-
- News
- Books
Featured Books
- smt007 Magazine
Latest Issues
Current IssueIntelligent Test and Inspection
Are you ready to explore the cutting-edge advancements shaping the electronics manufacturing industry? The May 2025 issue of SMT007 Magazine is packed with insights, innovations, and expert perspectives that you won’t want to miss.
Do You Have X-ray Vision?
Has X-ray’s time finally come in electronics manufacturing? Join us in this issue of SMT007 Magazine, where we answer this question and others to bring more efficiency to your bottom line.
IPC APEX EXPO 2025: A Preview
It’s that time again. If you’re going to Anaheim for IPC APEX EXPO 2025, we’ll see you there. In the meantime, consider this issue of SMT007 Magazine to be your golden ticket to planning the show.
- Articles
- Columns
Search Console
- Links
- Media kit
||| MENU - smt007 Magazine
4 Ways Your EMS Partner Can Respond to Supply Chain Disruption
July 27, 2017 | Neil Sharp, JJS ManufacturingEstimated reading time: 4 minutes
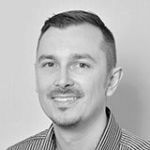
When disruptions to the electronic component supply chain occur, they are painful. Lead-times can extend overnight, prices can treble, and in some cases, parts are placed on allocation or discontinued altogether.
This can leave both original equipment manufacturers (OEMs) and electronics manufacturing service (EMS) providers with limited options when it comes to securing material for production requirements.
Unfortunately, right now, the component market is once again in the middle of being disrupted. After several years of slow growth and minimal investment, coupled with a number of significant M&A’s and an increased demand for memory products, the supply chain is once again struggling to keep up.
In the past few months, more companies have announced extended lead times and products on allocation. The memory sector appears to have been hit the hardest, with all Toshiba products on allocation with a lead time of over three months, and Micron facing similar problems. News outlets and industry sources are also predicting a delay to Apple’s iPhone 8 release due to supply chain constraints.
These concerns amplify the need for EMS firms to have practices in place for dealing with supply chain disruption. In this article, we discuss four ways your EMS partner can mitigate risks to your supply chain.
1. Maintain close relationships with suppliers
A good EMS partner will have long-standing relationships in place with a global network of reputable suppliers. Their suppliers should have an in-depth understanding of the market and be equipped to deal with changes in demand. Regular business reviews should take place between the EMS provider and their key suppliers so that quality, delivery, and pricing issues can be monitored and discussed. In addition, market intelligence and production demand should be shared freely between both parties to ensure there are appropriate supply chain solutions in place.
2. Firm up ‘call off’ demand into firm purchase orders
During times of disruption, your EMS partner may consider advancing their letters of intent to firm orders as a way of securing stock ahead of others. Turning a ‘call off’ annual order into a firm drop provides an extra level of commitment and can help the EMS firm negotiate stock from their suppliers. However, this can be a risk for the EMS provider, particularly if you are not prepared to mirror the same level of commitment. In a worst-case scenario, the EMS provider could be left liable for covering the costs of the unused stock so you may find they will expect a similar level of order coverage from you first before they go ahead and do this themselves. This tends to be more of an issue for customers that are running annual Service Level Agreements (SLAs) with their EMS partners as opposed to placing firm monthly purchase orders.
3. Artificially increase order coverage
Increasing order coverage over and above what is actually needed can be another way of helping to safeguard stock when the supply chain is struggling. In this scenario, the EMS firm has the chance of being seen as the ‘bigger’ customer (based on the supplier's existing order book) and then prioritized as a result. Money talks and the more spend an EMS firm has, or is willing to place during times of turmoil, the higher up the queue they can go. Of course, this does pose a number of risks. If demand is already too high and an allocation situation is in place, these additional orders will only heighten the problem and could lead to further challenges and price rises. It could also backfire on the EMS provider and their customer as the supplier might end up delivering everything they were asked for, impacting the EMS company’s cash flow. Be careful what you wish for.
4. Look at all the alternative parts available
A good EMS provider should review your bill of material (BOM) and build data to ascertain if other components can be used as a replacement. Quite often, multiple semiconductor manufacturers can be used in a design, providing they are the same fit, form and function. The EMS firm won’t want to keep swapping between manufacturers and suppliers but as a short-term solution, buying in alternative devices, approved by you of course, can be a quick win and is often overlooked. And if you haven’t listed any suitable alternatives in your design, your EMS partner should have strong product knowledge and access to suitable alternatives through their network of suppliers which they can then discuss with you.
When faced with any form of disruption, communication is fundamental to a successful partnership. There should be a clear, open and frequent line of communication about any risks and what your EMS partner is doing to eliminate them. But it works both ways too. It’s important for you to keep them abreast of anything that could have an additional impact on the supply chain. For example, by bringing to light any possible increases in demand you have planned for the future or a new product design you plan to bring to market soon.
There are many things that can disrupt an electronic component supply chain, from natural disasters, to price hikes of oil and copper, general economic conditions, and political unrest. Even annual events, like Chinese New Year and Christmas can impact production schedules. The best EMS partners are committed and keep their fingers on the pulse, communicating actions and proactively suggesting solutions to help you mitigate any additional costs or lead-times associated with supply chain issues.
This article originally appeared on the JJS Manufacturing blog, which can be found here.
Suggested Items
RF PCB Design Tips and Tricks
05/08/2025 | Cherie Litson, EPTAC MIT CID/CID+There are many great books, videos, and information online about designing PCBs for RF circuits. A few of my favorite RF sources are Hans Rosenberg, Stephen Chavez, and Rick Hartley, but there are many more. These PCB design engineers have a very good perspective on what it takes to take an RF design from schematic concept to PCB layout.
Trouble in Your Tank: Causes of Plating Voids, Pre-electroless Copper
05/09/2025 | Michael Carano -- Column: Trouble in Your TankIn the business of printed circuit fabrication, yield-reducing and costly defects can easily catch even the most seasoned engineers and production personnel off guard. In this month’s column, I’ll investigate copper plating voids with their genesis in the pre-plating process steps.
Elephantech: For a Greener Tomorrow
04/16/2025 | Marcy LaRont, PCB007 MagazineNobuhiko Okamoto is the global sales and marketing manager for Elephantech Inc., a Japanese startup with a vision to make electronics more sustainable. The company is developing a metal inkjet technology that can print directly on the substrate and then give it a copper thickness by plating. In this interview, he discusses this novel technology's environmental advantages, as well as its potential benefits for the PCB manufacturing and semiconductor packaging segments.
Trouble in Your Tank: Organic Addition Agents in Electrolytic Copper Plating
04/15/2025 | Michael Carano -- Column: Trouble in Your TankThere are numerous factors at play in the science of electroplating or, as most often called, electrolytic plating. One critical element is the use of organic addition agents and their role in copper plating. The function and use of these chemical compounds will be explored in more detail.
IDTechEx Highlights Recyclable Materials for PCBs
04/10/2025 | IDTechExConventional printed circuit board (PCB) manufacturing is wasteful, harmful to the environment and energy intensive. This can be mitigated by the implementation of new recyclable materials and technologies, which have the potential to revolutionize electronics manufacturing.