-
- News
- Books
Featured Books
- pcb007 Magazine
Latest Issues
Current IssueSales: From Pitch to PO
From the first cold call to finally receiving that first purchase order, the July PCB007 Magazine breaks down some critical parts of the sales stack. To up your sales game, read on!
The Hole Truth: Via Integrity in an HDI World
From the drilled hole to registration across multiple sequential lamination cycles, to the quality of your copper plating, via reliability in an HDI world is becoming an ever-greater challenge. This month we look at “The Hole Truth,” from creating the “perfect” via to how you can assure via quality and reliability, the first time, every time.
In Pursuit of Perfection: Defect Reduction
For bare PCB board fabrication, defect reduction is a critical aspect of a company's bottom line profitability. In this issue, we examine how imaging, etching, and plating processes can provide information and insight into reducing defects and increasing yields.
- Articles
- Columns
- Links
- Media kit
||| MENU - pcb007 Magazine
Estimated reading time: 3 minutes
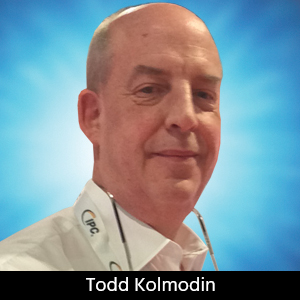
Testing Todd: Go With the Flow
In today’s testing theatre, the flow of information from the OEMs and manufacturers to the independent contractors is mission-critical. Missing information can cause delays, incorrect processing and ultimately scrap or end user rejection of the product. The buzz term being used a lot today is “flow-down.” It pretty much describes itself: It is the flow of information down the supply chain. So let’s go with the flow, shall we? We will break it down in the flow required for correct electrical testing of an unpopulated printed wiring board.
1. The OEM designs the latest must-have innovation for the market. Time is critical to get this product built, tested and on the shelves so that little Johnny will not be disappointed on his upcoming birthday. Now, the design engineers have painstakingly designed in all the impedance, IC footprints, material requirements, impedance/inductance and resistive components, and have written it in their design specification document. Since this is a new product and top secret the document is then saved at their top secret secure location (along with the notorious 11 herbs and spices).
2. The OEM procurement department now receives the build request from the engineers and proceeds to shop vendors for manufacturing. They may send out many RFQs and each time they need to be specific on what they want manufactured. Here is the first major flow-down example: When the RFQ goes out they must be very specific on what they wish to receive. Information here are the general manufacturing requirements (IPC-6011, IPC-6012) but also the specifics that may be outlined in the top-secret design specification document the engineers created in section 1. What are the special requirements for characteristic impedance, dielectric breakdown, continuity and isolation? What is the performance class expectation? Does this board need to pass military performance specifications?
(Mil-PRF-31032, 55110 or 50884 as examples.) These all need to be specified up front for the proper quotation to be generated.
3. Now that a suitable manufacturer has been selected the OEM issues a procurement document (PO) and the final design package. This now goes through the tooling process at the manufacturer. It is critical here that all specific information outlined in steps 1 and 2 are flowed down in the manufacturing order that will run the course of the manufacturing floor. It is important to remember it is difficult as the flow-down increases in steps that it will be more difficult and time-consuming to retrace steps to find important information that is missing in your current area. This can lead to delays and mistakes. So the information from the PO design specification and industry/military specifications need to be flowed-down.
4. Now that the flow-down has worked as it should, the product reaches electrical test and is ready for screening. If proper flow-down has been achieved the technicians will have the important information available for processing:
A. Part number
B. PO number
C. Order number
D. Date code
E. Performance class requirement
F. Voltage, continuity and isolation requirement
G. Indirect vs direct testing directive
H. Serialization requirement
I. Military requirement (if applicable)
J. Dielectric breakdown requirement
5. When ET is complete and the product goes to final inspection prior to shipping the flow-down information can be reconciled to the original PO and design specifications. The requirements have been flowed-down through the entire process so no required information is lacking. The product ships on time and little Johnny from step 1 (remember him?) receives his birthday gift on time and in perfect condition and working order.
Todd Kolmodin is the vice president of quality for Gardien Services USA, and an expert in electrical test and reliability issues. To read past columns, or to contact Kolmodin, click here.
Editor's Note: This article originally appeared in the April 2017 issue of The PCB Magazine, click here.
More Columns from Testing Todd
Testing Todd: Why 4-wire Kelvin?Testing Todd: Why TDR?
Testing Todd: Positivity Boosts Employee Morale
Testing Todd: Preparing Employees for the Long Haul
Testing Todd: Where Can We Improve?
Testing Todd: Turning Into the Wind
Testing Todd: Coming Back to Life—Design Recovery
Testing Todd: Decision Time—Invest or Delegate?