A Twist on Printed Electronics: Printing on 3D Shapes
June 23, 2017 | Barry Matties, I-Connect007Estimated reading time: 14 minutes
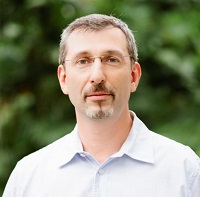
Barry Matties speaks with Optomec’s Pascal Pierra about their LENS printer systems and Aerosol Jet technology, which allows manufacturers to print applications like sensors and antennas on 3D objects. The process is significantly faster and greener than competing technologies.
Barry Matties: Pascal, why don't you start by telling our readers a little bit about your company.
Pascal Pierra: Optomec is a U.S. company, headquartered in New Mexico. We have been focused on 3D printing/additive manufacturing for about 20 years with two product lines. One is the LENS product line, which is a directed energy deposition technology where we can print metal, like titanium and stainless steel. The main application for the LENS product line is adding materials to existing components—for example to restore, remanufacture, or add features to metal parts. Optomec offers additive and hybrid systems where we can combine LENS technology with a CNC machine to enable additive/subtractive metal processing all on one machine. We have collaboration already with CNC machine tool suppliers in the U.S., Mexico with VIWA, Taiwan with Tongtai, and we're working on other collaborations in Asia. We also have our own hybrid systems called the LENS Machine Tool series.
The other product line is the Aerosol Jet, a unique technology for printing electronics onto 3D structures. It allows users to aerosol spray a wide variety of electronic and even bio-materials onto substrates at feature resolutions ranging from 10 microns to a few millimeters. What is unique to Aerosol Jet technology is its ability to print high-resolution conformal features onto any 3D shape.
Matties: So, Aerosol Jet is about 3D printing electronics; the technology is interesting because you're using gas to focus this and you atomize the particulate.
Pierra: Yes. Aerosol Jet printing is using an Optomec patented technology to create a spray. We have two different types of atomizers available, pneumatic or ultrasonic, that nebulizes a source material, for example a silver nano-particle ink, into a dense mist of very fine droplets ranging in diameter from 2–5 microns. Each droplet can contain thousands of silver nano-particles. This dense cloud of droplets with entrained nanoparticle particles is then directed to the Aerosol Jet deposition nozzle where it is surrounded by a sheath gas. The big advantage of our technology is that sheath gas is used to dynamically focus the cloud into a tight stream to create features ranging from 10 microns to a few millimeters. Also, thanks to the sheath gas, the mist is accelerated to a velocity of 50 meters/second , so it remains in focus during its travel from the nozzle exit to the substrate for a distance up to 5 mm. This long focal length enables it to maintain the desired feature resolution when printing on non-planar surfaces. No other technology on the market has that capability.
With other printing technologies, such as inkjet, the nozzle must be very close to the substrate and therefore they are not able to print on non-planar surfaces.
Matties: The market for 3D surfaces is quite broad because there are all types of applications.
Pierra: That's correct. So, one of the main markets that we're addressing is manufacturing of antennas for smartphones as well as the IoT market with printing various types of sensors. We can print antennas and sensors together as well as interconnects including multi-level interconnects, because we also can print dielectric materials at the cross-over points, eliminating the need for multilayer circuit boards. This all means we can print more electronics into a smaller space which is ideal for hand-held mobile devices, aerospace, and smart devices used for IoT applications. We also have customers using Aerosol Jet printing for applications in life science. For instance, there is a university in Singapore printing heaters on bandages. So, you can apply the bandage containing printed electronics onto the wound and then you apply heat to the wound. That is an example of the ability to print any circuitry onto a 3D substrate, even one that is flexible.
Matties: For a circuit board designer, would this be a tool to use for rapid prototyping for just a standard circuit?
Pierra: Rapid prototyping would be a very good application for this technology because you can print components such as resistors, capacitors, sensors, antennas, and even thin film transistors as well as interconnects to complete the circuitry. Since the printing process is driven by digital CAD data, users can create and revise prototypes very quickly. For instance, we have many military customers in the U.S. using our technology for prototyping and low volume production.
Matties: On the 3D printing side, has this technology been around for several years?
Pierra: Yes, this technology has been around for more than 15 years. There's a little subtlety between 3D printing and Aerosol Jet. With the Aerosol Jet we actually print on 3D shapes.
Matties: Versus printing an actual part.
Pierra: Right. With microfluidic needles, we can print the entire structures, but the main application is to print conformal electronics onto a 3D shape. In some cases where you need to achieve a certain resistivity, you can make the printed trace a little bit thicker by printing multiple layers but it’s not really 3D printing as you read about in the press, such as printing any shapes or any objects of various materials. What we do with Aerosol Jet is more what we call printing “on” 3D parts and those parts are typically made using conventional manufacturing methods such as injection molding.
Matties: It's an additive process onto a base that already exists. So you're not shaping a new knee. You're printing a circuit on a knee.
Pierra: That's exactly right. Then the other thing that we do, for instance we can print a coating on a stent; the addition of the material allows the body to better accept the stent and therefore reducing the medication required.
Another application that is very successful was developed in collaboration with General Electric. GE is now printing strain sensors onto metal blades used in their industrial gas turbine engines. The sensors are printed using a ceramic ink that can withstand the high operating temperature inside the engine. Each sensor has a unique digital code and a precisely printed pattern that can be used to measure expansion in the blade—a condition known as creep. During maintenance cycles the sensors are scanned and the data is sent to Predix, the GE Industrial Internet of Things analytics platform. Then just the blades that require replacement are identified and replaced reducing maintenance costs and downtime. The advantage of this is now they know which blades on the turbine need to be replaced and which don't. In reality very few blades need to be replaced during the early in-service life of the engine. Reliability engineers call the early life failure mode “infant mortality.” Prior to incorporating creep sensors, GE replaced all of the blades based on the predicted infant mortality failure time.
Matties: Regardless of condition.
Pierra: Yes. Now they can identify and replace just those blades that are about to experience failure. So, there's a huge market here that people are not yet aware of, which is to help extend the life of the critical parts by adding sensors on the parts. We are also printing strain sensors on shafts. And the same, you can measure the sensors and see if that shaft needs to be replaced or not. This opens the door to a very wide range of applications for many industries. Printing the sensors adds a few dollars to the cost of each blade, but saves thousands of dollars in unneeded blade replacement and downtime.
Matties: Now, if a customer already has materials and inventory in their warehouse, and they say, "We want to add a sensor to this," they don't need to go out to a manufacturer. They could just literally do it inside their own factory.
Pierra: That's exactly right.
Matties: This changes the way circuits could be built in the future.
Pierra: That's correct. You can add the sensor afterwards. You can add the sensors on the shaft. The shaft is a good example of a 3D shape. So, it doesn't matter. You can print anything on anything.
Matties: What about automobile applications?
Pierra: For automobiles we have a few applications, especially with printing heaters. For instance, new cars have assistance for drivers, right? Some luxury cars, if you start coming out of your lane, the car takes you back into the lane. All this technology is assisted by cameras. You don't want the camera to be obstructed by ice in the winter. So, we have applications where we can print heaters on the window that the camera is seeing through. Then, you can also print an ice sensor. You can sense that the heater needs to be turned on and turn it on automatically. This application is trickier than it looks because you send the same currents through the window, but you see the trace length is different. So, if you want the same current to go through each of the traces, you need to adjust. You don't see it, but some traces here are thicker than others so that all have the same resistance creating uniform heating/melting. So, it's not as trivial as it looks.
Matties: We were talking earlier about airplane wings or icy conditions. Can you explain more about that?
Pierra: We also have development with some airplane companies about printing the same type of heaters on flexible electronics so you can adjust it from the wings and then with the same ice sensor, you can detect the ice and then switch on the heater automatically to make sure the airplane has no icing problem before take-off.
Matties: Are you actually printing on a wing surface or are you printing a membrane that they apply?
Pierra: We can do both.
Matties: What's the size? Because the wing is awfully large. How does a wing get through your process?
Pierra: In this particular application that I was discussing, we were doing prototypes on drawings. Then it didn't get to the actual application, but in practice we could print on flexible circuitry and just apply it on the wing. It would not be a problem.
Matties: But the machine itself, it's not a machine that you could go mount somewhere and cover the whole wing, literally?
Pierra: Well, we could. The Aerosol Jet technology has been packaged as a stand-alone entity; we call it the Aerosol Jet Print Engine (AJPE). The AJPE can be mounted on a robot arm to access the wing in this example or on any other automation platforms to address whatever high volume manufacturing application you may have.
Matties: I'm wondering if there's a business of portability with this where someone can have it in a truck and go provide service to companies, or the military can have it in jeeps out in the battlefields or other locations. Is there thinking along those lines or any interest in that? Is there any practical purpose for that? Repair radios or something in a combat situation?
Pierra: Not at the moment but we did have a project with the U.S. Army to print various types of sensors and power circuits directly on 3D printed drones depending on the mission. This was a collaboration with a U.S. company called Aurora Flight Sciences.
Matties: You guys sound like you're very innovative. I'm just thinking about a wing, if I have an existing airplane and I want to convert all my planes to this heater technology in this area. So it works that way. This is really interesting technology and it's already changed the way people are thinking and doing business. Since it's not really 3D printing, how would you describe this?
Page 1 of 2
Testimonial
"Our marketing partnership with I-Connect007 is already delivering. Just a day after our press release went live, we received a direct inquiry about our updated products!"
Rachael Temple - AlltematedSuggested Items
How Good Design Enables Sustainable PCBs
08/21/2025 | Gerry Partida, Summit InterconnectSustainability has become a key focus for PCB companies seeking to reduce waste, conserve energy, and optimize resources. While many discussions on sustainability center around materials or energy-efficient processes, PCB design is an often overlooked factor that lies at the heart of manufacturing. Good design practices, especially those based on established IPC standards, play a central role in enabling sustainable PCB production. By ensuring designs are manufacturable and reliable, engineers can significantly reduce the environmental impact of their products.
50% Copper Tariffs, 100% Chip Uncertainty, and a Truce
08/19/2025 | Andy Shaughnessy, I-Connect007If you’re like me, tariffs were not on your radar screen until a few months ago, but now political rhetoric has turned to presidential action. Tariffs are front-page news with major developments coming directly from the Oval Office. These are not typical times. President Donald Trump campaigned on tariff reform, and he’s now busy revamping America’s tariff policy.
Global PCB Connections: Understanding the General Fabrication Process—A Designer’s Hidden Advantage
08/14/2025 | Markus Voeltz -- Column: Global PCB ConnectionsDesigners don’t need to become fabricators, but understanding the basics of PCB fabrication can save you time, money, and frustration. The more you understand what’s happening on the shop floor, the better you’ll be able to prevent downstream issues. As you move into more advanced designs like HDI, flex circuits, stacked vias, and embedded components, this foundational knowledge becomes even more critical. Remember: the fabricator is your partner.
MKS’ Atotech to Participate in IPCA Electronics Expo 2025
08/11/2025 | AtotechMKS Inc., a global provider of enabling technologies that transform our world, announced that its strategic brands ESI® (laser systems) and Atotech® (process chemicals, equipment, software, and services) will showcase their latest range of leading manufacturing solutions for printed circuit board (PCB) and package substrate manufacturing at the upcoming 17th IPCA Show to be held at Pragati Maidan, New Delhi from August 21-23, 2025.
MKS Showcases Next-generation PCB Manufacturing Solutions at the Thailand Electronics Circuit Asia 2025
08/06/2025 | MKS Instruments, Inc.MKS Inc, a global provider of enabling technologies that transform our world, today announced its participation in Thailand Electronics Circuit Asia 2025 (THECA 2025), taking place August 20–22 at BITEC in Bangkok.