A Conversation with Gene Weiner
March 30, 2017 | Barry Matties and Patty Goldman, I-Connect007Estimated reading time: 19 minutes
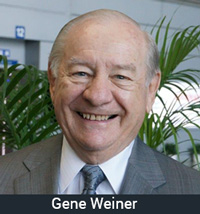
In a discussion following the PCB Executive Forum at IPC APEX EXPO in February, Gene Weiner opened up to Barry Matties and Patty Goldman on the state of the North American electronics industry supply chain and the importance of cooperative efforts up and down that supply chain.
Barry Matties: The first thing that caught my mind for this year’s Executive Forum was attendance; it was disappointing, but OK. In what sense was it okay, and in what sense was it disappointing?
Gene Weiner: It was disappointing in that we had hoped to bring in a total of 50 companies. More than 150 printed circuit companies are not members of IPC, plus all the suppliers, plus those that are members. We allowed nonmember companies to register at the same price as a member company. The IPC also offered an incentive of one year's membership with 75% discount. This was such a great value that I thought it would attract several companies. I was wrong. It didn't motivate a single fabricator to register!
On the other hand, many of these non-member companies constantly complain that the IPC is doing nothing for them. We all know IPC is a volunteer organization and that one gets dividends based upon one’s investment. It was just disappointing. One group of executives that we spoke to in the Midwest area said, "Well, if there was a golf tournament, we may have come." So we checked that out and found that the last time the IPC tried to sponsor a golf tournament, it couldn't raise a foursome—unlike the TCPA or HKPCA which seems to have dozens every time they have one. Additionally, one executive in the Midwest said, "Gee, I wish somebody would've told us that the IPC was revitalizing its bare board programs.” This was in the face of months of publicity and a barrage of promotion activity by the IPC, the press, large networks and members of the IPC’s Hall of Fame.
Matties: I did see that in your summary. Is that just somebody not paying attention to what's going on? Because I thought you did a great job at sharing that story.
Weiner: Yes and no. We had one company say, "The IPC should offer an incentive for me to come.” I said “What do you mean?" and he said, "Well, it should either be free or have an incentive." I said, "Do you know what the IPC is? It's made up of member companies and a hired staff that tries to follow the lead of what the board of directors—which is made up of executives from member companies—wants done to benefit its members. They volunteer their time and their dues go to pay for staff and put on events. Now who do you expect to pay for you or give you an incentive to come, have a free lunch, have a dinner and have a program? All these people are volunteering their time out of their own expenses." He got very angry and said, "Well, they should give me an incentive." That was the end of that. He did not come to the Executive Forum but did attend the (free) exhibits.
Matties: Is there perception that the content itself is not valuable?
Weiner: I don't know. For example, IPC and Mike Carano of RBP Chemical Technology put on an excellent program in advanced troubleshooting.
Matties: This is certainly a logical conclusion based on the fact that the program was available for them to review and they still didn't see enough value. To me, what does that say about our industry? Granted that was one person, but I've heard similar comments along these lines.
Weiner: The program was available to review—for months! These same executives did send their workers to the program, but felt, I guess, that it was beneath them to partake and mix in.
In so doing, they missed some tremendous opportunities to learn from the great presentations—such as the one by Dr. Joan Vrtis, who showed how Multek looks at the industry, how it invests in companies with new ideas—not wanting to take control of them, but just to bring them forward and access future technologies.. They missed Brad Bourne of FTG, who showed exactly what his strategy and plan was for growth and overcoming tough times while he doubled the size of the company since he became its president and CEO. We had the president of WKK Distribution, an American, come all the way from China to explain the business conditions and realities of operating in China. The Department of Commerce presented the results of their recent survey of PCB manufacturers along with many valuable charts and statistics that nobody had seen before. People are still poring over them and looking forward to the rest of the report when it's issued, and the interpretation thereof.
I guess that the disappointment goes to the leadership and egos of a number of the smaller companies who currently seem to be “making money” and are in a comfort zone. I also believe it shows a lack of foresight. Nothing is forever. Everything has a beginning and an ending. I believe that the behavior of these individuals will shorten the lives of their companies.
I noted that several major supplier companies were there. The Forum’s panel was composed solely of company presidents and leaders that were willing to answer any and all questions about their business, whether it was Colonial Circuits, IEC, Flexible Interconnect Technology [FIT), IMI or Chemcut. They were all there. They answered all the questions. They didn't dodge. They spoke out. They provided valuable input.
A number of attendees volunteered to be on the committee next time to help enhance the program further and make sure it meets their and the industry’s needs. The view of these successful industry leaders is obviously quite different than those that were “missing.” One of the IPC’s Board of Directors who attended the executive Session even commented on how good it was and later brought printed circuit company executives over to me to chat about how good the meeting was and how he felt it rejuvenated the fabricator’s management programs. That was refreshing.
Matties: Is the 2017 Executive Forum a retooling of a past program, or is it just a continuation of a program that's in place?
Weiner: It was more than a retooling of the Technical Marketing Research Council, which held concurrently both EMS and bare board sessions that joined together later in the day. These were tremendous successes. Since then, the nature of the industry has changed as has the membership of the IPC . It was my thought, along with the thoughts of other members of the Hall of Fame, not to retool but to re-ignite and re-form the concept for executives at senior management levels to bring them up to date as to what was available, and to help them confront the changes happening in the industry on a global basis. For example, we're more integrated vertically in packaging and more changes are coming. I just read this morning where Xiaomi, a major smartphone maker in China, is going to make their own chipsets now. They're going to compete with Qualcomm and others. These are big changes that we have to face.
The idea was to help people become aware of these changes, to see how the successful companies confronted and overcame these, how they continue to grow, how to make a profit, and the fact that collaboration is needed. That was one of the big things in Joan Vrtis’ presentation, as well as the panelist, Shawn Stone, of IEC. The fact that you have to look at new markets with your technology. This was also the view of Rick Lies of Chemcut, who broadened his product offerings and markets to survive and grow. This goes back to the concept of redefining boundaries in Blue Ocean Strategy published in 2005; such as the famous Canadian circus, which redefined what a circus was and was a huge success with Cirque du Soleil. The concept is still valid!
I believe that we accomplished the goals we established (except for attendance). I hope that the IPC decides to continue its efforts to enhance management training through future PCB Executive Forums.
Matties: Do you think there's a new wave of participation in that there's a new sense of manufacturing might, if you will, that's taking hold in America?
Weiner: I do think there's a new wave of manufacturing and it's different, because it includes software, the all-pervasive Internet of Things. In fact, I jokingly said to Joan Vrtis after her presentation, "How do I get disconnected today?" There are members of the industry and the IPC that are disconnected. Loyalties have receded along with the increase of “hands-off” approaches to purchasing. The result has changed to the cooperative approach of today. There was a time when you'd see companies working one-on-one to solve problems or develop new products, but things are so broad now and so complicated that you do need a cooperative effort up and down the supply chain. This has resulted in the rise of consortia.
Matties: What are your thoughts when you see people like Alex Stepinski creating the new factories of today here in America?
Weiner: First, I believe that he’s an absolute genius and an original thinker. Second, he had the proper support of a captive operation. Third, he's very creative and he knew how to bring different companies together to create a smooth operating facility. He’s fostered cooperation between a number of companies. He innovated and tried new concepts and equipment. He didn't just plug in the best of everything he saw. He changed it, he integrated it.
This is one of the messages I was trying to bring forward: the need for cooperation by the smaller companies to offset the activities of larger ones integrating more fully as they focused on the bigger customers. The remainder must get together. In fact, I have proposed several times the idea of a buyers’ cooperative to help the smaller companies get a better price on some of the materials that they need. That coupled with a consortia to test products can provide a “leg up” on future business opportunities.
We still have a problem with attracting enough young people to our industry. We have to increase our outreach beyond the colleges to high schools. The outreach by NextFlex to such universities as the University of Connecticut is a good example of outreach to college levels. Today we have to “sell” the excitement of our industry to our youth. We have to offer young people the excitement and challenge of creating new things through software and robotics, not just etching a printed circuit board or plating it, but looking at the system approach. You must be able to offer our youth new styles of working such as telecommuting, of which I'm a proponent of—and you certainly are.
I've been thinking about this ever since the meeting as to what worked and what didn't. Patty, you heard in the breakfast meeting when I said there were three types of circuit people: those that you're never going to convince, those that have to be willing to adapt and modify, and those that came. What is still astounding to me is not one single company took up the widely-publicized offer of a year of IPC membership for $300. They would've blown through that in a bar that night easily.
Matties: What does that say about the value offering that IPC is bringing out there even at that price?
Weiner: I think the value offering is great. I think that those who are not members just don't recognize it, won't accept it, or are too self-focused; perhaps they may not be here in the future, where those that attended were the guys that are growing and are already members. It's unfortunate, but that's the way it is. For example, someone bragged they had a couple dozen people at the last IMPACT event in Washington. We had 30–35 people, including staff, of course. We used to draw 75 to 100 and more to those events back when it was Capitol Hill Day.
Matties: Those were the days though, when we still had a couple thousand board shops, right?
Weiner: Right, that's why it's so much more important to have the remaining ones cooperate.
Matties: Patty, you covered IMPACT Washington, D.C. last year, and that is a topic I want to touch on here. How many participants did we have last year?
Patty Goldman: Not as many as we should have had.
Weiner: I heard that there were about 35 including IPC staff.
Goldman: I can believe that.
Page 1 of 2
Testimonial
"Advertising in PCB007 Magazine has been a great way to showcase our bare board testers to the right audience. The I-Connect007 team makes the process smooth and professional. We’re proud to be featured in such a trusted publication."
Klaus Koziol - atgSuggested Items
How Good Design Enables Sustainable PCBs
08/21/2025 | Gerry Partida, Summit InterconnectSustainability has become a key focus for PCB companies seeking to reduce waste, conserve energy, and optimize resources. While many discussions on sustainability center around materials or energy-efficient processes, PCB design is an often overlooked factor that lies at the heart of manufacturing. Good design practices, especially those based on established IPC standards, play a central role in enabling sustainable PCB production. By ensuring designs are manufacturable and reliable, engineers can significantly reduce the environmental impact of their products.
50% Copper Tariffs, 100% Chip Uncertainty, and a Truce
08/19/2025 | Andy Shaughnessy, I-Connect007If you’re like me, tariffs were not on your radar screen until a few months ago, but now political rhetoric has turned to presidential action. Tariffs are front-page news with major developments coming directly from the Oval Office. These are not typical times. President Donald Trump campaigned on tariff reform, and he’s now busy revamping America’s tariff policy.
Global PCB Connections: Understanding the General Fabrication Process—A Designer’s Hidden Advantage
08/14/2025 | Markus Voeltz -- Column: Global PCB ConnectionsDesigners don’t need to become fabricators, but understanding the basics of PCB fabrication can save you time, money, and frustration. The more you understand what’s happening on the shop floor, the better you’ll be able to prevent downstream issues. As you move into more advanced designs like HDI, flex circuits, stacked vias, and embedded components, this foundational knowledge becomes even more critical. Remember: the fabricator is your partner.
MKS’ Atotech to Participate in IPCA Electronics Expo 2025
08/11/2025 | AtotechMKS Inc., a global provider of enabling technologies that transform our world, announced that its strategic brands ESI® (laser systems) and Atotech® (process chemicals, equipment, software, and services) will showcase their latest range of leading manufacturing solutions for printed circuit board (PCB) and package substrate manufacturing at the upcoming 17th IPCA Show to be held at Pragati Maidan, New Delhi from August 21-23, 2025.
MKS Showcases Next-generation PCB Manufacturing Solutions at the Thailand Electronics Circuit Asia 2025
08/06/2025 | MKS Instruments, Inc.MKS Inc, a global provider of enabling technologies that transform our world, today announced its participation in Thailand Electronics Circuit Asia 2025 (THECA 2025), taking place August 20–22 at BITEC in Bangkok.