanded regionally as engineers spawned new, related businesses.
In this time frame, the 1980s, the flexible circuit market size was estimated at less than $200 million as Asia had yet to emerge as an industrial player (that seems like a long time ago). Today the North American flex circuit market is estimated at about $350 million but is dwarfed by manufacturers in Japan, Korea, China and Taiwan. Worldwide market size estimates vary considerably and are complicated since few customers buy a simple “flex circuit.” Added value is a common offering as circuits are frequently sold with components as an interconnect solution. A worldwide market size of $7−11 billion seems to be a common range. Almost any electronic application is a candidate for a flex circuit with cellphones, cameras, displays, and consumer electronics frequent adopters in Asia. The North American markets are characterized by medical, military, industrial and instrumentation applications.
Make Mine Smaller!
One technology trend has been a vector and can be summed up by the word “smaller.” Plated through-holes used to be considered small at .015” (15 mils). Today they are created with lasers at sizes of .001−.002” and are often plated shut. Conductor traces and spaces struggled to get below .010” then; now, designs with .002” conductors are common. Complementing this trend has been improved soldermask placement accuracy with a locational tolerance of +.002”, base film thickness common at .0005”, and 01005 SMT components (with dimensions of .0157” X .0079”) that are machine-placed at rates of multiple parts per second.
Two technical capabilities driving a significant portion of the improvements are optics and lasers. Using cameras for optical registration has significantly reduced or eliminated the use of punched or drilled tooling holes. Cameras find fiducials and product alignment is factored to create a best fit registration between sequential processes. Lasers are used extensively by laser direct imaging (LDI) equipment with software created by CAD files defining the artwork image during photolithographic exposing. No more 10:1 hand-laid artwork tapes (I won’t mention how long ago that was being practiced)! Lasers are also used extensively to excise circuits from panels and cut film coverlay. Capability is enhanced as laser cutting can be accomplished without traditional restrictions imposed by drill and routing tools.
Get the lead out!
On July 1, 2006, the Restriction of Hazardous Substances (RoHS) mandate was implemented by the European Union, requiring manufacturers of electronic and electrical equipment to reduce/eliminate six hazardous materials. Lead was included in this restriction which meant new methods for circuit board surface treatment and tin/lead soldering had to be invented. Certain dopants used to make printed circuits flame retardant were also prohibited. The industry did a remarkable job of responding with electroless nickel/immersion gold (ENIG) and organic solderability preservatives (OSPs) becoming workhorse surface treatments. Engineers also solved the struggles with lead-free soldering which has become widely adopted and highly reliable.
Get the glue out!
In the world of flexible circuits, adhesiveless laminates have become pervasive. Several technologies are used by multiple suppliers to create copper/polyimide composites sans adhesive. Vacuum deposition of copper onto polyimide, cast polyimide onto copper, and polyimide “adhesives” are used to fabricate these homogenous and high-performance structures.
Several advantages result with improved chemical resistance and improved performance at elevated temperatures. This opportunity to minimize adhesive removes material generally considered to be the weak link in the construction of a multilayer flex circuit. Moisture absorption is reduced making delamination from abrupt or extended temperature exposure less likely.
Made in USA...NOT!
As consumer electronics transitioned to an Asian supply chain, the demand for printed circuit suppliers also shifted East. The growth of notebook computers, digital cameras, and cellphones drove incredible volumes and spawned many high-volume circuit board suppliers. Circuit fabrication technology was often transferred with the cooperation of US manufacturers anxious to get a foothold in a burgeoning market. While that practice has gone away, technical linkage with Asia remains with companies offering brokerage services. Applications engineers in North America serve as technical liaisons between Asian factories and contract manufacturers and/or OEMs. These suppliers buy circuits in Asia and sell in North America.
Product Life Cycle!
The relentless drive of product technology improvements has created new problems and opportunities for flex circuit board suppliers. First to market is often more important than having a better product. With electronic product life estimated at an average of 4−5 years, 20%+ of part numbers are obsoleted annually. Enjoying the ride is not possible (at least not smart) as part number obsolescence is always a threat. A process to constantly and aggressively gather new business is imperative to prevent a circuit company from becoming one of the rusted-out factories scattered like tombstones across the landscape.
Since our industry is always building someone else’s parts, we must exist on what I call “derived demand.” I use this term when my boss wants to know what can be done to increase sales next month since, in the short term, we are at the mercy of our customer’s success stories. With this drive to reduce cycle time, a good way to stay relevant is to compete by being fast. A rapid response is protected from changes in technology. Because, much like in the ‘60s, “The Times They are a-Changing.”
Dave Becker is the V.P. of sales and marketing at All Flex Flexible Circuits and Heaters. To contact Becker, or read past columns, click here.
Editor's Note: This article originally appeared in the March 2017 issue of The PCB Magazine.
Testimonial
"In a year when every marketing dollar mattered, I chose to keep I-Connect007 in our 2025 plan. Their commitment to high-quality, insightful content aligns with Koh Young’s values and helps readers navigate a changing industry. "
Brent Fischthal - Koh YoungSuggested Items
How Good Design Enables Sustainable PCBs
08/21/2025 | Gerry Partida, Summit InterconnectSustainability has become a key focus for PCB companies seeking to reduce waste, conserve energy, and optimize resources. While many discussions on sustainability center around materials or energy-efficient processes, PCB design is an often overlooked factor that lies at the heart of manufacturing. Good design practices, especially those based on established IPC standards, play a central role in enabling sustainable PCB production. By ensuring designs are manufacturable and reliable, engineers can significantly reduce the environmental impact of their products.
50% Copper Tariffs, 100% Chip Uncertainty, and a Truce
08/19/2025 | Andy Shaughnessy, I-Connect007If you’re like me, tariffs were not on your radar screen until a few months ago, but now political rhetoric has turned to presidential action. Tariffs are front-page news with major developments coming directly from the Oval Office. These are not typical times. President Donald Trump campaigned on tariff reform, and he’s now busy revamping America’s tariff policy.
Global PCB Connections: Understanding the General Fabrication Process—A Designer’s Hidden Advantage
08/14/2025 | Markus Voeltz -- Column: Global PCB ConnectionsDesigners don’t need to become fabricators, but understanding the basics of PCB fabrication can save you time, money, and frustration. The more you understand what’s happening on the shop floor, the better you’ll be able to prevent downstream issues. As you move into more advanced designs like HDI, flex circuits, stacked vias, and embedded components, this foundational knowledge becomes even more critical. Remember: the fabricator is your partner.
MKS’ Atotech to Participate in IPCA Electronics Expo 2025
08/11/2025 | AtotechMKS Inc., a global provider of enabling technologies that transform our world, announced that its strategic brands ESI® (laser systems) and Atotech® (process chemicals, equipment, software, and services) will showcase their latest range of leading manufacturing solutions for printed circuit board (PCB) and package substrate manufacturing at the upcoming 17th IPCA Show to be held at Pragati Maidan, New Delhi from August 21-23, 2025.
MKS Showcases Next-generation PCB Manufacturing Solutions at the Thailand Electronics Circuit Asia 2025
08/06/2025 | MKS Instruments, Inc.MKS Inc, a global provider of enabling technologies that transform our world, today announced its participation in Thailand Electronics Circuit Asia 2025 (THECA 2025), taking place August 20–22 at BITEC in Bangkok.