The Significance of the PCB in the Value Chain of the European EMS Industry
June 27, 2017 | Pete Starkey, I-Connect007Estimated reading time: 8 minutes
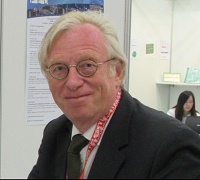
At SMT Nuremberg, Pete Starkey meets with Dieter Weiss, who comments upon the significance of the PCB in the value chain of the European EMS industry, and looks to a future where we embrace an open-minded attitude and a willingness to work together.
Starkey: I’m delighted to have the chance to talk with market analyst Dieter Weiss from Weiss Engineering in Germany, recognised for his knowledgeable and perceptive studies of the European electronics industry. Dieter, thank you for taking time out of your schedule to spare a few minutes to give us your view of the European EMS industry, and how our PCB industry relates to it.
Weiss: Pete, it’s nice to meet you again, and thanks for giving me the opportunity to share some of my observations.
Starkey: Dieter, we are aware that the PCB may represent only a small fraction of the overall cost of an electronic assembly. From your experience, what do you estimate that to be, and what is its significance with regard to the future of the European PCB industry?
Weiss: Clearly, the first fact to have to accept is that the PCB industry in Europe is now relatively small as a result of competition from the Far East. A lot of business has already gone to China and Taiwan, and maybe now to India and Vietnam as well. So this has reduced the number of players in Europe and it is becoming more and more difficult for the European PCB industry to survive. It will not vanish, but PCB manufacturers have to understand the markets of their customers—the OEM industry as well as the EMS industry, and when I talk about EMS industry I mean EMS as contract manufacturers. In the past contract manufacturers tended to be either EMS or ODM companies. Now, the boundaries have vanished and most companies do EMS work as well as ODM work, and they might even have their own products as well. It is very important for manufacturers in the PCB industry to understand what is going on in the EMS industry and how they can still sell their products to the industry, even if their prices are higher.
Starkey: So, back to my question about the cost of the PCB within the overall material cost.
Weiss: If we look at the total material consumption within the EMS and the OEM industry, depending on the company size and product line, material content can range from 30% to 85-90%, depending on whether a company makes just small batches or high-volume products. Combine this with labour costs, and we get to the basis of success or failure in this industry. A company with labour and material costs of 90% will never be able to make big profits. In the revenues of the EMS industry, the PCB accounts for roughly 5%. In some companies, depending on the complexity of the product, it can be as high as 6%. But on the other hand if we are talking about ordinary double-sided or single-sided work, it can easily be below 4%. But still, if that 4% can be purchased less expensively, and without problems, in the Far East, then the EMS industry has little option but to go and source its PCBs there. Because if we look at today’s profit margins in this industry, it’s ridiculous. I have recently analysed a couple of companies from the global top ten EMS, and 50% of their revenues are with five customers, which is totally unhealthy. And they have now gone to other industries, which they called DMS—diversified manufacturing services—in order to beef-up their revenues to reduce their dependence.
Their profit—and I’m not talking about EBIT because to an entrepreneur there is only one line that counts and that’s the bottom line—after tax, net profit—is less than 2%. And that is all the money the entrepreneur can re-use to invest in the future of his company. If EMS companies in general are making less than 2% in profit, then what chance do they have? They might like all the PCB companies in Europe, they might want to support the European industry, but at the end of the day they must look after themselves. That is the problem.
It has become very difficult for companies in the PCB industry to make a living—to get orders from the EMS industry. But if they can offer something the EMS industry needs, which is to have a reliable partner, then it’s still possible. I’ve seen many things; there is one German PCB manufacturer who is now doing a lot of work with a major semi-conductor manufacturer, and this company does a lot of heavy-copper PCBs for them. And that is something the EMS industry will not source from Asia. They will source it from Europe; in this case from a German PCB company. So there are advantages. If you understand the EMS industry, if you know the people, if you have contacts with people, and if you are willing to help them, and that is far beyond just contact with the purchasing guy, you need to have the contacts directly with the development people. That is the basis for success. And I hope that with my studies of the basic numbers of the EMS industry, I can help the PCB industry, as well the EMS industry, to understand the market.
Starkey: Dieter, I know that you have worked closely with the EIPC and run some very successful joint workshops that have enabled the interaction of people from both sides of the industry, the sharing of information and experience and the building of a network of communication and cooperation.
Weiss: Yes, the PCB people need to build up contact with the technical people, not only to the purchasing people and the general managers. They need to show the technical people that the PCB manufacturers have something to offer. They have to bring something to the table, similar to the way the suppliers to the PCB industry bring something to the PCB manufacturers. They don’t just show up and say “I can sell you something.” Instead, they say “I can offer you solutions to your problems.” That is the key¬—if you are able to give the EMS industry solutions to their problems, you can build a strong relationship and then these companies are willing to accept that, although they might have to pay a higher price, at the end of the day they get more reliable product and a lot of technical support in case of any problems arising. So that is the difference. The volume is coming from the Far East but technology is still coming from Europe.
Starkey: Yes, we see this is the ongoing characteristic of the European PCB industry—that it likes to get involved right at the early stage of the design and development process and to build upon those relationships, rather than being a faceless supplier to a faceless customer.
Changing the subject a little, Dieter, I know you have some opinions on cost reduction through miniaturisation. Could you give us an example?
Weiss: Yes, that’s a good subject, and it’s been an area of interest of mine for the 39 years I have worked in the electronics industry; I have written articles on miniaturisation as long ago as the early 1990s. The first concept is a very basic one, about considering the third dimension, not just X and Y but the Z-axis as well. At that time there was a lot of talk about the environmental impact of PCBs and the fact that PCBs contained brominated flame retardants. And it was the big OEMs in those days who brought up the issue that we needed to do something. I wrote an article in a German magazine suggesting that we just reduce the Z-axis finished thickness of the PCB from 1.5 mm to 0.8 mm.
Starkey: Which would very effectively halve the amount of brominated flame retardant without interfering with the chemistry!
Weiss: At that time I was a laminate manufacturer and I knew I was cutting my own flesh, but I didn’t consider that an issue. And anyway, thin laminates commanded higher prices than 1.5 mm rigid. But mine was an environmental issue—I cared about the waste and I had no solution what to do with scrap PCBs, but at least I had an answer how to cut the scrap volume in half. And do you know what the answer of a big German OEM was—and this was the company who had brought up the issue in the first place—“We cannot do this, because the slots in the racks are not the right fit any more!”
Starkey: An excellent example of narrow-minded thinking. I could quote many similar examples from my own experience.
Weiss: And I was manufacturing mass-lam in those days. Look at this circuit I am showing you with 1-mil lines and spaces [Dieter takes a multi-layer PCB from his wallet, about the size and thickness of a credit card]. I was making that on my mass-lam line, with liquid photoresist 3-microns thick. And PCB manufacturers came and looked at my mass-lam line but they never adopted the solutions because it meant changing their way of thinking.
Starkey: The attitude, “We’ve always done it this way, and we always will...”
Weiss: Exactly! And another example of the narrow-minded thinking that was typical in the industry. But looking to the future the key learning is that we have to be open-minded. We have to work together as an industry. We cannot just say that we are a PCB manufacturer or an EMS provider or an OEM. We are all in the same boat. We all have to manufacture electronics, and based on those electronics we have to produce products which meet the needs of the market. We don’t have to make things cheap, we have to make them cost-effective so that on the bottom line the end-user gets what he wants and what he is paying for. Not low cost but quality, reliability, durability and with a good end-of-life solution.
Starkey: Dieter, that’s been a fascinating few minutes’ conversation, with some interesting statistics, some very shrewd observations and a lot of wise advice. Many thanks.
To contact Dieter Weiss, click here.
Testimonial
"We’re proud to call I-Connect007 a trusted partner. Their innovative approach and industry insight made our podcast collaboration a success by connecting us with the right audience and delivering real results."
Julia McCaffrey - NCAB GroupSuggested Items
How Good Design Enables Sustainable PCBs
08/21/2025 | Gerry Partida, Summit InterconnectSustainability has become a key focus for PCB companies seeking to reduce waste, conserve energy, and optimize resources. While many discussions on sustainability center around materials or energy-efficient processes, PCB design is an often overlooked factor that lies at the heart of manufacturing. Good design practices, especially those based on established IPC standards, play a central role in enabling sustainable PCB production. By ensuring designs are manufacturable and reliable, engineers can significantly reduce the environmental impact of their products.
50% Copper Tariffs, 100% Chip Uncertainty, and a Truce
08/19/2025 | Andy Shaughnessy, I-Connect007If you’re like me, tariffs were not on your radar screen until a few months ago, but now political rhetoric has turned to presidential action. Tariffs are front-page news with major developments coming directly from the Oval Office. These are not typical times. President Donald Trump campaigned on tariff reform, and he’s now busy revamping America’s tariff policy.
Global PCB Connections: Understanding the General Fabrication Process—A Designer’s Hidden Advantage
08/14/2025 | Markus Voeltz -- Column: Global PCB ConnectionsDesigners don’t need to become fabricators, but understanding the basics of PCB fabrication can save you time, money, and frustration. The more you understand what’s happening on the shop floor, the better you’ll be able to prevent downstream issues. As you move into more advanced designs like HDI, flex circuits, stacked vias, and embedded components, this foundational knowledge becomes even more critical. Remember: the fabricator is your partner.
MKS’ Atotech to Participate in IPCA Electronics Expo 2025
08/11/2025 | AtotechMKS Inc., a global provider of enabling technologies that transform our world, announced that its strategic brands ESI® (laser systems) and Atotech® (process chemicals, equipment, software, and services) will showcase their latest range of leading manufacturing solutions for printed circuit board (PCB) and package substrate manufacturing at the upcoming 17th IPCA Show to be held at Pragati Maidan, New Delhi from August 21-23, 2025.
MKS Showcases Next-generation PCB Manufacturing Solutions at the Thailand Electronics Circuit Asia 2025
08/06/2025 | MKS Instruments, Inc.MKS Inc, a global provider of enabling technologies that transform our world, today announced its participation in Thailand Electronics Circuit Asia 2025 (THECA 2025), taking place August 20–22 at BITEC in Bangkok.