-
- News
- Books
Featured Books
- pcb007 Magazine
Latest Issues
Current IssueInventing the Future with SEL
Two years after launching its state-of-the-art PCB facility, SEL shares lessons in vision, execution, and innovation, plus insights from industry icons and technology leaders shaping the future of PCB fabrication.
Sales: From Pitch to PO
From the first cold call to finally receiving that first purchase order, the July PCB007 Magazine breaks down some critical parts of the sales stack. To up your sales game, read on!
The Hole Truth: Via Integrity in an HDI World
From the drilled hole to registration across multiple sequential lamination cycles, to the quality of your copper plating, via reliability in an HDI world is becoming an ever-greater challenge. This month we look at “The Hole Truth,” from creating the “perfect” via to how you can assure via quality and reliability, the first time, every time.
- Articles
- Columns
- Links
- Media kit
||| MENU - pcb007 Magazine
Estimated reading time: 7 minutes
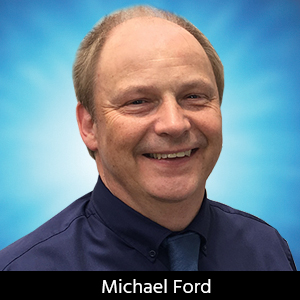
Contact Columnist Form
The Essential Pioneer's Survival Guide: One Size Fits All?
In the same way that we are not all driving the same car, have the same phones, or use the same SMT equipment in our factories, we are unlikely to all end up using a single smart solution or IoT technology. At the car rental counter, you can be confident that you will be able to drive whatever car is available; and in the same way, you should expect all of your factory technology to be interoperable. Choosing the best tool for the job differentiates the business and enhances competitiveness. Decisions on automation, IoT technologies, and software computerizations need to be based on merit because the choices vary considerably. Interoperability is the key for future-proofing, and this is not the time to be waiting for ultimate decisions while others are moving forward.
Humans–Cannot Live Without Them
Even in the wildest imagination of future smart factories, the reality is that humans remain in charge. We are the ones who will still make the fundamental decisions and choices about which technologies to use. We will have to wait I expect until Industry 5.0 to see factories that design, make, and configure themselves. That scenario may not be too far away once 3D printing technology really starts to evolve; but for the foreseeable future, Industry 4.0, which represents the computerized operation of the factory full of automated processes, is dependent on people.
Humans are quite variable entities. In spite of there being billions of us, we rarely see two people who look the same or dress the same. Because of this “human need” for differentiation, there are many variants in all of the stuff that we buy. For example, each car model can have thousands of variants for something that is just a mechanism for moving the fairly standard human form from one location to another. A distant potential relative of mine once thought that a single model in black should be all that we would need.
Many choices for any particular product also is common now in electronics, such as a smartphone or tablet. We carry these personal preferences with us wherever we go, including into our working lives. Ideas that successfully differentiate one operation against another create an immense amount of satisfaction. The need from humans for more personalized electronic products has led to an increasing number of product variations. Also, where once we saw electronics as a stand-alone industry, it is now a critical part of every other industry. As microelectronics move further into different aspects of our lives, new applications of electronics continue to add to the variation which, in some areas, appears to be increasing exponentially.
Intuition, innovation, ideas, and initiative—all of these words starting with “I” characterize qualities that we look for in engineers and managers. The simple fact that there is more than one factory in the world creates competitiveness. Humans are flexible, able to define and create factories that are appropriate for the product profiles that are being created, and for the human customers that they serve.
Following this chain of flexibility, electronics assembly factories have to be flexible to cope with the many different products and variants and to respond to changes in customer delivery demands in the short-term, perhaps even daily in a perfect Industry 4.0 world. This is contrary, however, to the concept and nature of mass production. Because of mass production and associated economies of scale, we have been able to enjoy affordable products of any type. Now, it seems as though we are being pushed backward to the days when most goods were made on a bespoke basis. In this fast-moving, progressive, throw-away culture, the reality is that this is not practical. These are all the causes of the so-called revolution in manufacturing, and the solution is Industry 4.0. Smart Industry 4.0 factories have to be making products on a demand-driven basis but also need to operate in a mass production mode, albeit in a flexible way. This near impossible task cannot be managed by humans, so Industry 4.0 requires us to use computerization to take over the operational decision-making, to guide the products with their associated resources and dependencies dynamically, in real time.
Computerization Without Knowledge
We often hear the comment that there are “too many” providers of SMT and related equipment on the market, often citing lack of growth in the number of “shipped PCBs” or even an overall decline in recent years. This decline is a debatable measurement. I suspect that it comes from data at the PCB fabrication stage; however, it is never really explained. One modern fabricated PCB panel is normally split into a number of smaller PCB boards, just one of which is normally needed per finished product. The number of boards derived from each panel has increased rapidly in recent years as feature and materials sizes have diminished.
But if you take a look around yourself right now, you can see that the electronics industry is not shrinking; instead, there is growth in new applications for electronics. The simple “shipped PCBs” statistic hides a great deal of the detail, of that I am sure. It is like looking out the window to see what the weather is really like versus trusting the generalized weather report on TV, true especially here in the U.K. Such calculations and computerizations lack the accuracy, detail, and timeliness of hard data. Rather than using a purely market financial approach and saying that there are too many providers of equipment; if you take a real look at electronics manufacturing technology, you will see the range of specialist features and equipment that are applicable and necessary in the various aspects of the operation.
Although we may not be confident to always trust the weather report, or the statistics on the “health” of the electronics industry as a whole, factory shop-floor reporting, in most cases, is even worse. With a multitude of choices of equipment selection and the human element of understanding of what might be the best tool for the job, plus the seemingly unending marketing efforts from all of the companies concerned, it is no surprise that even a modest SMT factory operation features a wide variety of types, vendors, and models of equipment. Also, humans are responsible for production management, performance, quality management, supply chain, and various other disciplines that make up the factory. Each person in his or her role has a different expectation of what they want from data and interoperability on the shop floor.
People today in factories are making the transition from being happy to sit and look at the “weather report” to preferring to focus in on the actual detail, cross-referencing it with other data sources from around the factory with “big data” analysis. The core needs of manufacturing management change over time; again, because they are ultimately driven by humans. Computerizations such as those mandated by Industry 4.0 are today and always will be, created by humans, and so they will change and evolve as time goes by, at different times around the factory. The smart factory is not a static entity, any more than regular production is today.
The Practical Evolution of Being “Smart”
Interoperability is the single most important common factor in a smart, flexible factory. Data that describes events needs to be reliable and timely. Machines need to be able to communicate out data related to process and performance and to get information in about products and work orders, as well as feedback from other machines in the line, whether on a machine-to-machine basis or through a smart computerized function. For the deep analysis associated with evolving Industry 4.0 functions, the information requirement is something that also will evolve. It certainly will not be just a simple set of data like what we got with the development of legacy formats such as CAM-X. The importance of any communication standard is that it is open for use by any and all computerizations, not just a simple, basic dataset where more advanced information is contained in proprietary fields that prevent use by anyone other than the specific machine vendor.
Of course, choices for the data format used in a factory will continue to be available. Even the old CAM-X and its intended update from the IPC can work side by side with more open formats such as the Open Manufacturing Language (OML), by using gateways or adaptors in between. As we said, it is important to use the best tool for the job. If only simple information is required, then many choices will be available. OML, however, will continue to be at the forefront of manufacturing IoT technology, continuously supported by a peer group of end-users and vendors (www.omlcommunity.com), to ensure that the maximum value and opportunity can be obtained. We need to allow the human element to thrive on the shop floor and continue to define automation and smart Industry 4.0 computerizations that every factory will be using.
More Columns from The Essential Pioneer's Survival Guide
If It's My Data, I Can Do What I Want, Right?Smart for Smart’s Sake, Part 3: Unification & Traceability
Smart for Smart's Sake, Part 2: Material Management
The 'New Face' of Automotive Traceability
Industry 4.0: Who Benefits?
To Be Lean is to Be Human
Stop the SMT Conspiracy, Part 2: Abduction
The Future of SMT: Welcome to the 4th Dimension