-
- News
- Books
Featured Books
- smt007 Magazine
Latest Issues
Current IssueWhat's Your Sweet Spot?
Are you in a niche that’s growing or shrinking? Is it time to reassess and refocus? We spotlight companies thriving by redefining or reinforcing their niche. What are their insights?
Moving Forward With Confidence
In this issue, we focus on sales and quoting, workforce training, new IPC leadership in the U.S. and Canada, the effects of tariffs, CFX standards, and much more—all designed to provide perspective as you move through the cloud bank of today's shifting economic market.
Intelligent Test and Inspection
Are you ready to explore the cutting-edge advancements shaping the electronics manufacturing industry? The May 2025 issue of SMT007 Magazine is packed with insights, innovations, and expert perspectives that you won’t want to miss.
- Articles
- Columns
- Links
- Media kit
||| MENU - smt007 Magazine
The Challenge of Filling PCB Assembly Positions
May 5, 2017 | John Talbot, Tramonto CircuitsEstimated reading time: 9 minutes
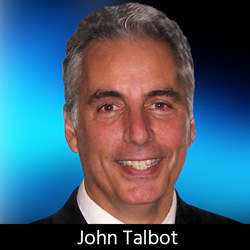
It is not a secret that U.S. manufacturers have a difficult time filling open positions. It has been reported for several years and the topic comes up frequently. There are many opinions why this is so. The main topic reported is that manufacturers cannot find workers with the necessary skills to fill the openings. If we look specifically at the PCB assembly industry, the rhetoric is similar. There are more openings than people to fill them. The discussions reveal that lower wages, lack of skills, and sometimes the reported low unemployment rate in the United States is part of the problem.
Larger companies, it seems, have an easier time filling positions than smaller companies because of their ability to pay higher wages; however, they suffer the same difficulties with lack of skills and loyalty. It was reported in a book titled “Men Without Work,” by Nicholas Eberstadt, that 8–10 million working-age (25–54) U.S. males have disappeared from the workforce and many, if not most, have given up looking for work. That may be a factor. Whatever the reason, employers find it challenging to fill open positions, which makes it difficult to grow and keep up with their customer’s demands. Business owners, however, are accustomed to challenges and need to find ways to adjust to the current employment situation.
Does anybody want to work in manufacturing anymore?
There have been articles written that suggest that people don’t choose manufacturing as a career anymore because of the pressure to go to college and get a “real” job. High schools across the U.S. have stopped offering shop classes that exposed our younger generations to vocations that are challenging, skillful, lucrative and fulfilling. Instead their interest lies in what percentage of students are accepted to colleges or universities. This stigma, that manufacturing is not good enough to make a career of, or glamorous enough to tell your neighbors about may have some effect on the current situation.
Then there are those that think that the U.S. cannot compete with the cheap labor of Mexico or China. Whatever the reasons, there are fewer young adults interested in manufacturing than there were 20 years ago. Never mind the fact that everything we use during our daily lives has been manufactured in one way or another.
Let’s examine a few ways that innovative employers have combatted the challenge.
Where do we find candidates?
In a review of traditional methods of finding candidates, we would surely include help-wanted ads online at Monster.com, Indeed.com, CraigsList.com, etc. We must consider staffing agencies that specialize in manufacturing jobs as well. And less relevant in our electronically connected world, the local newspapers.
These tried and true methods that have been trusted in the past surely must be the only way to communicate with interested applicants, right? Well if you’re one of those that have been actively searching for qualified candidates you’ve already realized that this isn’t working well.
The online sites are an easy way to get a job opening posted and hope that somebody reads it is qualified and interested. However, the results are less than exceptional for the printed circuit assembly industry and the manufacturing industry in its entirety.
The staffing agencies don’t fare much better. Anybody who has discussed their difficulties with an agency representative has heard that they have the same issues. Or they will tell you that they have many qualified candidates, but after filling out their necessary paperwork and agreeing to an “onsite review” of your workplace you don’t hear from them again. And why not? If it’s difficult to find employees for the manufacturers it stands to reason that it is hard for the agencies as well. It may be time to step out of the box.
Skills or culture: which is most important?
Jobs in the PCB assembly industry are unarguably skilled positions. Whether they will hand solder all day or program pick-and-place equipment for automated soldering, their skills are vital. The components that we ask them to solder get smaller every year, and it is not unusual these days to be asked to inspect, re-work and solder components that are .040” x .020” and smaller. They must be steady handed and as familiar with a microscope as they are with their solder iron and tweezers.
However, we also want candidates to fit into the company culture. It’s important for all employees to be comfortable and happy working together. The culture of the company takes a long time to be established and one cannot put a value on that. Any company that survives for an extended amount of time does so because of its employees.
Thankfully for those of us in the PCB assembly industry, we have the IPC standards to guide our way. The IPC has a time-tested training procedure that works individually or on entire teams. This affords us a positive benefit of not having to find candidates with both the skills and character to fit the position.
So, do we hire skills? Or do we hire culture? If the candidate has both, then this is not a question. However, if we can interview candidates that are interested in the position, but don’t have the skills as well as those that are skilled, we’ve increased the number of candidates that we can review. We also have the confidence that these candidates can be trained sufficiently to fill the position. This method requires us to understand that the candidate will not be valuable the day they start. Training takes time and of course a lot of practice. It requires a big commitment for the company and the employee to agree to employment without skills.
Once you’ve found them, how do you hire them?
Once you’ve found a worthy candidate, you’ve got to make them an offer that will result in a positive reaction. Some companies don’t struggle with this part of the hiring procedure. The smaller companies though, do. There’s a lot to consider. For instance, if you’ve found a skilled person that fits well into the culture, you must be able to offer them a package that is a step up from their current position if you hope to convince them of a change.
If you’ve chosen an un-skilled person you must balance the cost of training with the cost of normal employment and still make it lucrative for both. It’s a difficult position to be in for the smaller companies, but a necessary one. We’ve already acknowledged that our companies would not be successful if not for our employees. That includes our newest employees.
Training: Pros & Cons
If your company must consider a training program, and I suggest every company does, you will have concerns that must be reviewed, discussed and agreed to internally. Any training program will be costly and time consuming. It will require either sending the employee offsite for a week or more, or if you’re committed to the process you may have an IPC certified trainer on your team. In which case, it will require two of your employees be out for at least one week.
There are positives and negatives to consider with both options. If you choose to send the employee away to get the training you will endure the costs each time and experience inconsistency because the trainers are different each time. If you choose to have someone internally qualified as a trainer then the costs will be less, but you’ll also lose one of your top employees for an entire week for training. However, each employee will be trained consistently and with a slant toward the way your company wants things done. It helps to not have to unlearn practices learned from an outside trainer.
Page 1 of 2
Suggested Items
Driving Innovation: Direct Imaging vs. Conventional Exposure
07/01/2025 | Simon Khesin -- Column: Driving InnovationMy first camera used Kodak film. I even experimented with developing photos in the bathroom, though I usually dropped the film off at a Kodak center and received the prints two weeks later, only to discover that some images were out of focus or poorly framed. Today, every smartphone contains a high-quality camera capable of producing stunning images instantly.
Hands-On Demos Now Available for Apollo Seiko’s EF and AF Selective Soldering Lines
06/30/2025 | Apollo SeikoApollo Seiko, a leading innovator in soldering technology, is excited to spotlight its expanded lineup of EF and AF Series Selective Soldering Systems, now available for live demonstrations in its newly dedicated demo room.
Indium Corporation Expert to Present on Automotive and Industrial Solder Bonding Solutions at Global Electronics Association Workshop
06/26/2025 | IndiumIndium Corporation Principal Engineer, Advanced Materials, Andy Mackie, Ph.D., MSc, will deliver a technical presentation on innovative solder bonding solutions for automotive and industrial applications at the Global Electronics A
Fresh PCB Concepts: Assembly Challenges with Micro Components and Standard Solder Mask Practices
06/26/2025 | Team NCAB -- Column: Fresh PCB ConceptsMicro components have redefined what is possible in PCB design. With package sizes like 01005 and 0201 becoming more common in high-density layouts, designers are now expected to pack more performance into smaller spaces than ever before. While these advancements support miniaturization and functionality, they introduce new assembly challenges, particularly with traditional solder mask and legend application processes.
Knocking Down the Bone Pile: Tin Whisker Mitigation in Aerospace Applications, Part 3
06/25/2025 | Nash Bell -- Column: Knocking Down the Bone PileTin whiskers are slender, hair-like metallic growths that can develop on the surface of tin-plated electronic components. Typically measuring a few micrometers in diameter and growing several millimeters in length, they form through an electrochemical process influenced by environmental factors such as temperature variations, mechanical or compressive stress, and the aging of solder alloys.