-
- News
- Books
Featured Books
- pcb007 Magazine
Latest Issues
Current IssueInventing the Future with SEL
Two years after launching its state-of-the-art PCB facility, SEL shares lessons in vision, execution, and innovation, plus insights from industry icons and technology leaders shaping the future of PCB fabrication.
Sales: From Pitch to PO
From the first cold call to finally receiving that first purchase order, the July PCB007 Magazine breaks down some critical parts of the sales stack. To up your sales game, read on!
The Hole Truth: Via Integrity in an HDI World
From the drilled hole to registration across multiple sequential lamination cycles, to the quality of your copper plating, via reliability in an HDI world is becoming an ever-greater challenge. This month we look at “The Hole Truth,” from creating the “perfect” via to how you can assure via quality and reliability, the first time, every time.
- Articles
- Columns
- Links
- Media kit
||| MENU - pcb007 Magazine
Estimated reading time: 3 minutes
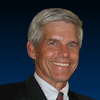
All About Flex: Etchback on Type 3 and Type 4 Flexible Circuits
Through-hole etchback is a requirement that is sometimes specified on medical, military and aerospace procurement documents for multilayer flexible circuits and combination multilayer flex/rigid board circuits. It specifically relates to the copper plated through-holes and the relative dimensions between the dielectric layers and copper layers.
How is etchback created?
Etchback is affected by two common flexible circuit fabrication processes: micro-etch and plasma etch.
To improve plating adhesion, the substrate or base laminate is often submerged or sprayed to remove a slight amount of copper in a micro-etch process. After the various circuit layers are laminated together the through-holes are drilled. This is then followed by a plasma etch step to remove organic resins such as smeared adhesives and dielectric debris. This sequence of processing insures the copper surface in the hole is free from contaminants. This is often referred to as desmearing.
The plasma etch process is controlled to remove a specified amount of dielectric. Etching or removing the dielectric to expose the copper layers as shown in Figure 1 is called etchback or positive etchback. Etchback exposes more of the copper so a larger area can be plated. Essentially three sides of the copper layer can now be plated. This physical feature is used to create a more reliable plated through-hole.
Figure 1: Diagram showing positive etchback.
Etchback is often a requirement for high-reliability applications found in medical, military and aerospace electronics for Type 3 and Type 4 circuits.
A Type 3 circuit is a multilayer flexible circuit consisting of three or more layers with plated through-holes. A Type 4 circuit is a multilayer flexible circuit and rigid board combination consisting of three or more layers with plated through-holes.
IPC-6013 states that etchback shall expose at least 0.003 mm (0.001”) and a maximum of 0.08 mm (0.003”) of copper, when etchback is specified on the procurement documentation. In other words, IPC-6013 does not require etchback on a Type 3 or 4 Class 3 circuit. It is up to the procurement organization to specify that requirement.
Negative etchback is when the copper layer is etched back from the through-hole barrel as shown in Figure 2. IPC-6013 specifies a minimum negative etchback for Class 1, 2 and 3 circuits.
Figure 2: Diagram showing negative etchback.
Maximum allowed negative etchback per IPC6013:
- Class 1: 25 µm (0.001”)
- Class 2: 25 µm (0.001”)
- Class 3: 13 µm(0.0005”)
While postive etchback is usually achieved by a plasma etch process that attacks the dielectric but leaves the metal intact, negative etchback is caused by a copper etchant used in a micro-etch process. Micro-etch is a common step that is performed immediately before the plating step. The micro-etch process normally removes up to two microns of copper, but long dwell times in the etchant or inadequate rinsing may cause negative etchback. IPC-6013 specifically states that no negative etchback is allowed if the procurement document specifies positive etchback.
Etchback has been a requirement for military and aerospace applications for many years. The DoD determined through a series of tests that postive etchback improves the reliabilty of the through-hole. This requirement was developed in the late ‘70s when plating technogies, chemistries and materials were quite different vs. today. Considering the many changes and improvments in plating, there is some controversy about whether etchback is really needed today .
It is doubtful this legacy requirement will go away any time soon as the defense industry is adverse to changes with out compelling motivations. Since most fabricators use plasma etch for desmearing through-holes, achieving the etchback requirement is not a significant added cost. Through-hole performance with etchback has decades of historical performance data to support the requirement. With reliability established over years of performance, decision-making leans toward a conservative approach. As such, the old saying “if it ain’t broke, don’t fix it” will probably rule the day.
Dave Becker is vice president of sales and marketing at All Flex Flexible Circuits LLC.
More Columns from All About Flex
All About Flex: Terms and ConditionsAll About Flex: ISO 9001 Basics
All About Flex: FAQs on UL Listings for Flexible Circuits
All About Flex: Avoiding Trace Fracturing in a Flexible Circuit
Polyimide vs. Silicone for Flexible Heaters
All About Flex: Copper Thickness Requirements for Flex Circuits
All About Flex: Copper Grain Direction
All About Flex: Options for Purchasing Flexible Heaters