-
- News
- Books
Featured Books
- smt007 Magazine
Latest Issues
Current IssueWhat's Your Sweet Spot?
Are you in a niche that’s growing or shrinking? Is it time to reassess and refocus? We spotlight companies thriving by redefining or reinforcing their niche. What are their insights?
Moving Forward With Confidence
In this issue, we focus on sales and quoting, workforce training, new IPC leadership in the U.S. and Canada, the effects of tariffs, CFX standards, and much more—all designed to provide perspective as you move through the cloud bank of today's shifting economic market.
Intelligent Test and Inspection
Are you ready to explore the cutting-edge advancements shaping the electronics manufacturing industry? The May 2025 issue of SMT007 Magazine is packed with insights, innovations, and expert perspectives that you won’t want to miss.
- Articles
- Columns
- Links
- Media kit
||| MENU - smt007 Magazine
Grow Your Own Training Programs
May 22, 2017 | Davina McDonnell, Saline LectronicsEstimated reading time: 10 minutes
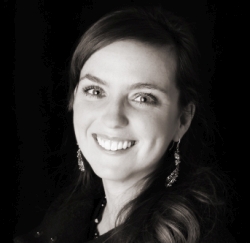
Introduction
With more than three million Baby Boomers retiring, or getting ready to do so, the manufacturing industry is bleeding out—losing talented, skilled, and experienced workers. Without a transfusion of new, even semi-skilled talent, many manufacturing companies are at a loss on how to best recruit the future work force.
Saline Lectronics, an electronics manufacturing services provider in southeastern Michigan, like many other manufacturers in the U.S., has struggled with finding the right skilled production workers to fill open positions. I checked in with several Saline Lectronics employees to find out their take on the state of the situation and included their impressions in this article.
The Current Situation
According to a study published by Deloitte, and the Manufacturing Institute on the manufacturing skills gap, “Six out of 10 manufacturing positions remain unfilled due to the talent shortage.” In other words, the current pool of workers lacks the necessary skills and industry experience to fill the open demand.
For years, the younger generations have been discouraged by manufacturing careers. Negative connotations about manufacturing jobs as dirty, repetitive, and boring have plagued the industry for the last 20 years. Manufacturing lacks the sex appeal that jobs in tech use to entice potential employees. Ironically, many of the tech companies create products that require some type of manufacturing, either domestically or abroad.
In the same manufacturing skills gap study, only 37% of respondents said that they would actively encourage their children to pursue a career in manufacturing. However, parents who actually work in the manufacturing industry are twice more likely to encourage their children to look into these careers. The people with firsthand experience and an accurate perception of American manufacturing today understand the exponential potential to a varied career in the industry.
Due to this great shortage of skilled workers and the lackluster image of the industry, manufacturing companies have had to re-evaluate and re-design their HR strategies to recruit, hire and train new employees.
In previous years, Lectronics leveraged a strong relationship with the local ITT Technical Institute to identify and recruit candidates with technical schooling and skills. Unfortunately, due to government funding shortages, since 2016 ITT Tech has closed over five campuses in Michigan.
Figure 1: Saline Lectronics’ technicians working on a lean assembly flow line.
“It’s been extremely difficult to find trained technicians for test or hand solder,” commented Amie Duffy, HR Specialist. “Since ITT Tech closed, it’s really impacted our funnel of skilled candidates.”
While working to establish new relationships with local community colleges, Lectronics’ HR strategy for 2017 blends a “grow your own” approach with heavy investment in new hire training and development. Additionally, the HR team actively reaches out to current employees to see if their communities, or alumni associations, might reveal hidden pools of untapped talent.
For manufacturing roles, community colleges tend to be a better resource than four-year universities for qualified applicants.
“Our industry is fast-paced and constantly advancing technology. If you’re out of it for two or three years than you’re missing a whole lot. People coming out of community college are far more connected to what we need,” commented Jeff Riedel, Lean Champion.
According to Lectronics’ HR Manager, Shelly Phelps, the company has a successful program that allows the organization to hire and train employees without previous manufacturing work or skills. If candidates have the basic education requirement of an Associate’s degree, then the organization will train them for specific openings.
For skilled production work, like hand soldering, Lectronics relies on a newly developed training program for candidates without any experience. During the interview process, applicants are required to provide a skills sample, to see how they perform with a soldering iron or other technical piece of equipment. It’s essentially a test to see if they’re a good fit for the full onboarding and training program.
“We’ve started looking for candidates with transferrable skills. Even if they don’t have direct experience in manufacturing, someone who likes to work with their hands could be a good fit for a mechanical assembly position,” commented Duffy.
During the interview process, Lectronics’ HR team isn’t solely focused on the applicant’s skills and experience. Personality and professional demeanor play a major role as the organization favors team-oriented and workable characteristics. HR typically recommends hiring people who are warm and friendly, and positively impact the company’s culture and work morale.
Surprisingly, Lectronics hasn’t had as much difficulty filling openings on the front side of manufacturing—such as customer service, purchasing, accounting or quoting roles. It’s the positions that require a more technical skill set that remain open and unfilled longer. In fact, most of technical production positions get filled by internal promotions rather than new hires.
“We grow our own. It’s our goal to identify what an employee wants in their personal career development; then, we give them an opportunity to pursue that avenue while providing the support and training to ensure that they stay,” commented Phelps.
Page 1 of 3
Suggested Items
Driving Innovation: Direct Imaging vs. Conventional Exposure
07/01/2025 | Simon Khesin -- Column: Driving InnovationMy first camera used Kodak film. I even experimented with developing photos in the bathroom, though I usually dropped the film off at a Kodak center and received the prints two weeks later, only to discover that some images were out of focus or poorly framed. Today, every smartphone contains a high-quality camera capable of producing stunning images instantly.
Hands-On Demos Now Available for Apollo Seiko’s EF and AF Selective Soldering Lines
06/30/2025 | Apollo SeikoApollo Seiko, a leading innovator in soldering technology, is excited to spotlight its expanded lineup of EF and AF Series Selective Soldering Systems, now available for live demonstrations in its newly dedicated demo room.
Indium Corporation Expert to Present on Automotive and Industrial Solder Bonding Solutions at Global Electronics Association Workshop
06/26/2025 | IndiumIndium Corporation Principal Engineer, Advanced Materials, Andy Mackie, Ph.D., MSc, will deliver a technical presentation on innovative solder bonding solutions for automotive and industrial applications at the Global Electronics A
Fresh PCB Concepts: Assembly Challenges with Micro Components and Standard Solder Mask Practices
06/26/2025 | Team NCAB -- Column: Fresh PCB ConceptsMicro components have redefined what is possible in PCB design. With package sizes like 01005 and 0201 becoming more common in high-density layouts, designers are now expected to pack more performance into smaller spaces than ever before. While these advancements support miniaturization and functionality, they introduce new assembly challenges, particularly with traditional solder mask and legend application processes.
Knocking Down the Bone Pile: Tin Whisker Mitigation in Aerospace Applications, Part 3
06/25/2025 | Nash Bell -- Column: Knocking Down the Bone PileTin whiskers are slender, hair-like metallic growths that can develop on the surface of tin-plated electronic components. Typically measuring a few micrometers in diameter and growing several millimeters in length, they form through an electrochemical process influenced by environmental factors such as temperature variations, mechanical or compressive stress, and the aging of solder alloys.