-
- News
- Books
Featured Books
- smt007 Magazine
Latest Issues
Current IssueWhat's Your Sweet Spot?
Are you in a niche that’s growing or shrinking? Is it time to reassess and refocus? We spotlight companies thriving by redefining or reinforcing their niche. What are their insights?
Moving Forward With Confidence
In this issue, we focus on sales and quoting, workforce training, new IPC leadership in the U.S. and Canada, the effects of tariffs, CFX standards, and much more—all designed to provide perspective as you move through the cloud bank of today's shifting economic market.
Intelligent Test and Inspection
Are you ready to explore the cutting-edge advancements shaping the electronics manufacturing industry? The May 2025 issue of SMT007 Magazine is packed with insights, innovations, and expert perspectives that you won’t want to miss.
- Articles
- Columns
- Links
- Media kit
||| MENU - smt007 Magazine
The Need for 3D AOI
June 5, 2017 | Stephen Las Marias, I-Connect007Estimated reading time: 2 minutes
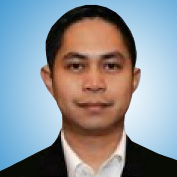
The continuing trend towards miniaturization of components, more advanced component packaging with finer lead pitches, and increasing component densities in smaller PCB sizes are driving the need for an even more accurate inspection systems to detect defects in PCB assemblies.
According to a new report by industry analyst MarketsandMarkets, the global AOI market is expected to reach $1 billion by 2022, registering a CAGR of 17.1% between 2016 and 2022. The report added that 2D AOI systems, which have been widely accepted and have been in use for many years, will continue to hold a larger share of the overall AOI systems market due to their advantages such as cost-effectiveness, high-speed inspection, and the ease of programming.
In fact, in our recent survey on inspection, the majority—or 60%—of the respondents from the EMS and PCB assembly industries say they are still using 2D AOI.
Technological advancements in terms of cameras, optics, and lighting have made 2D AOI suitable for detecting defects such as missing or wrong components, loose components, component misalignment, solder bridges, and solder balls, to name a few.
However, 2D AOI has its own set of disadvantages: it is incapable of true co-planarity inspection; it doesn’t provide volumetric measurement data; increased probability for escapes; and it has a high false call rate, according to an article by Brian D’Amico of Mirtec Corp.
Meanwhile, Kevin Garcia of Nordson YESTECH explains that, while the coplanarity of height-sensitive devices such as BGA packages and leaded components can be inspected in 2D using multi-angled colored lighting and side-angle cameras, these will be susceptible to an increase in false calls, a need for additional programming and cycle time, and possible escapes.
These factors underscore the need for 3D technology in inspection strategies. According to the report by MarketsandMarkets, various advantages of 3D AOI systems such as capability to inspect co-planarity of components, detecting lifted leads, and reduction in false call rates are contributing to the growth of the 3D AOI system market. In fact, 3D AOI systems are expected to grow at a high CAGR in the overall AOI system market between 2016 and 2022.
Going back to Figure 1, majority of those who answered “No” commented that they do have plans to adopt 3D AOI in their inspection lines; some within the next 12 to 18 months.
Before, inspection was viewed as something that doesn’t add value—human visual inspection was often enough. However, as reliability became critical in markets such aerospace and automotive electronics, the potential cost of failure overcomes the cost of installing automated inspection systems that would ensure quality and reliability of the systems being manufactured. Thus, every manufacturer now utilizes 2D or 3D AOI inline or offline in their manufacturing plants. According to our survey, majority or more than 60% of the respondents with inspection equipment installed have seen improvements in their manufacturing process—through early detection of potential defects and improving failure rates. This has also led to increased yields—according to more than half (52%) of the respondents, having an inspection strategy has resulted in at most a 10% improvement in yields. Nearly a quarter (24%) of the respondents, on the other hand, have achieved between 26% and 50% improvement in yields.
To read the full version of this article, which appeared in the June 2017 issue of SMT Magazine, click here.
Testimonial
"The I-Connect007 team is outstanding—kind, responsive, and a true marketing partner. Their design team created fresh, eye-catching ads, and their editorial support polished our content to let our brand shine. Thank you all! "
Sweeney Ng - CEE PCBSuggested Items
Weller Tools Supports Future Talent with Exclusive Donation to SMTA Michigan Student Soldering Competition
07/23/2025 | Weller ToolsWeller Tools, the industry leader in hand soldering solutions, is proud to announce its support of the upcoming SMTA Michigan Expo & Tech Forum by donating a limited-edition 80th Anniversary Black Soldering Set to the event’s student soldering competition.
Koh Young Appoints Tom Hattori as President of Koh Young Japan
07/21/2025 | Koh YoungKoh Young Technology, the global leader in True 3D measurement-based inspection solutions, announced the appointment of Tom Hattori as President of Koh Young Japan (JKY).
Silicon Mountain Contract Services Enhances SMT Capabilities with New HELLER Reflow Oven
07/17/2025 | Silicon Mountain Contract ServicesSilicon Mountain Contract Services, a leading provider of custom electronics manufacturing solutions, is proud to announce a significant upgrade to its SMT production capability with the addition of a HELLER 2043 MK5 10‑zone reflow oven to its Nampa facility.
Knocking Down the Bone Pile: Addressing End-of-life Component Solderability Issues, Part 4
07/16/2025 | Nash Bell -- Column: Knocking Down the Bone PileIn 1983, the Department of Defense identified that over 40% of military electronic system failures in the field were electrical, with approximately 50% attributed to poor solder connections. Investigations revealed that plated finishes, typically nickel or tin, were porous and non-intermetallic.
SHENMAO Strengthens Semiconductor Capabilities with Acquisition of PMTC
07/10/2025 | SHENMAOSHENMAO America, Inc. has announced the acquisition of Profound Material Technology Co., Ltd. (PMTC), a premier Taiwan-based manufacturer of high-performance solder balls for semiconductor packaging.