-
- News
- Books
Featured Books
- pcb007 Magazine
Latest Issues
Current IssueInventing the Future with SEL
Two years after launching its state-of-the-art PCB facility, SEL shares lessons in vision, execution, and innovation, plus insights from industry icons and technology leaders shaping the future of PCB fabrication.
Sales: From Pitch to PO
From the first cold call to finally receiving that first purchase order, the July PCB007 Magazine breaks down some critical parts of the sales stack. To up your sales game, read on!
The Hole Truth: Via Integrity in an HDI World
From the drilled hole to registration across multiple sequential lamination cycles, to the quality of your copper plating, via reliability in an HDI world is becoming an ever-greater challenge. This month we look at “The Hole Truth,” from creating the “perfect” via to how you can assure via quality and reliability, the first time, every time.
- Articles
- Columns
- Links
- Media kit
||| MENU - pcb007 Magazine
Estimated reading time: 3 minutes
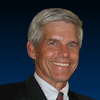
All About Flex: Button Plating on a Flexible Circuit
Button plating describes a fabrication process widely used in the flex circuit industry to selectively electroplate copper to the vias and onto the pads capturing the vias. The rest of the copper traces do not have plating. Another industry term used to describe this feature is pads only plating. Producing a circuit with this processing methodology requires two photolithography steps. The initial imaging/developing process provides electroplating chemistry access to the copper vias and pads. The second process repeats the imaging to define the copper trace pattern. The term button is descriptive as the selectively plated pads are slightly raised from the surrounding copper regions and create a physical signature that looks like a button.
There are two primary applications where button plating is desirable.
- Dynamic flex applications (when continuous or frequent bending of the flex circuit is required) and
- Impedance control applications (often a requirement in high signal speed applications)
Dynamic Flex
Some applications for flexible circuits require specific areas of a circuit to be flexed during the operation of the consumer device. This could be thousands (opening and closing of a notebook computer) if not millions (interconnection to the read/write heads on a disc drive) of flex cycles required during the life of the product. Each dynamic flex application has a unique combination of motion, bend radius, cycle acceleration and proximate circuitry features that may affect flex life performance. Avoiding the addition of electroplated copper onto traces by button plating is a common practice for extending flex life. Since electroplated copper has a different grain structure vs. rolled annealed copper, the grain structure is less flexible and prone to fracture with repeated bending.
To further optimize flex life, additional design rules with specific material sets and features will often be adopted and/or recommended by the fabricator:
- Use of rolled annealed copper which has a grain direction parallel to the roll length
- Orienting the circuit on the panel to position the grain direction perpendicular to the flex plane
- Balancing the material thickness composition to locate the copper layer in the neutral axis of the flex circuit sandwich. This prevents the copper from being in either compression or tension when bent
- Avoiding any unusual shapes of traces or inclusion of features such as vias in the flexing region (parallel traces of equal width are optimum features through a dynamically flexing region)
- Thinner copper will generally perform better than thicker copper for extended flexing
These design practices, in combination with button plating, will help ensure a circuit design has been defined for optimum flexing. Ideally, a flexible circuit should undergo verification testing in a simulated end-product environment to confirm expected performance with some empirical data.
Impedance Control
Applications using high-speed electronics frequently require impedance control. As with dynamic flex applications, a specific structure and material set is ideal:
- Homogenous dielectric material (ER)
- Equivalent dielectric thickness spacing between top and bottom ground planes
- Consistent copper thickness and copper width
- Consistent copper spacing
Electroplated copper thicknesses are more variable with electroplated surfaces vs. non-plated copper. It is not uncommon to see a 10% variation in a circuit’s copper plating thickness as current densities cause features to plate at higher or lower rates. This variation can translate to a similar variation in the impedance. Pads only plating of circuitry requiring impedance control will result in less variability within an individual part and between multiple product builds.
Another critical aspect of impedance control is the relative dielectric (ER) constant of the dielectric stack-up. The dielectric stack-up can consist of one or more layers of dielectric film bonded together with adhesives. The adhesive has a different dielectric coefficient than the dielectric film. Using adhesiveless laminates reduces the variation caused by adhesive and will normally result in a more consistent impedance.
References
1. Processing options when plating vias on double-sided flexible circuitry have been discussed in previous columns publishing at flex.iconnect007.com: Plated Through-holes in Flexible Circuits and Plating Process Options for Flexible Circuits.
2. Impedance calculator, www.ideaconsulting.com.
3. Considerations for Impedance Control in Flexible Circuits, flex.iconnec007.com.
4. Tradeoffs when implementing impedance control, www.allflexinc.com.
5. Impedance control using microstrip and strip line, www.allflexinc.com.
Dave Becker is vice president of sales and marketing at All Flex Flexible Circuits LLC.
More Columns from All About Flex
All About Flex: Terms and ConditionsAll About Flex: ISO 9001 Basics
All About Flex: FAQs on UL Listings for Flexible Circuits
All About Flex: Avoiding Trace Fracturing in a Flexible Circuit
Polyimide vs. Silicone for Flexible Heaters
All About Flex: Copper Thickness Requirements for Flex Circuits
All About Flex: Copper Grain Direction
All About Flex: Options for Purchasing Flexible Heaters