-
- News
- Books
Featured Books
- pcb007 Magazine
Latest Issues
Current IssueIn Pursuit of Perfection: Defect Reduction
For bare PCB board fabrication, defect reduction is a critical aspect of a company's bottom line profitability. In this issue, we examine how imaging, etching, and plating processes can provide information and insight into reducing defects and increasing yields.
Voices of the Industry
We take the pulse of the PCB industry by sharing insights from leading fabricators and suppliers in this month's issue. We've gathered their thoughts on the new U.S. administration, spending, the war in Ukraine, and their most pressing needs. It’s an eye-opening and enlightening look behind the curtain.
The Essential Guide to Surface Finishes
We go back to basics this month with a recount of a little history, and look forward to addressing the many challenges that high density, high frequency, adhesion, SI, and corrosion concerns for harsh environments bring to the fore. We compare and contrast surface finishes by type and application, take a hard look at the many iterations of gold plating, and address palladium as a surface finish.
- Articles
- Columns
Search Console
- Links
- Media kit
||| MENU - pcb007 Magazine
Estimated reading time: 1 minute
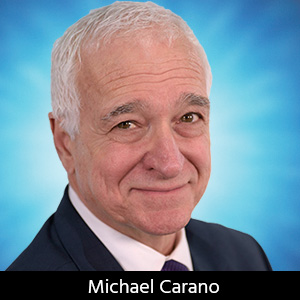
Contact Columnist Form
Trouble in Your Tank: The Critical Importance of Rinsing, Part 1
In nearly every chemical process step in the PCB industry, rinsing is an immediate and required process step. Rinsing is typically a crucial step following a chemical process, and is thought to be one that requires little or no attention to function properly. However, problems caused by ineffective rinsing are responsible for many rejects, as well as huge operating costs in the waste treatment department.
It’s a fact: Processing printed circuit boards consumes large volumes of a precious resource. However, there are ways to perform the function of removing contaminants from the printed circuit board and still conserve water.
At first thought, rinsing is often defined as the removal of process solution from the work, or in the case of the PCB industry, a panel. This is true, if not absolutely true. Rinsing, in general, is not the complete removal of the contaminants, but rather a dilution of a process solution from the work (panel) down to manageable concentrations. With this definition in mind, rinsing systems can be designed to minimize harmful contaminants on a printed circuit board and reduce water consumption. I am often asked if there is some standard that can be applied to the rinsing process. Are all types of contaminants the same? Is there a hard and fast rule to rinsing? The short answer is, not really.
What constitutes a manageable concentration is dependent upon three conditions:
1. The type of contaminant
2. The tolerance of the following process step for the contaminant in question
3. The effect the residual contaminants have on the work
Let us examine the contamination, or “dragin,” of an alkaline cleaner into a persulfate-based microetch vs. the same cleaner dragged into an acid copper plating bath.
To read the full version of this column which appeared in the July 2017 issue of The PCB Magazine, click here.
More Columns from Trouble in Your Tank
Trouble in Your Tank: Yield Improvement and ReliabilityTrouble in Your Tank: Causes of Plating Voids, Pre-electroless Copper
Trouble in Your Tank: Organic Addition Agents in Electrolytic Copper Plating
Trouble in Your Tank: Interconnect Defect—The Three Degrees of Separation
Trouble in Your Tank: Things You Can Do for Better Wet Process Control
Trouble in Your Tank: Processes to Support IC Substrates and Advanced Packaging, Part 5
Trouble in Your Tank: Materials for PWB Fabrication—Drillability and Metallization
Trouble in Your Tank: Supporting IC Substrates and Advanced Packaging, Part 5