-
- News
- Books
Featured Books
- smt007 Magazine
Latest Issues
Current IssueWhat's Your Sweet Spot?
Are you in a niche that’s growing or shrinking? Is it time to reassess and refocus? We spotlight companies thriving by redefining or reinforcing their niche. What are their insights?
Moving Forward With Confidence
In this issue, we focus on sales and quoting, workforce training, new IPC leadership in the U.S. and Canada, the effects of tariffs, CFX standards, and much more—all designed to provide perspective as you move through the cloud bank of today's shifting economic market.
Intelligent Test and Inspection
Are you ready to explore the cutting-edge advancements shaping the electronics manufacturing industry? The May 2025 issue of SMT007 Magazine is packed with insights, innovations, and expert perspectives that you won’t want to miss.
- Articles
- Columns
- Links
- Media kit
||| MENU - smt007 Magazine
3D Inspection is the Way to Go
June 13, 2017 | Stephen Las Marias, I-Connect007Estimated reading time: 7 minutes
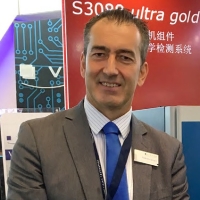
In an interview with SMT Magazine during NEPCON China, Guido Bornemann, head of sales in Asia for Viscom, discusses how inspection technology is keeping up with the latest requirements and demands from customers. He also explains why 3D technology is the best inspection technology to utilize in electronics assembly.
Stephen Las Marias: Guido, what are the greatest challenges that your customers are facing right now?
Bornemann: Right now, there is a lot of energy going into avoiding false calls. If you look back five years ago, mainly the automotive industry needed to find all the defects and false calls, and things like false alarms were not so important. We still find all the defects there, but now they don’t want to the risk for false calls. That means we have to find all the defects at zero false calls, because every false call is a potential escapee. The machine is correct, but the operator may be classifying it as a false effect. So, the challenge is to find all the defects at the highest yield rate.
Las Marias: How are you helping your customers do that?
Bornemann: 3D, of course, is the way to go. The more information you get, the easier it will be, and there are a lot of features we are just introducing, such as the 360-degree view. That means we’re taking 2D, 2.5D pictures from all angles, and we are displaying them on the classification station of the machine. It means the operators don’t really need to be present at the machine, but can see the whole view on the monitor and then classify properly and correctly.
Las Marias: Before, people aren’t giving too much of a though on inspection. What drove them to increasingly integrate inspection systems into their SMT assembly lines?
Bornemann: If you look back a couple of years ago, people didn’t consider inspection because there’s no value add in it, or it’s really late ROI. Inspection, in general, was basically just, “Let's put it to ensure that I only deliver perfect products for my customer.” But recently, the implementation of closed loop uplink functions was really helpful, because you have all the information available at the end of the process. And now, we developed a lot of software features to help the customers use this information to optimize their process. It means producing less defects and really evaluate what is going wrong in your process, and then to utilize this information to optimize your process—and therefore, cut down defects and cut down the cost.
Las Marias: That involves a lot of data.
Bornemann: Yes. While the collection of data is important, utilization of that data is also very important. So, we developed proper software tools that evaluate if the defects are coming from the pick-and-place machine or from the oven, for instance, and we work together with suppliers to feed that information back and prepare the data, store them properly, or feed them back properly to other machines in the SMT process.
Las Marias: How do you help customers with their inspection strategy?
Bornemann: All in all, you need to have a proper 3D approach. There are a lot of 3D machines available in the market. 3D has limitations, especially when you have very tall capacitors and you have small chips in the shadows. So you need to have a technology that can cover this. The combination we are doing is for 3D, but we still have the options of 2D or 2.5D, making it possible to inspect the whole boards. If you only do it by 3D, you'll have still limitations. So, you have to have a proper 3D performance, plus the opportunities to still inspect the boards or the components where they are limited. So, this is basically what we are doing.
I mean, one of the biggest limitations, usually, was speed. So, you could go into 3D but you were really facing a speed issue. What we have done is we have increased our field of view of our angular cameras. And with this, we are promoting our so called XM Plus module, which is really tackling these limitations. So now we have a system which can do a full 3D measurement at in-line speed. This I would say is one of the key factors to really make a full 3D in-line measurement, in-line capable.
3D is the way to go, because especially components are getting smaller, boards are getting more populated. There are the limitations of the 2D, which is basically like lifted leads of small QFPs, fine pitch QFPs, and it is tombstoning very small chips. You really reach the limitation over to the system. 3D helps you on, like I mentioned before, with first pass yield. This is getting more and more important, so 3D is helping you to increase your yield. Because simply you have much more information available and this is the way to go.
Las Marias: What are some of the key factors to consider when selecting a 3D AOI system?
Bornemann: Basically, you should make sure that this is in-line capable, and that this is real measurement. You know, the difference between inspection and measurement is that inspection only tells you whether it’s good or bad; but the measurement is the one that is really helping you. There's a lot of systems in the market who claim to do measurement, but if you look closer, it's just inspection. If you go for an SPI measurement, it's rather easy because you have just height differences of a very few micro meters. If you go for post reflow, measurement becomes more challenging, because we have from small components up to very tall components. You have to cover a whole range.
Speed, of course, is the second factor. You have to make sure that your measurement speed is in-line capable and covering your whole board, and not only certain components.
Las Marias: You mentioned earlier that it makes sense to have a setup wherein you got 2D or 2.5D, and 3D, in an inspection line.
Bornemann: Yes. Basically, we would start from the 3D, but there are a few limitations. We have a lot of limitations on the 2D, you still have a few limitations on the 3D. So, we still believe that implementing a couple of 2D factors into our 3D system is helping you on speed, on inspection, and quality. OCR is an example. For OCR, you don't necessarily need 3D, but 2D inspection of OCR can help you a lot in increasing the speed. So, a combination of 3D, 2D, and 2.5D is really the best solution for speed, inspection depth and inspection quality.
Las Marias: How do you convince customers who are still very much focused on the cost issue?
Bornemann: Cost, of course, is a very important issue. Here, we're coming back to the speed again. Because the more throughput we can offer, the easier you can utilize the machine and the sooner you get your ROI. Looking into Asia, we are also offering price-performance machines, which include the full range of our high-end machines at certain limitations. Cost, of course, is a very important factor in Asia, and we're able to handle this with our so-called Asia machines as well.
Las Marias: I think the cost of failure when systems break down is higher than installing systems earlier on in the process, right?
Bornemann: Correct. That's why, you know, we are made in Germany, so sturdiness, repeatability is really an important factor. Especially when you go into high-end manufacturing, of course, where you want to make sure that if you test the board today and your customer brings back the board in two years, the results are still the same. So that’s why we spend a lot of effort into repeatability, sturdiness, and I would say that is one of the really big advantages our machines have.
Page 1 of 2
Suggested Items
Intervala Hosts Employee Car and Motorcycle Show, Benefit Nonprofits
08/27/2024 | IntervalaIntervala hosted an employee car and motorcycle show, aptly named the Vala-Cruise and it was a roaring success! Employees had the chance to show off their prized wheels, and it was incredible to see the variety and passion on display.
KIC Honored with IPC Recognition for 25 Years of Membership and Contributions to Electronics Manufacturing Industry
06/24/2024 | KICKIC, a renowned pioneer in thermal process and temperature measurement solutions for electronics manufacturing, is proud to announce that it has been recognized by IPC for 25 years of membership and significant contributions to electronics manufacturing.
Boeing Starliner Spacecraft Completes Successful Crewed Docking with International Space Station
06/07/2024 | BoeingNASA astronauts Barry "Butch" Wilmore and Sunita "Suni" Williams successfully docked Boeing's Starliner spacecraft to the International Space Station (ISS), about 26 hours after launching from Cape Canaveral Space Force Station.
KIC’s Miles Moreau to Present Profiling Basics and Best Practices at SMTA Wisconsin Chapter PCBA Profile Workshop
01/25/2024 | KICKIC, a renowned pioneer in thermal process and temperature measurement solutions for electronics manufacturing, announces that Miles Moreau, General Manager, will be a featured speaker at the SMTA Wisconsin Chapter In-Person PCBA Profile Workshop.
The Drive Toward UHDI and Substrates
09/20/2023 | I-Connect007 Editorial TeamPanasonic’s Darren Hitchcock spoke with the I-Connect007 Editorial Team on the complexities of moving toward ultra HDI manufacturing. As we learn in this conversation, the number of shifting constraints relative to traditional PCB fabrication is quite large and can sometimes conflict with each other.