-
- News
- Books
Featured Books
- pcb007 Magazine
Latest Issues
Current IssueInventing the Future with SEL
Two years after launching its state-of-the-art PCB facility, SEL shares lessons in vision, execution, and innovation, plus insights from industry icons and technology leaders shaping the future of PCB fabrication.
Sales: From Pitch to PO
From the first cold call to finally receiving that first purchase order, the July PCB007 Magazine breaks down some critical parts of the sales stack. To up your sales game, read on!
The Hole Truth: Via Integrity in an HDI World
From the drilled hole to registration across multiple sequential lamination cycles, to the quality of your copper plating, via reliability in an HDI world is becoming an ever-greater challenge. This month we look at “The Hole Truth,” from creating the “perfect” via to how you can assure via quality and reliability, the first time, every time.
- Articles
- Columns
- Links
- Media kit
||| MENU - pcb007 Magazine
Estimated reading time: 2 minutes
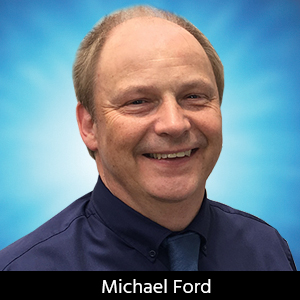
Contact Columnist Form
Industry 4.0: Who Benefits?
Benefits and return on investment (ROI) are not as black-and-white as you might think, and as engineers would like them to be. The reality is that even tangible reductions in cost may not be realized unless enabling factors are in place that allow savings to happen. For example, if an operator’s time in a certain position is reduced by half, it leaves the other half of the operator’s work that must be done, which means that the full reduction in the worker’s time can only be realized if the remainder work can be reliably redistributed across other operators. For an increase in productivity to bring significant change to the bottom-line of a manufacturing business, there must also be the opportunity to increase the business volume to fill the gap. Thus, the intangible side of this equation is scrutinized more as the tangible side diminishes.
The good news is that control and management software for SMT/PCB assembly manufacturing provide different sources of benefit, from which engineers can usually find just a single tangible return that can be enough to justify the purchase of a sophisticated system. However, focus on the vast majority of the rest of the system may be lost. This risk might not be thought through, adding tangible burdens and costs to the other areas of the operation rather than benefits. After installation of a new system, these effects can blow away the benefits that were identified as part of the ROI justification.
After many cycles of this experience have occurred already in most PCB assembly manufacturing companies, people are realizing that innovation and investment in new systems may affect them in ways that are less than optimum, resulting in certain groups within the organization resisting pretty much every major innovation. The real problem is that they often are not wrong.
Now, along comes Industry 4.0, which, whether fully and properly understood or not, will certainly trigger a significant amount of “automated” objection from the shop floor. For those who fully understand the nature of Industry 4.0, which is that automated communication and decision-making happen between pieces of equipment supported by sophisticated software, this can represent a nightmare scenario.
This may be a tough environment in which to introduce innovations, but this does not mean that Industry 4.0 is going to go away. One key reason is that the ideas and principles of Industry 4.0 have been a top-down initiative of the German federal government who were specifically looking for ways to create the computerization of the manufacturing industry. They may perceive Industry 4.0 as a way to reduce the overhead of low-skill labor and to address the competition of low-cost labor resources in other countries.
Editor's Note: This article originally appeared in the July 2015 issue of SMT Magazine.
More Columns from The Essential Pioneer's Survival Guide
If It's My Data, I Can Do What I Want, Right?The Essential Pioneer's Survival Guide: One Size Fits All?
Smart for Smart’s Sake, Part 3: Unification & Traceability
Smart for Smart's Sake, Part 2: Material Management
The 'New Face' of Automotive Traceability
To Be Lean is to Be Human
Stop the SMT Conspiracy, Part 2: Abduction
The Future of SMT: Welcome to the 4th Dimension