-
- News
- Books
Featured Books
- pcb007 Magazine
Latest Issues
Current IssueInventing the Future with SEL
Two years after launching its state-of-the-art PCB facility, SEL shares lessons in vision, execution, and innovation, plus insights from industry icons and technology leaders shaping the future of PCB fabrication.
Sales: From Pitch to PO
From the first cold call to finally receiving that first purchase order, the July PCB007 Magazine breaks down some critical parts of the sales stack. To up your sales game, read on!
The Hole Truth: Via Integrity in an HDI World
From the drilled hole to registration across multiple sequential lamination cycles, to the quality of your copper plating, via reliability in an HDI world is becoming an ever-greater challenge. This month we look at “The Hole Truth,” from creating the “perfect” via to how you can assure via quality and reliability, the first time, every time.
- Articles
- Columns
- Links
- Media kit
||| MENU - pcb007 Magazine
Estimated reading time: 4 minutes
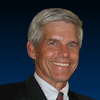
All About Flex: Back-Bared Flexible Circuits
Back-bared pad flexible circuits are a distinctive type of single-sided flexible circuit providing some advantages over more standard circuits. In the printed circuit industry, back-bared pad circuit designs are also referred to as dual-access or reversed bared. As their name suggests, these circuits have insulation openings on both their top and bottom sides allowing dual access to a single plane of copper. Substrate lamination is a unique and critical step when creating a back bared pad solution.
A background description of common flex circuit types helps to understand the design nuance between single-sided and back-bared circuitry. Below is a review of the typical constructions for flexible circuits.
Single-Sided
Most single-sided flexible circuits (Figure 1) start out with copper foil bonded to a single layer of polyimide dielectric film. The bonding between the copper and polyimide is usually accomplished with a layer of adhesive. Alternatively, the copper may be bonded directly to the dielectric. These composites are known as adhesiveless substrates.
Creation of the copper pattern is done by photolithographic imaging, developing, and etching. A finished circuit is created with a subsequent lamination of pre-punched polyimide bonded as a coverlay; or a photoimaged soldermask can be defined as a selective dielectric covering on the top layer.
Figure 1: Single-sided flex circuit.
Double-Sided
Double-sided circuits (Figure 2) start out with two copper plane layers separated electrically with a layer of insulating film. As with single-sided designs, the bonding between the substrate film and the copper conductors can be with adhesive or adhesiveless. Double-sided circuits will have through-holes drilled and plated to form conductive vias, while both sides are imaged and etched to create the trace patterns.
Figure 2: Double-sided flex circuit.
Multilayer
Multilayer circuits (Figure 3) repeat the pattern established in a double-sided circuit and are created by bonding pre-fabricated layers of single- or double-sided circuits. Excluding some variations introduced by blind and buried vias, the common practice in multilayer processing is to then drill through-holes followed by copper electroplating. This completes the electrical connection among the various conductive layers. The fabricated layers are laminated together using a bond ply material consisting of a dielectric coated on both sides with an adhesive.
Figure 3: Multilayer flex circuit.
Back-Bared
A back-bared circuit (Figure 4) often starts by laminating a custom pre-punched or drilled dielectric film to a single layer of copper. Imaging and etching the copper is done to create a copper pattern in registration to openings in the pre-punched dielectric film. These locations become the access points from the back side. Pre-punched dielectric or photoimaged soldermask is then applied to the top side. Additional plating and other surface finishing processes such as reflowed solder or electroless nickel immersion gold (ENIG) may be added for surface contacts and/or to provide a solderable surface.
Figure 4: Back-bared flex circuit.
An alternative and increasingly popular method of creating a back bared pad circuit is to laser ablate select regions to remove the dielectric. This process is closely controlled to ablate through the film plus adhesive while leaving the copper. This is a very precise process and can be done with tighter resolution as compared to pre-drilling the dielectric film before lamination. Using expensive capital equipment (for laser ablation) is usually a more expensive processing option.
The two primary advantages of back bared circuits are:
1. Create electrical access points on the back side of the circuit without the added expense of creating a double-sided circuit. Components can be inserted and soldered from both top and bottom sides. An exposed area can be a pad, or it can be a trace that spans an opening. A functionally similar design can be created with a double-sided circuit, but an extra layer of copper and polyimide film is required, as is an additional copper plating process.
2. Create exposed copper “fingers” that are soldered directly from one rigid circuit board to another as in a jumper cable. This serves as a highly reliable and low-profile method to replace connectors and is often referred to as a sculptured circuit. Typically, the exposed fingers will need to be thicker than other parts of the circuit. The exposed insertion fingers are differentially etched to create circuitry containing variable copper thickness with pin features that are bent to match an insertion connector profile.
Sculptured Circuits
This variant of a back-bared circuit has been adopted in a variety of applications taking advantage of their integrated solder pin utility. Among the reasons a sculptured circuit might be useful include:
- Reliability—the connector pins hold up extremely well in vibration testing or thermal cycling; minimizing connection junctions is a common method for reliability improvement
- Lower cost—the connector component is eliminated as is the labor to attach it
- Weight and space reduction—with the elimination of a connector, this component’s weight and profile are eliminated
- Configurability—photolithography imaging and copper etching processes allow significant choices in terms of number of pins, density of pins, and even thickness and length; they can be bent for 90- or 45-degree insertion
- Surface finishing—leads can be plated with tin, tin-lead, gold or other surface finishes to be compatible with mating components
Dave Becker is vice president of sales and marketing at All Flex Flexible Circuits LLC.
More Columns from All About Flex
All About Flex: Terms and ConditionsAll About Flex: ISO 9001 Basics
All About Flex: FAQs on UL Listings for Flexible Circuits
All About Flex: Avoiding Trace Fracturing in a Flexible Circuit
Polyimide vs. Silicone for Flexible Heaters
All About Flex: Copper Thickness Requirements for Flex Circuits
All About Flex: Copper Grain Direction
All About Flex: Options for Purchasing Flexible Heaters