-
- News
- Books
Featured Books
- smt007 Magazine
Latest Issues
Current IssueWhat's Your Sweet Spot?
Are you in a niche that’s growing or shrinking? Is it time to reassess and refocus? We spotlight companies thriving by redefining or reinforcing their niche. What are their insights?
Moving Forward With Confidence
In this issue, we focus on sales and quoting, workforce training, new IPC leadership in the U.S. and Canada, the effects of tariffs, CFX standards, and much more—all designed to provide perspective as you move through the cloud bank of today's shifting economic market.
Intelligent Test and Inspection
Are you ready to explore the cutting-edge advancements shaping the electronics manufacturing industry? The May 2025 issue of SMT007 Magazine is packed with insights, innovations, and expert perspectives that you won’t want to miss.
- Articles
- Columns
- Links
- Media kit
||| MENU - smt007 Magazine
3D: Towards Better Inspection Capability
June 8, 2017 | Stephen Las Marias, I-Connect007Estimated reading time: 4 minutes
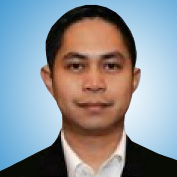
There is a critical need for inspection in the PCB assembly industry as the trend towards miniaturization of electronics systems and devices continue—on top of increasing requirements for reliability and quality.
For this month's issue of SMT Magazine, we spoke with Mark McMeen, vice president of engineering at STI Electronics, to know more about the inspection challenges and requirements from an EMS provider's standpoint. We also talked with Jean-Marc Peallat, vice president of global sales at Vi TECHNOLOGY, to find out, from a supplier's perspective, how they are looking at these challenges and addressing them through their product development efforts.
According to McMeen, the real challenge is being able to verify the solder fillets on very fine pitch QFNs and LGA parts. He said that's both done by utilizing the co-planarity of the part as well as being able to get a 3D viewing of the solder fillet on the side of the QFN and LGA.
"One of the challenges in inspection is the miniaturization of the devices and components," said Peallat. "Joints are getting smaller, fine pitch are getting denser; this trend became a challenge for all our inspection types. Embedding 3D technologies in inspection systems, and lately for the components inspection, is a solution to improve the quality and reliability of the tests."
Peallat explained that most of the 3D systems are using a top-down camera with projectors from the side. "I would say that that covers probably 95–98% of the vendors. In that case, systems are dependent on the top-down view from the camera. Some are using angled cameras, and one of the challenges is the calibration of the optics. Combining top-down cameras and angled cameras is a real challenge with no simple solution when PCB warpage is important."
According to Peallat, all these are common problems for all automated inspection vendors. "The other way to approach these process challenges is to use a global approach of inspection in your line. If you look at the QFN joint quality, it’s a combination of what you have done at the print process and what you have done at component placement, not only individual independent processes. The biggest challenge we face today is the use of all the data from the inspection: we have 3D images, we have data, we have measurements. The challenge is to use that huge amount of information to improve the process," he said. "The past year, we invested to develop a solution that combines data from the SPI and the AOI. In fact, this combination gives more valuable and actionable information to the user than just a picture at the AOI review station."
That solution is called feed forward—a direct communication between SPI and AOI. Today, there are already systems that enable direct communication between the printer, to the pick and place machine, and others. What Vi TECHNOLOGY did, according to Peallat, was to focus on making SPI and AOI work together hand in hand to improve SMT line quality. In fact, the combination of these data, at the end of the line, offers more information about SPI parameters that really impact the quality.
Peallat noted that one of the benefits of this system is that users don't have to wait for the post reflow inspection to improve their process. Adjustments can be made at the printer level or at the SPI level to improve the process. Then you gain quality and also reduce your costs of rework. “I cannot disclose too much of this as we are currently working on an article, but we have done this with an EMS company on their automotive application," he said.
McMeen added that one of the challenges that they are also facing is the ability of getting the wetting angle. But he noted that the 3D AOI systems now are allowing them to ensure that on their passives, they are getting a 75% solder fillet going up the side of the part, 75% of the height, and then a nice wetting angle off of it. "If you're looking for a high degree of reliability and repeatability in your process, you're looking for getting the wetting on these caps and resistor faces up to 75% of its effacement and getting a nice fillet off of that."
At this point, McMeen asked Peallat about how 3D AOI allows them to get that measurement and why it’s an improvement over 2D AOI.
“The 2D was not able to measure the profile of the fillet because even with a set of lightings, your 2-D image is a flat image,” explained Peallat. “The only solution to measure 75% of the side of the component is to use 3D measurement. The challenge of 3D is what we call specularity, which is mainly when you have a very shinny joint, and the difficulty is to avoid the specular effect—meaning that you sometimes have a bright spot due to the angle of the light coming from the projector and going up directly to the cameras. Of course, 3D is a better way to measure this angle and the height of the joint. The challenge is, again, back to the size and the miniaturization of the component. Today, most of the systems have the ability to give you a profile of your joint, but the difficulty that I think most of the vendors have is to be clearly compliant to the IPC standards.”
To read the full version of this article, which appeared in the June 2017 issue of SMT Magazine, click here.
Suggested Items
Driving Innovation: Direct Imaging vs. Conventional Exposure
07/01/2025 | Simon Khesin -- Column: Driving InnovationMy first camera used Kodak film. I even experimented with developing photos in the bathroom, though I usually dropped the film off at a Kodak center and received the prints two weeks later, only to discover that some images were out of focus or poorly framed. Today, every smartphone contains a high-quality camera capable of producing stunning images instantly.
Hands-On Demos Now Available for Apollo Seiko’s EF and AF Selective Soldering Lines
06/30/2025 | Apollo SeikoApollo Seiko, a leading innovator in soldering technology, is excited to spotlight its expanded lineup of EF and AF Series Selective Soldering Systems, now available for live demonstrations in its newly dedicated demo room.
Indium Corporation Expert to Present on Automotive and Industrial Solder Bonding Solutions at Global Electronics Association Workshop
06/26/2025 | IndiumIndium Corporation Principal Engineer, Advanced Materials, Andy Mackie, Ph.D., MSc, will deliver a technical presentation on innovative solder bonding solutions for automotive and industrial applications at the Global Electronics A
Fresh PCB Concepts: Assembly Challenges with Micro Components and Standard Solder Mask Practices
06/26/2025 | Team NCAB -- Column: Fresh PCB ConceptsMicro components have redefined what is possible in PCB design. With package sizes like 01005 and 0201 becoming more common in high-density layouts, designers are now expected to pack more performance into smaller spaces than ever before. While these advancements support miniaturization and functionality, they introduce new assembly challenges, particularly with traditional solder mask and legend application processes.
Knocking Down the Bone Pile: Tin Whisker Mitigation in Aerospace Applications, Part 3
06/25/2025 | Nash Bell -- Column: Knocking Down the Bone PileTin whiskers are slender, hair-like metallic growths that can develop on the surface of tin-plated electronic components. Typically measuring a few micrometers in diameter and growing several millimeters in length, they form through an electrochemical process influenced by environmental factors such as temperature variations, mechanical or compressive stress, and the aging of solder alloys.