-
- News
- Books
Featured Books
- pcb007 Magazine
Latest Issues
Current IssueInventing the Future with SEL
Two years after launching its state-of-the-art PCB facility, SEL shares lessons in vision, execution, and innovation, plus insights from industry icons and technology leaders shaping the future of PCB fabrication.
Sales: From Pitch to PO
From the first cold call to finally receiving that first purchase order, the July PCB007 Magazine breaks down some critical parts of the sales stack. To up your sales game, read on!
The Hole Truth: Via Integrity in an HDI World
From the drilled hole to registration across multiple sequential lamination cycles, to the quality of your copper plating, via reliability in an HDI world is becoming an ever-greater challenge. This month we look at “The Hole Truth,” from creating the “perfect” via to how you can assure via quality and reliability, the first time, every time.
- Articles
- Columns
- Links
- Media kit
||| MENU - pcb007 Magazine
Estimated reading time: 3 minutes
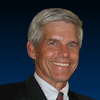
All About Flex: Flexible Circuit Component Assembly…and a Math Lesson
The market for rigid PCBs is estimated to be about 10X the market size for flexible printed circuits (FPCs). As a result, the equipment infrastructure is driven primarily by the needs of the rigid board market. This is true of both equipment used to fabricate the circuitry (image, etch, copper plate, AOI, etc.) and equipment used for component assembly (wave solder and SMT assembly).
Flexible circuits are often sold in multiple-up panels or arrays to facilitate the assembly of SMT components. Coordination between the desires of the assembly supplier and the fabricator can have a significant effect on costs based on material/panel utilization. Fabrication panels are generally larger (12” x 24” and 18”x 24” are common sizes in the U.S.) than assembly panels. Assembly panel sizes should be efficient subsets of fabrication panel sizes to optimize material utilization. The math for determining parts per panel becomes a bit more complicated since fabrication panels will have a “keep out” border around the perimeter of the panel for tooling holes, fiducials, and test coupons.
In addition to considerations for material utilization based on circuit fabrication panel sizes, the quantity of circuits on a given panel size will be a function of several other variables. These variables include: size of the circuit, components to be populated, registration requirements and assembly equipment capability. Multiple fiducials per panel may slow SMT placement rate, but this tradeoff is often trumped by the yield improvement and/or rework avoided.
Positioning parts accurately for SMT placement is a key to successful assembly. Custom carrier pallets are sometimes designed to hold singulated circuits. Another option is to use a machined glass epoxy carrier that is bonded to the circuitry. This can be the same material as is used to selectively apply discrete component stiffeners, thereby integrating the carrier panel and the component stiffeners into a single drilled and routed stiffener. Breakaway features separate the carrier from the circuitry after component assembly. Both these methods mimic the handling conventions of rigid printed circuits.
Multiple-up panels inevitably result in a discussion about defective parts within the panel matrix. False economy results when the contract manufacturer (CM) specifies a “no X-out” requirement. The CM wants to operate their equipment as efficiently as possible, and intuitively this works best if they never deal with defective parts within the assembly panel. But this will often make the CM non-competitive on their bid to capture the business because of the premium paid for circuits.
The yield impact of this requirement can be approximated with statistical probability by the binomial distribution which is used to estimate the probability of drawing a good (or bad) part from a population. The incredible yield impact on the fabrication house is best illustrated with an example. Suppose an assembly panel with eight circuits is required. If any of the circuits within the panel are defective the entire panel is scrap. Even if the fabrication process is running at a 98% yield, the probability of all eight parts being good on a panel tumbles to 85% (0.98 to the 8th power)! As circuit density, tolerances, and layer counts increase, yields of 90–95% are not uncommon. Using the same 8-up panel and a 92% yield, the probability of a defect-free panel is a mere 51%.
These statistical calculations assume defects occur randomly on a panel, which is probably a stretch, but the illustration remains valid. Someone must pay for all those “good” parts that are thrown in the trash can. The fabrication house seeing a “no X-out” requirement will quote the part assuming a poor yield. The likely consequence is the CM uses an inflated circuit cost in their BOM and doesn’t get the contract, especially if they are competing with assembly houses allowing defects within the panel. Today’s modern SMT equipment can recognize black marked circuits and will avoid placing components on these individual circuits. Most CMs recognize this inefficiency is a legitimate cost expectation and are willing to concede some level of defective parts within a panel.
The example with defective parts in a panel is a good illustration of the need for compatibility and cooperation among the members in the supply chain. Sub-optimizing at circuit fab may make component assembly much more cost effective. Or vice versa. Lowest cost is often achieved through compromise. Understanding the big picture will win the game.
Dave Becker is vice president of sales and marketing at All Flex Flexible Circuits LLC.
More Columns from All About Flex
All About Flex: Terms and ConditionsAll About Flex: ISO 9001 Basics
All About Flex: FAQs on UL Listings for Flexible Circuits
All About Flex: Avoiding Trace Fracturing in a Flexible Circuit
Polyimide vs. Silicone for Flexible Heaters
All About Flex: Copper Thickness Requirements for Flex Circuits
All About Flex: Copper Grain Direction
All About Flex: Options for Purchasing Flexible Heaters