-
- News
- Books
Featured Books
- smt007 Magazine
Latest Issues
Current IssueWhat's Your Sweet Spot?
Are you in a niche that’s growing or shrinking? Is it time to reassess and refocus? We spotlight companies thriving by redefining or reinforcing their niche. What are their insights?
Moving Forward With Confidence
In this issue, we focus on sales and quoting, workforce training, new IPC leadership in the U.S. and Canada, the effects of tariffs, CFX standards, and much more—all designed to provide perspective as you move through the cloud bank of today's shifting economic market.
Intelligent Test and Inspection
Are you ready to explore the cutting-edge advancements shaping the electronics manufacturing industry? The May 2025 issue of SMT007 Magazine is packed with insights, innovations, and expert perspectives that you won’t want to miss.
- Articles
- Columns
- Links
- Media kit
||| MENU - smt007 Magazine
Using Paste Flux for Rework
July 10, 2017 | Bob Wettermann, BEST Inc.Estimated reading time: 4 minutes
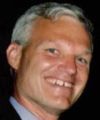
When using a hot air or IR rework system where the reflow cycle is mimicking the original SMT reflow profile, and when using flux for re-attachment, paste flux otherwise known as gel or tacky flux is the correct type of flux to use. The extended time above the solder liquidus temperature causes liquid flux to expire and not be effective during the complete reflow cycle. Paste flux, on the other hand, due to its high viscosity and tack properties, prevents components from being moved during hot-air reflow while being able to remain active for the complete time-temperature period. This prevents disturbed solder joints, which are a defect for all three classes of product, from forming (IPC-A-610F). It also prevents ultra-miniature, low-mass parts from being blown off the board if using a hot air rework source. Typically, the rule of thumb for the reflow cycles is to make sure the tin-lead solders are 30–45 seconds above liquidus whereas the lead-free solder alloys are 60–90 seconds above liquidus. Tacky fluxes are designed to be active for this length of time. Using the properly-formulated lead free or tin-lead version will ensure that the flux remain active during the entire reflow profile.
In addition to the property of being able to remain active during an extended rework cycle time, the flux chemistry is also important. No clean flux residues are intended to be benign after reflow on a PCB when processed properly and are intended to NOT require any post application cleaning. Conversely, water-soluble paste fluxes are generally more active and are designed such that the residues need to be cleaned off the PCB post rework.
While water soluble fluxes are aggressive, giving the rework technician a wider process window, it often bonds with the PCB itself or other metal surfaces, and as a result will require thorough cleaning. It is important to get the cleaning right especially when conformal coating needs to be applied to the PCB. It is also important to clean off the residues when probe testability is important—that is the electrical probe needs to make good electrical contact with the pads.
One of the other advantages of using gel flux is the ability to control the application and hence the area requiring cleaning after soldering. When using liquid fluxes, the material, due to its low viscosity, can spread onto multiple areas of a PCB. This becomes a problem when the flux spreads out from the soldering location and does not experience the full localized reflow temperature cycle. These contaminants left behind can potentially cause electromigration of these soils, which can cause reliability problems later in the life of the assembly. Conversely, the high-viscosity gel fluxes, when dispensed or stencil printed, stay in the area where they were applied. One must be careful of the application of the gel flux as too much flux volume can make the lead or ball float off the pad during the soldering process.
What does paste flux do?
Like all fluxes, the paste fluxes used in rework serve two basic functions. The first job of the flux is to make sure that the oxides are cleaned up from the area to be soldered. It should form an oxidation barrier which allows the BGA ball or paste to coalesce and form a homogenous solder joint. Its other function is to make sure that proper wetting is achieved so that the solder fillet can be formed properly to meet the acceptability requirements.
How does paste flux get applied?
There are a multiple paste flux application methods for the rework of BGAs and other complex components. In some cases, the simplest form of application of the tacky flux is by using a flux dip of the part into a flux bath. This bath is a reservoir slightly oversized compared to the package outline dimensions. The depth of the reservoir is approximately 60% of the ball diameter which allows more than half of the ball to be covered in paste flux when the device bottoms out in the fixture. If the reservoir is kept full of fresh paste flux, the process works well.
Figure 1: Solder paste dipping of POP package into dipping well for paste flux application.
In another application method, paste flux is simply applied to the board area where the device rework location resides. This can be accomplished with a brush, gloved-finger or even selectively applied via a miniature stencil.
The stencil has the added benefit of not having excess flux residues on the PCB to clean off post reflow. Alternatively, dispensing paste flux on to the pads of the device area being reworked has benefits similar to that of stencil printing. Finally, the part may be selectively printed with the paste flux by using the properly-sized rework fixture. In this paste flux application method, the part is held in to an inverted fixture which holds and aligns the part. The bottom side of the component is then stencil printed with the paste flux such that the solder balls, component leads or pads are printed with paste flux.
Figure 2: Dispensing of paste flux onto BGA for rework.
By using the right type of paste flux in both area array and leadless device rework, consistent, acceptable results can be achieved.
Suggested Items
Driving Innovation: Direct Imaging vs. Conventional Exposure
07/01/2025 | Simon Khesin -- Column: Driving InnovationMy first camera used Kodak film. I even experimented with developing photos in the bathroom, though I usually dropped the film off at a Kodak center and received the prints two weeks later, only to discover that some images were out of focus or poorly framed. Today, every smartphone contains a high-quality camera capable of producing stunning images instantly.
Hands-On Demos Now Available for Apollo Seiko’s EF and AF Selective Soldering Lines
06/30/2025 | Apollo SeikoApollo Seiko, a leading innovator in soldering technology, is excited to spotlight its expanded lineup of EF and AF Series Selective Soldering Systems, now available for live demonstrations in its newly dedicated demo room.
Indium Corporation Expert to Present on Automotive and Industrial Solder Bonding Solutions at Global Electronics Association Workshop
06/26/2025 | IndiumIndium Corporation Principal Engineer, Advanced Materials, Andy Mackie, Ph.D., MSc, will deliver a technical presentation on innovative solder bonding solutions for automotive and industrial applications at the Global Electronics A
Fresh PCB Concepts: Assembly Challenges with Micro Components and Standard Solder Mask Practices
06/26/2025 | Team NCAB -- Column: Fresh PCB ConceptsMicro components have redefined what is possible in PCB design. With package sizes like 01005 and 0201 becoming more common in high-density layouts, designers are now expected to pack more performance into smaller spaces than ever before. While these advancements support miniaturization and functionality, they introduce new assembly challenges, particularly with traditional solder mask and legend application processes.
Knocking Down the Bone Pile: Tin Whisker Mitigation in Aerospace Applications, Part 3
06/25/2025 | Nash Bell -- Column: Knocking Down the Bone PileTin whiskers are slender, hair-like metallic growths that can develop on the surface of tin-plated electronic components. Typically measuring a few micrometers in diameter and growing several millimeters in length, they form through an electrochemical process influenced by environmental factors such as temperature variations, mechanical or compressive stress, and the aging of solder alloys.