-
- News
- Books
Featured Books
- pcb007 Magazine
Latest Issues
Current IssueInventing the Future with SEL
Two years after launching its state-of-the-art PCB facility, SEL shares lessons in vision, execution, and innovation, plus insights from industry icons and technology leaders shaping the future of PCB fabrication.
Sales: From Pitch to PO
From the first cold call to finally receiving that first purchase order, the July PCB007 Magazine breaks down some critical parts of the sales stack. To up your sales game, read on!
The Hole Truth: Via Integrity in an HDI World
From the drilled hole to registration across multiple sequential lamination cycles, to the quality of your copper plating, via reliability in an HDI world is becoming an ever-greater challenge. This month we look at “The Hole Truth,” from creating the “perfect” via to how you can assure via quality and reliability, the first time, every time.
- Articles
- Columns
- Links
- Media kit
||| MENU - pcb007 Magazine
Estimated reading time: 2 minutes
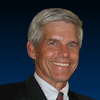
All About Flex: Flex Circuit Stiffeners
Many flexible circuit designs require selectively bonded stiffeners…they’re just too flexible! Stiffener materials can be any number of materials, but they are usually polyimide films or FR-4 glass/epoxy substrates and are available in a wide variety of thicknesses. Three-dimensional metal stiffeners may also be attached for thermal dissipation properties. The purpose of a stiffener is to rigidize or structurally support discrete areas of the flexible circuit.
The following are some common purposes for flexible circuit stiffeners:
- Zero Insertion Force (ZIF) connectors: This is probably the most popular connectorization method seen with flexible circuits. The insertion end requires adequate structural support and thickness to fully engage with the mating ZIF connector.
- SMT or through-hole components: Stiffeners will help prevent mechanical bending or flexing near soldered components. Bending that occurs near a solder joint can create stress concentration at the junction of the trace and the cover insulation. This mechanical force is a risk to fracture a circuit trace, causing an intermittently open circuit.
- Mechanical strength: Stiffeners can provide mechanical support that protects the thin circuit film and component from damage in applications where certain areas of the circuit assembly are subject to mechanical wear.
- Selectively rigidizing: Stiffeners can keep certain areas of a flexible circuit flat and stable. For example, a mechanical actuator may need a firm, flat surface to function properly.
- Adding thickness: It is often desirable to add to the surface profile in certain areas of the flexible circuit to “match up” with other parts of the electronic assembly.
- Facilitate handling: Flexible circuits are thin and flimsy and can be difficult to handle. Adding a selective stiffener can make it easier to assemble the circuit into an end state electronic package. This may include integrating the stiffener(s) as part of a carrier used to facilitate SMT assembly.
A wide variety of adhesives are used to bond stiffeners to the flex circuit substrate. The two main types of adhesive generically fall into the categories of pressure sensitive adhesives (PSA) and thermally bonded adhesives. Varieties of each are available to meet specific performance requirements for thermal exposure, chemical resistance, and adhesion to various materials. Pressure sensitive adhesives are applied with minimal contact pressure and do not require heating to enhance the bond. Circuits are shipped with the PSA attached and protected by a low tack release liner that is removed when the nest level assembly occurs. PSA bonding is often an economical solution but highest bond strength is generally achieved with thermally cured materials. Thermal-bonded adhesives offer a much stronger and more permanent bond, but require a hydraulic press to achieve temperatures and pressures for attachment. Applications requiring high-temperature exposure will most often specify thermally bonded adhesives.
While stiffeners can be discretely applied to a single flexible circuit, it is usually more efficient to bond an oversized routed stiffener array to a flexible circuit panel. The final dimensions of the stiffener location are often defined coincident with the circuit cutline when the circuit is excised from the manufacturing panel. Bonding routed stiffener arrays is frequently adopted when component assembly is done in panel form. The ideal size and configuration for the stiffener array depends on several factors. Nesting density for panel fabrication needs to be balanced against optimum subpanel layouts used for SMT efficiency during component assembly. This tradeoff is done most economically when there is close cooperation between the circuit fabricator and the assembly supplier.
Dave Becker is vice president of sales and marketing at All Flex Flexible Circuits LLC.
More Columns from All About Flex
All About Flex: Terms and ConditionsAll About Flex: ISO 9001 Basics
All About Flex: FAQs on UL Listings for Flexible Circuits
All About Flex: Avoiding Trace Fracturing in a Flexible Circuit
Polyimide vs. Silicone for Flexible Heaters
All About Flex: Copper Thickness Requirements for Flex Circuits
All About Flex: Copper Grain Direction
All About Flex: Options for Purchasing Flexible Heaters