-
- News
- Books
Featured Books
- smt007 Magazine
Latest Issues
Current IssueWhat's Your Sweet Spot?
Are you in a niche that’s growing or shrinking? Is it time to reassess and refocus? We spotlight companies thriving by redefining or reinforcing their niche. What are their insights?
Moving Forward With Confidence
In this issue, we focus on sales and quoting, workforce training, new IPC leadership in the U.S. and Canada, the effects of tariffs, CFX standards, and much more—all designed to provide perspective as you move through the cloud bank of today's shifting economic market.
Intelligent Test and Inspection
Are you ready to explore the cutting-edge advancements shaping the electronics manufacturing industry? The May 2025 issue of SMT007 Magazine is packed with insights, innovations, and expert perspectives that you won’t want to miss.
- Articles
- Columns
- Links
- Media kit
||| MENU - smt007 Magazine
The Importance of Conformal Coating, Now and in the Future
June 29, 2017 | Happy Holden, I-Connect007Estimated reading time: 7 minutes
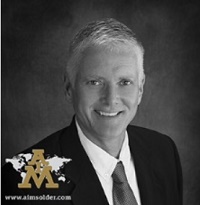
At the Michigan regional SMTA Expo and Tech Forum, held in Grand Rapids on May 11, Technical Editor Happy Holden spent a few minutes with AIM Solder’s Technical Marketing Manager Tim O’Neill. The two discussed O’Neill’s talk that he led earlier that day on the topic of conformal coating over no-clean fluxes, and judging by the number of people in attendance, it’s an area of concern for many people, but also an area of high interest regarding potential future applications, and for good reason.
Happy Holden: Tim, you delivered an excellent talk today about conformal coating over no-clean fluxes, but let me ask you this before we get into the topic of that talk: Why are conformal coatings used, in general?
Tim O’Neill: Conformal coat provides an added measure of environmental protection to meet the mission profile of the assembly. For example, if an assembly is destined for an automotive application, applying conformal coat to boards subject to moisture and temperature variation would be prudent and reasonable.
Holden: In your talk today, you mentioned waterproofing products like those used on the new iPhones and Samsungs. You mentioned reliability, tin whisker abatement and environmental protection, can you elaborate on these?
O’Neill: As of today, applying conformal coat is the only tin whisker mitigation strategy. As I mentioned during the presentation, conformal coat won't prevent the formation of tin whiskers, but it will capture and contain the tin whiskers rather than leaving them free to wreak havoc.
Holden: This topic is pretty timely. You mentioned that 80% of conformal coatings are applied over no-clean fluxes, but I'd like you to repeat your emphasis about the potential future use of the combination of these materials, especially your example.
O’Neill: As the world becomes more connected and devices start to speak to one another, and all the functionality promise that that holds, circuit boards are going to find their way into environments that are more and more harsh as it relates to the circuit board. An example I gave during my speech was that there's a fork that is designed to basically slow down how quickly we eat, which in theory should reduce the amount that we eat, so its goal is weight loss. Imagine that you've got this fork and it vibrates every time you're supposed to pick it up and take another bite, but that fork has to be put through a dishwasher. That was just one example of how electronics are finding their way into applications that were previously unforeseeable and even a bit ridiculous.
Another example that I've used is where a commode or a toilet will be able to analyze your waste and identify medical issues long before your next doctor's visit, which would improve your quality of life, improve your health, and improve overall patient care. Again, a case where a sophisticated electronic device is in an environment that would be incredibly harsh, —one of the worst places you could imagine.
Holden: Tim, can you explain to everybody a little bit more about what's in the paper and about the unique nature of all the tests you completed? This is something that's quite a bit more comprehensive than just an advertising format.
O’Neill: This was a case study, but expanded once we understood that there was a real need for this type of information. Currently, there's no IPC specification for determining compatibility between flux residue and coating. And, as you and I both mentioned, 80% of conformal coat is applied over no-clean flux residue. Those figures are informal but they come from learned people in the conformal coating industry.
While the practice is widespread, the data that justifies the material sets that are chosen is often kept in-house as it is primarily automotive manufacturers. For other industries that are considering deploying this technique, they may not have access to the same resources to be able to establish compatibility. What we determined when we were doing this work for our client was that this is the basis for useful information for people making decisions about material sets and provides an overview of the testing that we conducted to establish compatibility.
We basically deferred to the IPC standards that were applicable to the materials in use. In the case of soldering fluxes, it would be the J-standard 004B and in the case of conformal coat, it was the CC830. We extracted the tests that we felt were most applicable and then combined them in our test vehicles and determined compatibility between the different material sets. Surface insulation resistance testing is something we do extensively as solder paste and flux developers. It's not something that's included in the IPC conformal coating standards. We applied that specification to coatings and learned how conformal coats behave independent of flux interactions. Then we overlayed the combination of fluxes and coating in combination to begin to understand the differences and the interactions between the different material sets.
Our goal was to give this information to the user group that is confronted with making decisions, and hopefully give them enough information to understand what tests they might have to perform. They could also review prior tests between with the coating and paste manufacturers and ask for a recommended material set based on what their requirements and capabilities are.
Holden: Your talk included a lot of interesting slides. Can you remind everybody of the four or five kinds of conformal coatings that you covered?
O’Neill: We studied acrylics, urethanes, acrylated urethanes, silicones and epoxies. We focused primarily on acrylics and urethanes/urethane acrylates because I think those are the most widely deployed.
Holden: I think there's something to be learned from the interaction reported here for people. What was particularly useful how you explained the troubleshooting when you're caught in the middle between a problem where everybody points at the flux or the conformal coatings. Elaborate about how you solve that.
O’Neill: It comes down to this: The coating manufacturers are never going to endorse applying their products over flux residue. They'll never say you should do that. Now, they'll also acknowledge it happens with great regularity. So, when they're confronted with an electro-chemical issue like the one I shared in the presentation, they immediately default to, well you have to clean it to make that problem go away. In fact, if the coating manufacturer and the solder supplier were to engage, we might find that it was a processing issue related to the flux rather than an interaction between the coating and the flux that caused the problem. Therefore, having both areas of expertise responding to the customer needs is really the best way, in my experience, to address these problems when there's conflict between the recommendations of one supplier versus another supplier. I would also say that's also true not just for coating over flux residue, but for other processes as well. When there's so much dependence between the two different materials to be successful, having collaboration between vendors is invaluable in leading to a resolution as quickly as possible.
Page 1 of 2
Suggested Items
Driving Innovation: Direct Imaging vs. Conventional Exposure
07/01/2025 | Simon Khesin -- Column: Driving InnovationMy first camera used Kodak film. I even experimented with developing photos in the bathroom, though I usually dropped the film off at a Kodak center and received the prints two weeks later, only to discover that some images were out of focus or poorly framed. Today, every smartphone contains a high-quality camera capable of producing stunning images instantly.
Hands-On Demos Now Available for Apollo Seiko’s EF and AF Selective Soldering Lines
06/30/2025 | Apollo SeikoApollo Seiko, a leading innovator in soldering technology, is excited to spotlight its expanded lineup of EF and AF Series Selective Soldering Systems, now available for live demonstrations in its newly dedicated demo room.
Indium Corporation Expert to Present on Automotive and Industrial Solder Bonding Solutions at Global Electronics Association Workshop
06/26/2025 | IndiumIndium Corporation Principal Engineer, Advanced Materials, Andy Mackie, Ph.D., MSc, will deliver a technical presentation on innovative solder bonding solutions for automotive and industrial applications at the Global Electronics A
Fresh PCB Concepts: Assembly Challenges with Micro Components and Standard Solder Mask Practices
06/26/2025 | Team NCAB -- Column: Fresh PCB ConceptsMicro components have redefined what is possible in PCB design. With package sizes like 01005 and 0201 becoming more common in high-density layouts, designers are now expected to pack more performance into smaller spaces than ever before. While these advancements support miniaturization and functionality, they introduce new assembly challenges, particularly with traditional solder mask and legend application processes.
Knocking Down the Bone Pile: Tin Whisker Mitigation in Aerospace Applications, Part 3
06/25/2025 | Nash Bell -- Column: Knocking Down the Bone PileTin whiskers are slender, hair-like metallic growths that can develop on the surface of tin-plated electronic components. Typically measuring a few micrometers in diameter and growing several millimeters in length, they form through an electrochemical process influenced by environmental factors such as temperature variations, mechanical or compressive stress, and the aging of solder alloys.