-
- News
- Books
Featured Books
- smt007 Magazine
Latest Issues
Current IssueSupply Chain Strategies
A successful brand is built on strong customer relationships—anchored by a well-orchestrated supply chain at its core. This month, we look at how managing your supply chain directly influences customer perception.
What's Your Sweet Spot?
Are you in a niche that’s growing or shrinking? Is it time to reassess and refocus? We spotlight companies thriving by redefining or reinforcing their niche. What are their insights?
Moving Forward With Confidence
In this issue, we focus on sales and quoting, workforce training, new IPC leadership in the U.S. and Canada, the effects of tariffs, CFX standards, and much more—all designed to provide perspective as you move through the cloud bank of today's shifting economic market.
- Articles
- Columns
- Links
- Media kit
||| MENU - smt007 Magazine
Solder Ball Joint Reliability with Electroless Ni/Pd/Au Plating – Influence of Electroless Pd Plating Film Thickness
June 20, 2017 | Yoshinori Ejiri, et al., Hitachi Chemical Co. LtdEstimated reading time: 4 minutes
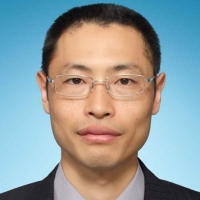
Abstract
The influence of Pd film thickness in electroless Ni/Pd/Au plating on the solder ball joint reliability after reflow cycles and thermal aging was investigated by conducting a high-speed solder ball shear test. Sn-3.0Ag-0.5Cu (SAC305) was used as the solder ball in this study. On the basis of the solder joint reliability obtained after multiple reflow cycles and thermal aging, the optimum thickness of the Pd film was found to be 0.05–0.2 µm.
The covering property of electroless Pd plating film on the electroless Ni plating film was also investigated. We found that an electroless Pd plating film with a thickness of 0.02 µm or more covered the electroless Ni plating film adequately, and the solder ball joint reliability in this case was better than that with electroless Ni/Au plating. We consider that the shape of the intermetallic compounds (IMCs) is one of the factors that influence the solder joint reliability after multiple reflow cycles. Consequently, we inferred that the high adhesion at the dendrite layers of IMCs/solder interface resulted in excellent solder ball joint reliability after the reflow cycles. We consider that the thickness of the IMCs is one of the factors that influence the solder joint reliability after thermal aging. In (Cu, Ni, Pd)6Sn5 IMCs that contained trace amounts of Pd, the growth of the IMCs is prevented by Pd, resulting in excellent solder ball joint reliability after thermal aging.
Introduction
With the widespread use of portable electronic equipment, chip scale packages (CSPs) and ball grid arrays (BGAs) mounted on high-density printed circuit boards (PCBs) have become popular as semiconductor package assemblies. The CSPs and BGAs are connected to the PCBs using solder balls. Such connection methods require smaller connection areas and no metal leads, thus resulting in a lower ability to resist the stress relaxation than in the case of the traditional methods of connecting the leads of thin small outline packages (TSOP) and quad flat packages (QFPs). The connection methods employing solder balls, therefore, involve many problems related to joint reliability. Several studies on the reliability of solder ball joint connections with CSPs and BGAs are now in progress.
The conventional electrolytic Ni/Au plating is a mature technology that has long been used for surface finishing of package substrates. However, this technique cannot be applied to high-density package substrates, because it requires bus lines to each terminal and the necessary area for those lines. Therefore, electroless Ni/Au plating was adopted because it does not require bus lines. However, drop tests revealed that the reliability of ball joints prepared by this technique is insufficient. To solve this problem, electroless Ni/Pd/Au plating was adopted for surface finishing of the terminals of package substrates.
Recently, electroless Ni/Pd/Au plating is being offered as an alternative surface finishing process with high solder joint reliability and wire bondability. In the previous studies, the details regarding the influence of Pd thickness on solder joint reliability and IMC growth have not been provided. In this study, the influence of Pd film thickness on solder ball joint reliability was investigated to clearly identify the optimum thickness of the Pd film in electroless Ni/Pd/Au plating.
Experiments
Sample Preparation
A test pattern was formed on an epoxy resin copper cladding laminate (MCL-E-679F; Hitachi Chemical Co. Ltd) using the semi-additive method. The thicknesses of the board and copper pad were 0.6 mm and 25 μm, respectively. Then, solder resist was formed with a solder mask using a photo-definable type resist. The opening diameter of the ball pad was 0.45 mm. These test substrates were covered with electroless Ni/Au (ENIG: electroless Ni/immersion Au) and electroless Ni/Pd/Au (ENEPIG: electroless Ni/electroless Pd/immersion Au) plating. After applying flux, solder balls (SAC305) were attached to the test substrates and passed through a nitrogen-reflow furnace. The thickness of each plating film and the evaluation conditions are listed in Table 1.
Reliability Test on Solder Ball Joints (High-Speed Shear)
As shown in Figure 1, the distance between the shear tool tip and the package substrate was 50 μm. The shear speeds were 20, 200, and 500 mm/s.
Figure 1: Outline of solder-ball shear test.
A high-speed bond tester 4000HS (Dage Precision Industries, Ltd.) was used (Figure 2).
Figure 2: Externals of high-speed shear test equipment (DAGE 4000HS Bond Tester).
Page 1 of 2
Testimonial
"We’re proud to call I-Connect007 a trusted partner. Their innovative approach and industry insight made our podcast collaboration a success by connecting us with the right audience and delivering real results."
Julia McCaffrey - NCAB GroupSuggested Items
BEST Inc. Provides High-Reliability BGA Reballing and Component Rework Services
08/22/2025 | BEST Inc.BEST Inc., a leader in electronic component services, is pleased to announce its component rework services are available for all types of area array devices including ball grid array, land grid array and quad flat no-lead SMT packages.
Indium Corporation Promotes Two Leaders in EMEA (Europe, Middle East, and Africa) Markets
08/05/2025 | Indium CorporationWith its commitment to innovation and growth through employee development, Indium Corporation today announced the promotions of Andy Seager to Associate Director, Continental Sales (EMEA), and Karthik Vijay to Senior Technical Manager (EMEA). These advancements reflect their contributions to the company’s continued innovative efforts with customers across Europe, the Middle East, and Africa (EMEA).
MacDermid Alpha Electronics Solutions Unveils Unified Global Website to Deepen Customer, Talent, and Stakeholder Engagement
07/31/2025 | MacDermid Alpha Electronics SolutionsMacDermid Alpha Electronics Solutions, the electronics business of Elements Solutions Inc, today launched macdermidalpha.com - a unified global website built to deepen digital engagement. The launch marks a significant milestone in the business’ ongoing commitment to delivering more meaningful, interactive, and impactful experiences for its customers, talent, and stakeholders worldwide.
KOKI to Showcase Analytical Services and New HF1200 Solder Paste at SMTA Guadalajara 2025
07/31/2025 | KOKIKOKI, a global leader in advanced soldering materials and process optimization services, will exhibit at the SMTA Guadalajara Expo & Tech Forum, taking place September 17 & 18, 2025 at Expo Guadalajara, Salón Jalisco Halls D & E in Guadalajara, Mexico.
Weller Tools Supports Future Talent with Exclusive Donation to SMTA Michigan Student Soldering Competition
07/23/2025 | Weller ToolsWeller Tools, the industry leader in hand soldering solutions, is proud to announce its support of the upcoming SMTA Michigan Expo & Tech Forum by donating a limited-edition 80th Anniversary Black Soldering Set to the event’s student soldering competition.