-
- News
- Books
Featured Books
- pcb007 Magazine
Latest Issues
Current IssueInventing the Future with SEL
Two years after launching its state-of-the-art PCB facility, SEL shares lessons in vision, execution, and innovation, plus insights from industry icons and technology leaders shaping the future of PCB fabrication.
Sales: From Pitch to PO
From the first cold call to finally receiving that first purchase order, the July PCB007 Magazine breaks down some critical parts of the sales stack. To up your sales game, read on!
The Hole Truth: Via Integrity in an HDI World
From the drilled hole to registration across multiple sequential lamination cycles, to the quality of your copper plating, via reliability in an HDI world is becoming an ever-greater challenge. This month we look at “The Hole Truth,” from creating the “perfect” via to how you can assure via quality and reliability, the first time, every time.
- Articles
- Columns
- Links
- Media kit
||| MENU - pcb007 Magazine
Estimated reading time: 3 minutes
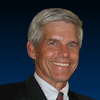
All About Flex: Origami Interconnection
Origami is the art of folding paper; it was believed to have originated in Japan, but historical evidence suggests it existed in several parts of the world during the same period. Origami artistry starts with a flat sheet of paper and by making a series of folds and creases, the result is a three-dimensional figure. Creating even just a simple figure takes imagination and a unique ability to visualize in three dimensions. Three-dimensional folding to fit into a multiplanar shape? Why does this sound familiar?
Most think of PCB design in terms of a series of flat layers. Thin flexible circuits offer another level of design. Since a flex circuit can be folded and creased, it can be designed to occupy three dimensions. On several occasions, I have had potential customers describe their flexible circuit application as an “origami interconnect” challenge. It wasn’t much of a stretch to imagine this concept as a metaphor for the challenges faced by a flex-circuit sales engineer. In the flex-circuit world, we are frequently asked to design origami circuits.
All Flex has designed and fabricated several three-dimensional origami models made from flexible circuit material constructions and displayed them at trade shows, or provided them as illustrations to clients. The purpose of creating these “origami flex” sales samples is to emphasize the potential that flexible circuits have to solve complex three-dimensional packaging problems. A couple of the “origami flex” models are shown here as Figures 1 and 2.
Figure 3: The flat state of the origami dog shown in Figure 2.
This thought process also provides insight into why a flex circuit might be utilized in a certain application. I am often asked about the cost of a flex circuit vs. a rigid board on a square-inch area comparison. My answer usually makes a reference suggesting “if you don’t take advantage of the flexibility, the rigid circuit will be less expensive.” But consider the task of trying to create a 3-dimensional dog using rigid PCBs. The design would involve multiple circuit boards, routed out in different shapes, and electrically interconnected with wires and connectors to arrive at an equivalently functional product. It might be accomplished, but would certainly not be considered an elegant solution. And in this extreme example, the cost to achieve a complex shape like the origami dog with rigid PCBs would be considerably costlier than using flex-circuit technology.
Of course, even the most intricate electronic package will seldom require something as complicated as an origami shape (disassembly of a single lens reflex camera might be an exception). However, origami flexible circuits do highlight some advantages of flex circuitry for electronic packaging. The value of flex increases dramatically when one thinks of it as a multi-planar interconnect system that can be flexed and folded to significantly increase the effective density of the interconnections. Reducing the interconnection requirements, whether in the form of soldered wires, connectors, or multiple rigid PCBs, demonstrates how the value might be harnessed in a variety of diverse applications.
Three-dimensional modelling software has provided a boost for flex-circuit adoption. These design tools help expose the multi-dimensional potential of flexible circuits. Avoiding bends near solder joints, or close to regions with nickel/gold surface treatments, are examples of hard knock lessons learned through experience. Flexible-circuit engineers have exposure to a wide variety of applications and can assist with guidelines for “origami circuits” when helping customers imagine designs squeezed into a housing requiring multi-planar interconnection shapes.
Fully exploiting the three-dimensional potential of flexible circuits will often translate into cost, weight and space reduction as well as reliability improvement. Contacting a circuit supplier with ideas early in the design phase is the best way to take advantage of the utility offered by this origami interconnect medium.
Dave Becker is vice president of sales and marketing at All Flex Flexible Circuits LLC.
More Columns from All About Flex
All About Flex: Terms and ConditionsAll About Flex: ISO 9001 Basics
All About Flex: FAQs on UL Listings for Flexible Circuits
All About Flex: Avoiding Trace Fracturing in a Flexible Circuit
Polyimide vs. Silicone for Flexible Heaters
All About Flex: Copper Thickness Requirements for Flex Circuits
All About Flex: Copper Grain Direction
All About Flex: Options for Purchasing Flexible Heaters