-
- News
- Books
Featured Books
- pcb007 Magazine
Latest Issues
Current IssueInventing the Future with SEL
Two years after launching its state-of-the-art PCB facility, SEL shares lessons in vision, execution, and innovation, plus insights from industry icons and technology leaders shaping the future of PCB fabrication.
Sales: From Pitch to PO
From the first cold call to finally receiving that first purchase order, the July PCB007 Magazine breaks down some critical parts of the sales stack. To up your sales game, read on!
The Hole Truth: Via Integrity in an HDI World
From the drilled hole to registration across multiple sequential lamination cycles, to the quality of your copper plating, via reliability in an HDI world is becoming an ever-greater challenge. This month we look at “The Hole Truth,” from creating the “perfect” via to how you can assure via quality and reliability, the first time, every time.
- Articles
- Columns
- Links
- Media kit
||| MENU - pcb007 Magazine
Estimated reading time: 3 minutes
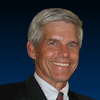
Successful Flex Circuit Assembly
There are key differences between flexible PCBs and rigid PCBs requiring alternative design rules and handling methods. One general area that is often a particular concern occurs when flexible circuits require component assembly. Many contract manufacturers are reluctant to mix rigid and flexible circuits on the same assembly line as the handling and fixturing requirements can be quite different. Characteristics allowing a flexible circuit to be flexible can often present learning curve challenges when component or mechanical assembly is required.
The following are some common issues experienced when assembling flexible circuits.
General Handling Damage
Rigid printed circuits provide structural component support and protection not inherent in flexible circuits. This can often be accommodated on a flex circuit with selective stiffeners, generally either polyimide or glass epoxy. In addition, both surface-mounted and through-hole components can cause handling damage if proper precautions are not taken during assembly. Assembled circuits loosely placed in storage trays can experience damage due to jostling or sliding. Custom inexpensive in-process and shipping storage trays are frequently adopted to minimize the chance of handling damage.
Misaligned Solder
Solder printing with a stencil is the most common method for discrete placement of solder paste and can often be done while the flexible circuit is in a multiple-up array. Compensation of the stencil may be required as flexible circuits are less dimensionally stable versus the rigid board counterpart. A myriad of factors determine if this is necessary including circuit construction, component types, circuit/array size and circuit feature density. Solder paste misalignment causes incomplete solder joints, resulting in opens or intermittent continuity.
Fracturing Due to Bending/Creasing
A flexible circuit is usually folded and/or creased as part of its final installation or during its assembly process. There are a few design features that might cause issues during assembly or installation:
- If the bend is too close to a solder joint, the probability of a solder fracture increases significantly. While the copper on a flexible circuit is flexible, the intermetallic layer between the solder and copper is not. Adequate distance between the solder joint and bend area can be chosen strategically by coordination with a flex circuit applications engineer.
- With a double-sided flex construction, one needs to be concerned about the “I-beam” effect. This occurs when top- and bottom-side traces are directly aligned on opposite sides of the dielectric. This forces the outside layer copper trace into a tension mode and increases the probability of trace fracture.
- The copper type will also have an impact. Rolled annealed (RA) copper is generally better equipped to withstand folding or creasing than electrodeposited (ED) copper. It is advisable to make sure RA copper is used for a part used in a dynamic flex working environment and insure the grain direction is parallel to the fold line.
Stiffener/Connector Alignment
Many times, an FR-4 (glass epoxy) stiffener is used to support a connector. It is a mistake to have the stiffener hole sizes exactly match the flexible circuit openings. Misalignment will result in problems with the connector assembly or the access to the through-hole connector. The stiffener needs to have larger openings to allow for placement tolerances.
Packaging/Shipping/Unpacking
Flexible circuit assemblies are more prone to damage due to handling. Parts loosely packaged in a bag can experience damage during shipping or when parts are removed from the package. Special packaging trays or foam bags will usually provide enough protection to assure the part arrives to the assembly line without damage.
With proper designs and handling methods, flexible circuit assemblies have proven to be as reliable as an assembly of a rigid PCB. Since each part is a custom design, nuances of materials, fabrication processes, and end environment create an individually unique performance situation. Good communication between the flexible circuit manufacturer and the end user can go a long way to ensure minimal assembly issues. An experienced applications engineering support staff should guide a customer to define a robust interconnection part number.
More Columns from All About Flex
All About Flex: Terms and ConditionsAll About Flex: ISO 9001 Basics
All About Flex: FAQs on UL Listings for Flexible Circuits
All About Flex: Avoiding Trace Fracturing in a Flexible Circuit
Polyimide vs. Silicone for Flexible Heaters
All About Flex: Copper Thickness Requirements for Flex Circuits
All About Flex: Copper Grain Direction
All About Flex: Options for Purchasing Flexible Heaters