Ding Cheng of BYD Electronic: Embracing the FPC Factory Model of the Future
May 12, 2017 | Tulip Gu, I-Connect007Estimated reading time: 4 minutes
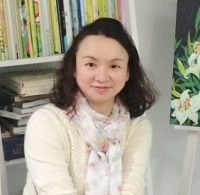
The topic of the third issue of PCB007 China Magazine is "The Wide World of Flex." Around this theme, we asked one of the leaders of China's FPC industry, Ding Cheng, general manager of the FPC Division of Shenzhen BYD Electronic Parts Company, to share his perspective about trends in flex, and where he thinks that market is headed in the future.
Tulip Gu: What trends have you seen in the flexible printed circuit market in recent years, such as product applications, technology updates, and process improvement?
Ding Cheng: I think the FPC market is mainly affected by the following drivers. While product requirement are getting smaller and smaller, the product itself should also be smaller. Traces and spaces should be finer, 9/12/9 double-sided non-adhesive material will be widely implemented. And 50/50 trace, 0.1 mm vias and 0.05 mm blind vias will become the market standard.
There are many technical requirements that 5G brings, such as high frequency, loss control, etc. The material process consistency, processing difficulty, and electrical performance testing requirements will be higher and higher.
Lastly, FPC is being driven by the requirements of faster assembling speed and direct assembly production. Today, FPC manufacturers are asked to provide similar services like EMS. FPC + SMT + assembly will become the best choice, but also the last choice. In addition to soldering electronic devices on the FPC, more and more orders request the integration of metal/plastic structural parts, die-cut plastic parts, dispensing, etc. We found that the end-customer is gradually transferring the hard-to-process part for EMS manufacturers to the upstream FPC fabricators.
Gu: What is the biggest advantage for Chinese FPC manufacturers? Looking at the global market, could this advantage provide global competitiveness for Chinese manufacturers?
Ding: Chinese FPC manufacturers basically can be divided into two kinds: one is the supply end, which provides product assemblies, similar to small EMS providers. The other focuses on specialized modules (LCM, CC, TP), providing FPC to these fabricators. But Chinese FPC manufacturers' technical capabilities and management capabilities are relatively weak; their product portfolio is mainly composed of double-sided circuits.
Today, the Chinese FPC industry's main end-customers are mobile phone and tablet companies. There are quite a lot of models out there, changing fast, with short cycle times. Chinese FPC companies are well adapted to these. But, there are two sides to every coin; these also lead to shorter design cycles, which will lead to poor manufacturability, in turn resulting in poor production consistency. At the same time, with lots of models, production of one model is limited, resulting in limited investment on tooling and equipment. Overall, Chinese FPC manufacturers lack technology accumulation. Also, their management is weaker than foreign manufacturers.
Compared to Apple or Samsung, they have less models, more units sold, longer design cycle, mass production quality is easier to control. Lots of Japanese and South Korean companies are opening facilities in mainland China or Southeast Asia with solid quality control and good yields, and their prices are not much higher than that of Chinese manufacturers. Meanwhile, workforce and environmental policy changes are leading to rising costs, so that Chinese manufacturers may have lost the cost advantage.
Today, in terms of the complexity of product, Chinese manufacturers are basically double-sided, while the Korean rigid-flex manufacturers took about 50% of the entire FPC production. In recent years, Korean companies have been developing rapidly, and their technical capabilities have even surpassed some major Japanese companies. Their factories are highly automated; AVI visual inspection is very common.
In my opinion, FPC + SMT + assembly is extremely complex. It's not something that other industries can imagine. FPC is characterized by its flexible design, but at the same time, designing and manufacturing is very much dependent on people. FPC requires Chinese manufacturers to try to eliminate the variations, solidify process, promote automation and IT management. The biggest factor in variations is the human factor, we must control, manage it well.
Gu: Artificial intelligence application in automotive electronics is a highlight in the market and Chinese and foreign manufacturers in this area continue to grow. With BYD as one of the leading FPC and new energy vehicle manufacturers in China, what is your response?
Ding: As for automotive electronics, we are mainly supplying ourselves, including sensor, remote control, multimedia, power batteries, lights, gearbox, etc. We are considering to provide them to other automotive companies in the future.
Gu: Can you share the current status of the new plant?
Ding: In addition to single-sided RTR production line established in 2006 in our Shen Hui facility, we have invested in a new double-sided RTR production line, which can perform RTR laser drilling, remove residue and black hole, RTR copper plating, RTR automatic alignment exposure, all the way to the finished circuit, 100% AOI inspection, double-sided 50/50 line spacing, 0.1 mm vias / 0.05 mm blind vias, plate plating and hole plating production capacity.
In the future, we will be able to do automatic drilling, automatic stamping, automatic stiffener application, automatic sticker application, automatic electrical test, automatic loading and unloading, automatic dispensing and other automated processes. Some will be able to be automatically visual inspected, QR code traceability; SMT production lines with AOI and SPI as standard equipment will be ramped up. At the same time, we will actively implement smart manufacturing for the full realization of production automation, IT management, and personnel specialization, as well as comprehensively promoting lean production and good management. Our vision is to become the most competitive FPC assembly provider.
Meanwhile, our new plant in Jiangxi will have the capacity of 50,000 square meters of precision double-sided + assembly by the end of 2017. The capacity of the FPC Division will reach 160,000 square meters per month by then, marching on the FPC + SMT + assembly to EMS path.
Gu: Thank you for your time.
Ding: Thank you.
Tulip Gu is executive editor of PCB007 China, with I-Connect007 China.
Testimonial
"Advertising in PCB007 Magazine has been a great way to showcase our bare board testers to the right audience. The I-Connect007 team makes the process smooth and professional. We’re proud to be featured in such a trusted publication."
Klaus Koziol - atgSuggested Items
How Good Design Enables Sustainable PCBs
08/21/2025 | Gerry Partida, Summit InterconnectSustainability has become a key focus for PCB companies seeking to reduce waste, conserve energy, and optimize resources. While many discussions on sustainability center around materials or energy-efficient processes, PCB design is an often overlooked factor that lies at the heart of manufacturing. Good design practices, especially those based on established IPC standards, play a central role in enabling sustainable PCB production. By ensuring designs are manufacturable and reliable, engineers can significantly reduce the environmental impact of their products.
50% Copper Tariffs, 100% Chip Uncertainty, and a Truce
08/19/2025 | Andy Shaughnessy, I-Connect007If you’re like me, tariffs were not on your radar screen until a few months ago, but now political rhetoric has turned to presidential action. Tariffs are front-page news with major developments coming directly from the Oval Office. These are not typical times. President Donald Trump campaigned on tariff reform, and he’s now busy revamping America’s tariff policy.
Global PCB Connections: Understanding the General Fabrication Process—A Designer’s Hidden Advantage
08/14/2025 | Markus Voeltz -- Column: Global PCB ConnectionsDesigners don’t need to become fabricators, but understanding the basics of PCB fabrication can save you time, money, and frustration. The more you understand what’s happening on the shop floor, the better you’ll be able to prevent downstream issues. As you move into more advanced designs like HDI, flex circuits, stacked vias, and embedded components, this foundational knowledge becomes even more critical. Remember: the fabricator is your partner.
MKS’ Atotech to Participate in IPCA Electronics Expo 2025
08/11/2025 | AtotechMKS Inc., a global provider of enabling technologies that transform our world, announced that its strategic brands ESI® (laser systems) and Atotech® (process chemicals, equipment, software, and services) will showcase their latest range of leading manufacturing solutions for printed circuit board (PCB) and package substrate manufacturing at the upcoming 17th IPCA Show to be held at Pragati Maidan, New Delhi from August 21-23, 2025.
MKS Showcases Next-generation PCB Manufacturing Solutions at the Thailand Electronics Circuit Asia 2025
08/06/2025 | MKS Instruments, Inc.MKS Inc, a global provider of enabling technologies that transform our world, today announced its participation in Thailand Electronics Circuit Asia 2025 (THECA 2025), taking place August 20–22 at BITEC in Bangkok.