-
- News
- Books
Featured Books
- pcb007 Magazine
Latest Issues
Current IssueInventing the Future with SEL
Two years after launching its state-of-the-art PCB facility, SEL shares lessons in vision, execution, and innovation, plus insights from industry icons and technology leaders shaping the future of PCB fabrication.
Sales: From Pitch to PO
From the first cold call to finally receiving that first purchase order, the July PCB007 Magazine breaks down some critical parts of the sales stack. To up your sales game, read on!
The Hole Truth: Via Integrity in an HDI World
From the drilled hole to registration across multiple sequential lamination cycles, to the quality of your copper plating, via reliability in an HDI world is becoming an ever-greater challenge. This month we look at “The Hole Truth,” from creating the “perfect” via to how you can assure via quality and reliability, the first time, every time.
- Articles
- Columns
- Links
- Media kit
||| MENU - pcb007 Magazine
Estimated reading time: 4 minutes
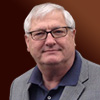
Contact Columnist Form
Mr. Laminate Tells All: Where in the Holy Halogens did 900, 900, 1500 Come From?
The 900, 900, 1500 is not a combination to an enormous safe that contains the remains of Jimmy Hoffa, nor is it the weight of three elephants at the San Diego Zoo in kilograms. The 900, 900, 1500 is the maximum parts per million (ppm) of bromine and chlorine and the total bromine and chlorine in a material that can be defined as “halogen-free” in the electronics industry today. But where did these requirements come from? Clearly, 900 ppm of bromine or chlorine is obviously not halogen-free. Some would argue that it is not even low-halogen at all.
In 2001, during an International Electrotechnical Commission (IEC, Geneva CH) meeting of TC91 Working Group 4: Base Materials and Boards, the member countries decided there should be a specification for FR-4 copper-clad laminates that were halogen-free. Several Japanese manufacturers were selling these laminates and prepregs around the world, primarily in Europe, but there were no specifications to conduct commercial business. Although the square meters per month of sales were quite small at the time, we knew that this product line would grow.
IEC 61249-2-21 was the document number designated in becoming the first FR-4 halogen-free standard in the world. The Working Group 4 decided to base the document and the requirements on the brominated counterpart IEC-61249-2-7 in terms of other property requirements. The main change was a relaxed moisture absorption requirement since halogen-free resins were worse than their brominated counterparts in these tests.
This was the easy part, but defining the halogen content would prove to be more controversial. During subsequent meetings, the Japanese National Committee, led by Dr. Aki Shibata, proposed a maximum of about 450 ppm of chlorine and about 450 ppm of bromine as a specification limit. As the USA National Committee leader, I proposed 1200 ppm for both halogens, as several domestic resin companies presented data that this was a more reasonable number. The debate continued for more than one year. No punches were thrown, but there was still a lot of pain.
One problem was that the copper-clad laminates (CCL), comprised of a higher resin content, generated a higher test value, since all the chlorine and bromine contaminants were coming from the epoxy resin components. For example, a 0.10 or 0.20 mm thick CCL may have a resin content of more than 65% while a 1.52 mm thick CCL may have only 40% resin. So two CCLs using the same resin varnish, but different constructions, generated significantly different results in the halogen test. In the end, the test specimen was defined as eight plies of low resin content/fiberglass fabric construction.
With the test specimen defined, the compromise on the definition of halogen-free between Dr. Shibata and me was decided upon as 900 ppm maximum chlorine, 900 ppm maximum bromine and a new requirement of 1500 ppm maximum for chlorine plus bromine. The rest of the Working Group 4 members agreed to these proposed specifications and the document was completed using the IEC process scheme for developing standards with a vote of the member countries.
Page 1 of 2
More Columns from Mr. Laminate Tells All
Mr. Laminate Tells All: Is Your Laminate and Prepreg Supplier Cheating? Only One Way to Find OutMr. Laminate Tells All: Good Morning, Vietnam!
Mr. Laminate Tells All: IPC-4101 Validation Services—The QPL Lives Again
IEC TC111 and the Ban on PTFE: Update
PTFE is About to be Banned by IEC TC111
The Certification of IPC-4101D Polyimide Base Materials: Buyer Beware
CEM-3 Reinvents Itself (Again)—or, Atari Game Boards on eBay?
Who Would Like a Mil-Spec Audit?