-
-
News
News Highlights
- Books
Featured Books
- smt007 Magazine
Latest Issues
Current IssueSpotlight on India
We invite you on a virtual tour of India’s thriving ecosystem, guided by the Global Electronics Association’s India office staff, who share their insights into the region’s growth and opportunities.
Supply Chain Strategies
A successful brand is built on strong customer relationships—anchored by a well-orchestrated supply chain at its core. This month, we look at how managing your supply chain directly influences customer perception.
What's Your Sweet Spot?
Are you in a niche that’s growing or shrinking? Is it time to reassess and refocus? We spotlight companies thriving by redefining or reinforcing their niche. What are their insights?
- Articles
- Columns
- Links
- Media kit
||| MENU - smt007 Magazine
Fixturing: Key to Accurate Flex Circuit Assembly
April 17, 2017 | Stephen Las Marias, I-Connect007Estimated reading time: 3 minutes
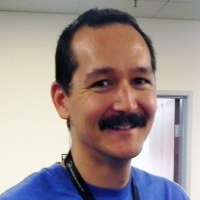
Adrian Nishimoto, operation manager at Spectrum Assembly Inc. (SAI), talks about the critical factors to consider during flex circuit assembly, such as fixturing and accurate thermal profiling. He also mentions why jet printers are suitable for use in assembling flex circuits.
Stephen Las Marias: What do you think are the major challenges in flex circuit assembly?
Adrian Nishimoto: Making our customers realize that fixturing is an integral part of successfully building flex circuits. We need good 3D Solidworks files, CAD or Gerber data to design carriers able to provide a rigid surface as the flex circuits go through stencil printing, pick-and-place and reflow. In some cases, we also use specialized carriers for aqueous wash system.
Las Marias: Please talk about specific steps in the flexible circuit assembly process that have the biggest effect on yields.
Nishimoto: Having tooling holes that keep the flex substrate rigid in a fixture during stencil printing and pick-and-place ensures better solder paste accuracy and component placement accuracy. The goal is to keep it flat and keep it from moving during these processes. The carrier is also critical if you have any type of conveyor system handling PCBAs in production.
Las Marias: How do you address these challenges? Does the process require different parameters?
Nishimoto: In addition to the fixturing considerations we’ve mentioned, accurate thermal profiling is also necessary. The carrier’s thermal mass impact—the ability to absorb and store heat—needs to be taken into consideration. We do have our suppliers drill material out of the carrier to make them more web-like and less of a heatsink. That said, there isn’t a one-size-fits-all solution to profiling because flex circuits come in all size ranges and that changes the optimum profile.
Las Marias: How does flex circuit assembly differ from standard PCB assembly?
Nishimoto: Because the material is flexible, all secondary operations need to use extra care in processing. If there are ceramic capacitors or other large ICs, it becomes important to make sure that the substrate is not flexed in handling because that will damage the solder joint.
Las Marias: What about the challenges with respect to flexible circuit materials?
Nishimoto: We don’t see any challenges as long as we can create a fixture to keep it rigid.
Las Marias: Do customers call out a specific brand name of material to use when dealing with flexible printed circuits?
Nishimoto: There is no specific brand name of material called out. In some cases, the substrate is exotic, but most are polyimide materials. Some customers specify the supplier on the approved vendor list, but in many cases, they depend on us to identify suppliers and give them choices to qualify that meet their requirements in terms of material performance and lead-time.
Las Marias: Which practice has the greatest impact on the quality of flexible circuit assemblies?
Nishimoto: Following industry-standard best practices in initial design and layout. Since flex circuits are folded up and put in tight enclosures, it is important to reduce points of failure, such as the location of points of interconnect. For example, a really long connector may require a rigid flex design, which uses stiffener rather than a 100% flex design.
Las Marias: In which end markets are you seeing increasing use of flexible circuits?
Nishimoto: Primarily, we are seeing them in medical and consumer applications.
Las Marias: What are the key things for OEMs to consider when choosing an assembly partner for flexible circuit assemblies/projects?
Nishimoto: First is prior experience with flex circuit assembly. Then, they should have a good relationship with one or more board carrier fabricators. Lastly, they should have an expertise in thermal profiling in reflow and strong discipline in work-in-process handling practices.
Las Marias: Are there new technologies out there that will significantly impact or benefit the flexible circuit assembly process?
Nishimoto: When you have rigid-flex combinations or stiffeners in use, you have two different heights—which makes it impossible to screen print without specialized fixturing. Paste jet printers like the MY500 we use are more adjustable and do not have that constraint because it allows us to tailor the amount of solder on individual components without the use of a stencil.
Las Marias: Thank you, Adrian.
Nishimoto: Thank you.
This article was originally published in the March 2017 issue of SMT Magazine.
Testimonial
"Advertising in PCB007 Magazine has been a great way to showcase our bare board testers to the right audience. The I-Connect007 team makes the process smooth and professional. We’re proud to be featured in such a trusted publication."
Klaus Koziol - atgSuggested Items
Altus Supports Datalink Electronics with Advanced Selective Soldering Solution to Boost Manufacturing Efficiency
09/02/2025 | Altus GroupDatalink Electronics has partnered with Altus Group to integrate a cutting-edge automated soldering solution, enhancing its production capabilities and reinforcing its strategic focus on quality, automation, and scalability.
Connect the Dots: How to Avoid Five Common Causes of Board Failure
09/03/2025 | Matt Stevenson -- Column: Connect the DotsBoards fail for various reasons, and because I’ve been part of the PCB industry for a long time, I’ve seen most of the reasons for failure. As part of my ongoing crusade to help designers design for the reality of manufacturing, here are five common causes for board failure and how to avoid them.
More Than a Competition: Instilling a Champion's Skill in IPC Masters China 2025
09/01/2025 | Evelyn Cui, Global Electronics Association—East AsiaNearly 500 elite professionals from the electronics industry, representing 18 provinces and municipalities across China, competed in the 2025 IPC Masters Competition China, March 26–28, in Pudong, Shanghai. A total of 114 contestants advanced to the practical competition after passing the IPC Standards Knowledge Competition. Sixty people competed in the Hand Soldering and Rework Competition (HSRC), 30 in the Cable and Wire Harness Assembly Competition (CWAC), and 24 in the Ball Grid Array/Bottom Termination Components (BGA/BTC) Rework Competition.
Indium Promotes Huang to Senior Manager, Marketing Communications
08/28/2025 | Indium CorporationWith its commitment to innovation and growth through employee development, Indium Corporation announces the promotion of Jingya Huang to Senior Manager, Marketing Communications, to continue to lead the company’s branding and promotional efforts.
Rehm Academy Expands Its Training Program
08/28/2025 | Rehm Thermal SystemsThe demands on modern industrial companies and employees continue to rise, and therefore, the topic of further education is becoming increasingly important today.