-
- News
- Books
Featured Books
- smt007 Magazine
Latest Issues
Current IssueWhat's Your Sweet Spot?
Are you in a niche that’s growing or shrinking? Is it time to reassess and refocus? We spotlight companies thriving by redefining or reinforcing their niche. What are their insights?
Moving Forward With Confidence
In this issue, we focus on sales and quoting, workforce training, new IPC leadership in the U.S. and Canada, the effects of tariffs, CFX standards, and much more—all designed to provide perspective as you move through the cloud bank of today's shifting economic market.
Intelligent Test and Inspection
Are you ready to explore the cutting-edge advancements shaping the electronics manufacturing industry? The May 2025 issue of SMT007 Magazine is packed with insights, innovations, and expert perspectives that you won’t want to miss.
- Articles
- Columns
- Links
- Media kit
||| MENU - smt007 Magazine
Cleaning that Matters
August 15, 2017 | Stephen Las Marias, I-Connect007Estimated reading time: 10 minutes
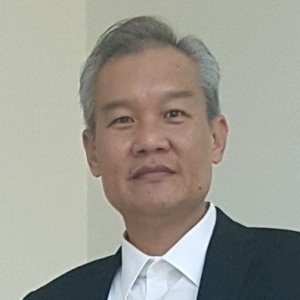
As the executive director of Zestron Precision Cleaning Sdn Bhd, James Yeoh is responsible for South Asia—predominantly Taiwan and the Southeast Asian region. In an interview with SMT Magazine, Yeoh discusses the challenges in the cleaning industry, and strategies that can help manufacturers address those issues. He also covers the need for continuous education when it comes to cleaning, and how automation can ensure the stability of cleaning systems.
Stephen Las Marias: What is your company’s sweet spot?
James Yeoh: We are one of the cleaning companies with seven technical centers to support our customers: one in the United States, one in Germany, two in China—in Shanghai and Shenzhen—one in Malaysia, one in Tokyo, and one in South Korea. Very soon we will have an eighth—in Taiwan—which we hope to start running this this year or early next year.
None of our competitors has as many technical centers as we have. And in all our technical centers, we have more than 70 different cleaning machines, most of which are owned by cleaning equipment manufacturers for us to run evaluation and trials for customers. One thing that is unique here is that we can replicate whatever customer parameters are at different sites if there is a need to.
This is one of our strongest selling points. We can do as many trials as the customer wants before they qualify our chemistry. Also, we have a very strong application technology team, and these people are so mobile. Take my region for example: Every week, there is a Zestron application engineer somewhere travelling in our region to talk to customers. And we are continuously employing people to cater to the increase in our business as well as customer base.
Another strength we have is that we continue the education process for the industry. We call it Zestron Academy. We have highly qualified trainers to teach and train the industry.
For us here in Asia, we continue to provide free seminars. In my region alone, we organize 30 training sessions every year. Some of them are for the whole industry, while others we do for particular customers. For instance, one customer has 20 engineers interested in cleaning. We will come in and do the training for them.
In fact, we have plans in South Asia to expand the Zestron Academy. Not only do we want to train the engineers of our customers, but we want to extend it to technical colleges because cleaning is not part of their syllabus of studies. When these graduates eventually get hired, they will already be able to handle cleaning.
We will extend Zestron Academy, but it is not something that will happen tomorrow. It is in the pipeline, maybe two or three years down the road. We also want a dedicated academy team. Right now, we use the application engineers to do the training. But what we want to do at the end of the day is to have a separate Zestron Academy team, so that it can stand alone by itself.
Las Marias: In which end-markets are you seeing strong growth?
Yeoh: We have seen very good growth in the automotive and semiconductor industries. The latter is very wide, we have power module and automotive electronics, we can cover IoT, we can cover mobile phones. Even aerospace industry is a growing market. If you talk about the automotive and the aerospace industries, there’s no compromise. Cleaning is a priority.
Las Marias: From a cleaning standpoint, what challenges are your customers facing?
Yeoh: Basically, most of the challenges are very closely related. Our customers don’t have a lot of equipment, because these are all investments. Some customers have one or two cleaning machines. In some cases, these customers, especially the EMS providers, may have 20 different products to run. It’s a big challenge because the pastes are different, a lot of their fluxes are different, there are variations in products, and they need to run. They need to clean with just one machine, and they need to clean with just one chemical. That is a challenge for them. And it is a part of our duty to make sure we go in and optimize and help them, with one chemical solution, to clean all their boards.
The market now is driven predominantly by two trends: one is IoT, the other is hybrid vehicles. These two will be very significant going forward. When we talk about hybrid or electric vehicles, these are very European and American driven. This industry is growing and will continue to drive the market. When you have more and more electronics in the vehicles, there is a need for more cleaning.
Meanwhile, things have become narrower and smaller. At one point, you can no longer put a lot of components into the board. So probably, the ICs or packages will be 2D or 3D. In the future, the ICs will be so small that there will be an even lower standoff height. Now, it’s 0.05 mm. It may continue to become lower than that. This is a challenge because water will no longer be able to penetrate such low standoff heights. You need chemicals to wash. But you also must consider material compatibility issues.
We are the first in the market to offer what we call pH-neutral cleaning solutions. Now, we have our third-generation pH-neutral cleaners. With pH-neutral solutions, we are able to address material compatibility issues, especially with copper lead frames.
Las Marias: Do people still have some sort of misconception when it comes to no-clean solder pastes?
Yeoh: If you talk about the aerospace and the automotive industries, cleaning ensures it’s 100% clean. Even though you use no-clean flux or paste, you still clean because there is a reliability issue and safety issue. When it comes to reliability and safety, I think nobody wants to take a chance. A few years ago, people started talking about no-clean solders and fluxes, and that the cleaning business will go away. It did not. In fact, the business just kept on increasing, first, because of the safety and reliability issues; and second, as you go to lower and lower standoff heights, you basically just cannot clean with water anymore. So, cleaning is essential; it will be a priority as we move forward. Of course, there are still some who use DI (deionized) water for cleaning. But moving forward, as standoff heights become significantly lower, there is no choice. Chemical cleaning is the trend.
Las Marias: There are still companies who are manually dosing their bath to maintain the stability of the cleaning solution. What’s the challenge here?
Yeoh: Manual replenishment is not wrong; it’s okay. The only thing is that what I think companies look for in terms of their production is stability. If I am a manager in a manufacturing company, I will always look at consistency. If Zestron tells me my cleaning system must run at, let’s say, 20%, I want to make sure that at any point in time when I go to the line or when my customer comes for audit, it’s 20%. If I manually do it, it may fluctuate. With Zestron EYE and Zestron EYE CM, all these are coordinated, which means if the concentration level drops from 20%, there will have a trigger that will inform you that it’s time to replenish the chemical. In terms of ISO, it is also good. Because you will have a record to show your auditors that it’s always at 20%.
This is one of the areas that the Zestron EYE or Zestron EYE CM can help customers in terms of stability and consistency, which are very important now from a manufacturing perspective to ensure yield.
Page 1 of 2
Suggested Items
Driving Innovation: Direct Imaging vs. Conventional Exposure
07/01/2025 | Simon Khesin -- Column: Driving InnovationMy first camera used Kodak film. I even experimented with developing photos in the bathroom, though I usually dropped the film off at a Kodak center and received the prints two weeks later, only to discover that some images were out of focus or poorly framed. Today, every smartphone contains a high-quality camera capable of producing stunning images instantly.
Hands-On Demos Now Available for Apollo Seiko’s EF and AF Selective Soldering Lines
06/30/2025 | Apollo SeikoApollo Seiko, a leading innovator in soldering technology, is excited to spotlight its expanded lineup of EF and AF Series Selective Soldering Systems, now available for live demonstrations in its newly dedicated demo room.
Indium Corporation Expert to Present on Automotive and Industrial Solder Bonding Solutions at Global Electronics Association Workshop
06/26/2025 | IndiumIndium Corporation Principal Engineer, Advanced Materials, Andy Mackie, Ph.D., MSc, will deliver a technical presentation on innovative solder bonding solutions for automotive and industrial applications at the Global Electronics A
Fresh PCB Concepts: Assembly Challenges with Micro Components and Standard Solder Mask Practices
06/26/2025 | Team NCAB -- Column: Fresh PCB ConceptsMicro components have redefined what is possible in PCB design. With package sizes like 01005 and 0201 becoming more common in high-density layouts, designers are now expected to pack more performance into smaller spaces than ever before. While these advancements support miniaturization and functionality, they introduce new assembly challenges, particularly with traditional solder mask and legend application processes.
Knocking Down the Bone Pile: Tin Whisker Mitigation in Aerospace Applications, Part 3
06/25/2025 | Nash Bell -- Column: Knocking Down the Bone PileTin whiskers are slender, hair-like metallic growths that can develop on the surface of tin-plated electronic components. Typically measuring a few micrometers in diameter and growing several millimeters in length, they form through an electrochemical process influenced by environmental factors such as temperature variations, mechanical or compressive stress, and the aging of solder alloys.