-
- News
- Books
Featured Books
- pcb007 Magazine
Latest Issues
Current IssueSales: From Pitch to PO
From the first cold call to finally receiving that first purchase order, the July PCB007 Magazine breaks down some critical parts of the sales stack. To up your sales game, read on!
The Hole Truth: Via Integrity in an HDI World
From the drilled hole to registration across multiple sequential lamination cycles, to the quality of your copper plating, via reliability in an HDI world is becoming an ever-greater challenge. This month we look at “The Hole Truth,” from creating the “perfect” via to how you can assure via quality and reliability, the first time, every time.
In Pursuit of Perfection: Defect Reduction
For bare PCB board fabrication, defect reduction is a critical aspect of a company's bottom line profitability. In this issue, we examine how imaging, etching, and plating processes can provide information and insight into reducing defects and increasing yields.
- Articles
- Columns
- Links
- Media kit
||| MENU - pcb007 Magazine
Fabricators Speak Out on High-Speed Materials
April 18, 2017 | Barry Matties and Patty Goldman, I-Connect007Estimated reading time: 2 minutes
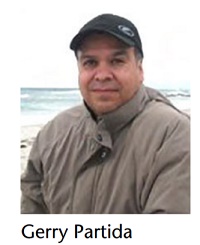
Recently, I-Connect007 Publisher Barry Matties and his editorial team joined with two PCB fabricators to discuss the state of advanced materials. The meeting included Gerry Partida, director of engineering at Summit Interconnect and Joe Menning, program manager at All Flex Flexible Circuits. The discussion centered on the processes, challenges, and procurement of high-speed materials, as well as need to work with customers during the design stage.
Patty Goldman: We are here to talk about high performance and high-speed materials. We’ve spoken with a few laminate suppliers, but we also wanted to get the viewpoint of the guys making the boards. We asked you to join us so we can find out how fabricators are dealing with these materials, what you need from suppliers, what you think our readers should know about advanced materials.
Barry Matties: When we start talking about highspeed materials, what are the greatest challenges you face with high-speed materials, from procurement to processing and delivery? Maybe even from OEMs specifying materials or not? Gerry, why don’t we start with you.
Gerry Partida: Thank you for allowing us to share this. This is very important stuff. A lot of the RF materials are very hard to register when you laminate or process the materials. There are many RF materials that are not glass-reinforced or very loosely glass-reinforced. When we planarize the material for epoxy fill, or blind via lamination structures and we epoxy fill, the material stretches out. We call some of it bubble gum because you can just distort the material as you planarize an epoxy-filled via. Also, the material just moves a lot, in some cases three times greater than standard glass-reinforced epoxy materials.
That’s one of the biggest challenges—maintaining registration and controlling it, knowing where it’s going to end up. The material is very expensive. I like to use the analogy with people that building FR-4 boards, regular, digital or something that’s straightforward versus an RF board is like playing craps. The difference between FR-4 boards and RF boards is that the FR-4 boards are like playing craps Saturday night in Laughlin, Nevada, which is a $5 minimum bet, where RF is like playing the Bellagio at 9 o’clock on Saturday night where the minimum bet is $25. Same rules, same game, but the buyin is huge because of the registration and the other fun stuff that goes with it. You can lose fast or you can win a lot.
That’s one of the greatest challenges—the material itself, its softness, its registration, as well as processing. One of the things is holding registration and the material. The other parts that are a challenge for the materials are the ability to deposit electroless and maintaining peel strength. A lot of them have low peel strength. Many RF materials can have smear.
We call it flat, but it’s smear when you drill and you cover the inner face of an innerlayer pad; it violates the IPC-6012 rigid PCB performance spec. It’s allowed somewhat in IPC-6018, the performance spec for high-frequency/microwave PCBs—but smear is always a concern on a lot of high-speed materials.
Some of the other challenges with materials are Teflon or PTFE surfaces, where you have to do special treatment to get the solder mask or legend to stick to it.
To read the full version of this interview which appeared in the April 2017 issue of The PCB Magazine, click here.
Suggested Items
Silicon Mountain Contract Services Enhances SMT Capabilities with New HELLER Reflow Oven
07/17/2025 | Silicon Mountain Contract ServicesSilicon Mountain Contract Services, a leading provider of custom electronics manufacturing solutions, is proud to announce a significant upgrade to its SMT production capability with the addition of a HELLER 2043 MK5 10‑zone reflow oven to its Nampa facility.
Knocking Down the Bone Pile: Addressing End-of-life Component Solderability Issues, Part 4
07/16/2025 | Nash Bell -- Column: Knocking Down the Bone PileIn 1983, the Department of Defense identified that over 40% of military electronic system failures in the field were electrical, with approximately 50% attributed to poor solder connections. Investigations revealed that plated finishes, typically nickel or tin, were porous and non-intermetallic.
SHENMAO Strengthens Semiconductor Capabilities with Acquisition of PMTC
07/10/2025 | SHENMAOSHENMAO America, Inc. has announced the acquisition of Profound Material Technology Co., Ltd. (PMTC), a premier Taiwan-based manufacturer of high-performance solder balls for semiconductor packaging.
KYZEN to Highlight Understencil and PCB Cleaners at SMTA Querétaro Expo and Tech Forum
07/09/2025 | KYZEN'KYZEN, the global leader in innovative environmentally responsible cleaning chemistries, will exhibit at the SMTA Querétaro Expo & Tech Forum, scheduled to take place Thursday, July 24, at Centro de Congresos y Teatro Metropolitano de Querétaro.
Driving Innovation: Direct Imaging vs. Conventional Exposure
07/01/2025 | Simon Khesin -- Column: Driving InnovationMy first camera used Kodak film. I even experimented with developing photos in the bathroom, though I usually dropped the film off at a Kodak center and received the prints two weeks later, only to discover that some images were out of focus or poorly framed. Today, every smartphone contains a high-quality camera capable of producing stunning images instantly.