-
- News
- Books
Featured Books
- pcb007 Magazine
Latest Issues
Current IssueInventing the Future with SEL
Two years after launching its state-of-the-art PCB facility, SEL shares lessons in vision, execution, and innovation, plus insights from industry icons and technology leaders shaping the future of PCB fabrication.
Sales: From Pitch to PO
From the first cold call to finally receiving that first purchase order, the July PCB007 Magazine breaks down some critical parts of the sales stack. To up your sales game, read on!
The Hole Truth: Via Integrity in an HDI World
From the drilled hole to registration across multiple sequential lamination cycles, to the quality of your copper plating, via reliability in an HDI world is becoming an ever-greater challenge. This month we look at “The Hole Truth,” from creating the “perfect” via to how you can assure via quality and reliability, the first time, every time.
- Articles
- Columns
- Links
- Media kit
||| MENU - pcb007 Magazine
Estimated reading time: 6 minutes
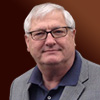
Contact Columnist Form
Mr. Laminate Tells All: Is Your Laminate and Prepreg Supplier Cheating? Only One Way to Find Out
A huge void now exists in the base materials specifications for PCBs and PCB assemblies with the inactivation of MIL-S-13949 for base materials and the loss of the military’s oversight function. IPC-4101 replaced the specification for MIL-S-13949, but there was no mechanism established for an oversight function. There was no longer a police officer to make sure the suppliers were manufacturing according to the new industry specifications. There was no longer the threat of being dropped from the Qualified Product Lists (QPLs) because testing is not being carried out following the industry required test procedures, test frequency, and sampling plans.
No one came for the annual audit to review the mountain of test reports with Group A, Group B, and Group C data. What basis did the military have to define a “lot” as 200 pressed sheets or one press load—whichever is greater? And the industry felt that this “significant yearly cost” of doing business was not necessary. Statistical process control (SPC) and other manufacturing improvements would fill the void. Now, more than 30 years later, we are so, so, so wrong.
When all this went down at Isola, our two plants in the USA and our five facilities in Europe continued to test at the same level as before. As data was generated, we changed the frequency of some tests from once per lot to once per day, some monthly tests became quarterly tests, and some quarterly tests became yearly tests—all based on the statistical data gathered from our in-house testing capability. At that time, virtually all of the USA laminate and prepreg suppliers could test for all of the performance requirements in IPC-4101, except for fungus resistance.
Since the time when MIL-S-13949 was canceled, and IPC-4101 took its place, the world has changed. The number of original MIL-S-13949 producing and certifying factories in the U.S. has dwindled to less than five. Literally hundreds of new base material suppliers have sprung up around the world and have grown quite large, but none of them remember or know anything about MIL-S-13949. None of them remember the audits, required testing, or non-conformances that shut factories down immediately until the non-conformance was corrected—nor the yearly oversight from DSCC Dayton.
As the director of quality, I remember how I could have gone to jail for falsifying a MIL-SPEC Certificate of Compliance (C of C). I signed the C of Cs for the IPC-4101 the same way as I did for MIL-S-3949. I did not cheat.
Around 2012, IPC was being encouraged to get back into the role of auditor with respect to assembly, fabrication, and base materials specifications. Specifically, the Board of Governors pushed the TAEC and the Board of Directors to take charge of the IPC documents. IPC hired Randy Cherry in March 2013 to lead this effort and created a group called IPC Validation Services.
Randy and his team created standardized audit lists for various IPC documents for assembly, PCBs, wire and cable harnesses, and base materials. If you were to look at the IPC website under the heading “knowledge,” you could now find the “validation services” link in the far-right-hand column. This link has all the companies that have passed the audit and qualification testing requirements for each document. These now represent true and trusted suppliers to the electronics industry.
For example, for the assembly part of the electronics supply chain, 32 facilities have been successfully audited and passed all the requirements for IPC-A-610/ IPC-J-STD-001:
- USA: 11
- China: 15
- Taiwan: 2
- Sweden: 1
- Germany: 1
- Argentina: 1
- Denmark: 1
IPC-WHMA-620, Acceptability of Wire Harness and Cable, has 11 facilities on the Qualified Manufacturers List (QML). For the standard IPC-1791—Trusted Electronics Design, Manufacture, and Assembly—there are 10 QML facilities. For manufacturers of laminates and prepregs, according to IPC-4101, there are three listed vendors on the QPL. We say QPL because each product must be tested in accordance with the qualification testing outlined in Table 3-1 and pass the minimum requirements shown on the appropriate specification sheet. The initial testing for each specification sheet must be conducted at an IPC-qualified laboratory.
There are several reasons why copper-clad laminate and prepreg suppliers are not following the requirements and certification for IPC-4101. One is that they simply do not understand the document. For example, paragraph 3.4 indicates that all products shall be qualified, and the tabulated data be available for anyone to review. Only U.S. manufacturers ever prepared such a report. I have never had a board shop provide the qualification test data from their CCL supplier because they do not have any idea of what I am talking about. When I conduct a validation services audit against IPC-4101E, this is the first document I require:
3.4 Qualification Testing: Laminate and prepreg base materials furnished under this specification shall be qualified as described in Table 3-1 for laminates and Table 3-2 for prepregs. The supplier shall retain on file, supporting data that the materials meet the requirements of this specification using the test methods described herein. Qualification testing shall be performed to demonstrate the supplier’s ability to meet all of the requirements of each applicable specification sheet for each base material.
Another failure is the lack of test equipment. The original base material suppliers had all the test equipment required to conduct the Group A, Group B, and Group C lot testing. Now, many suppliers do not even have the Group A test equipment, let alone Groups B and C. Somehow, though, certifications with test data miraculously appear from these companies for each lot of certification.
IPC posts all the test reports from the qualification testing on the IPC website for everyone to review. According to Bob Neves of Microtek Changzhou, who has tested all the candidates for Validation Services for IPC-4101 to date, commented, “The unique requirements of individual IPC-4101E specification sheets were established to ensure that complying materials would meet the demands of their intended end-use application.”
Neves further stated, “As an IPC Validation Services Qualified independent laboratory, we provide testing services to assure compliance to the IPC-4101E specification sheet requirements and report passing or failing results that allow IPC to certify compliance under their Validation Services Program."
From my perspective, I have found a significant number of copper-clad laminate and prepreg suppliers simply worried about passing the most basic standard in the industry. From 1996, when virtually all the base material suppliers in the U.S. and many in Europe certified to MIL-S-13949, there are only three that have passed the IPC Validation Services QPL to be a trusted supplier. Clearly, the world has changed and not for the better. Why would any company build Class 3 PCBs on untested substandard base materials?
Currently, three laminate and prepreg manufacturers are QPL listed on the IPC website that are considered “trusted suppliers:”
- Arlon Electronic Materials, USA
- Taiwan Union Technology Corp (TUC), Taiwan
- Ventec Shenzhen, China
Summary
OEMs have reached out to IPC for help in monitoring suppliers and their usage of IPC-4101. The IPC Validation Services Program can prepare suppliers of base materials, conduct the on-site audit, and ultimately have their company names added to the IPC QPL listing of trusted suppliers.
To those out there who are reluctant to obtain the IPC QPL for IPC-4101E, I understand your reluctance. And to those who have a solid quality system and are producing laminates and prepregs to the standard, what are you waiting for?
Douglas J. Sober is the president of Essex Technologies Group.
More Columns from Mr. Laminate Tells All
Mr. Laminate Tells All: Good Morning, Vietnam!Mr. Laminate Tells All: IPC-4101 Validation Services—The QPL Lives Again
IEC TC111 and the Ban on PTFE: Update
PTFE is About to be Banned by IEC TC111
The Certification of IPC-4101D Polyimide Base Materials: Buyer Beware
CEM-3 Reinvents Itself (Again)—or, Atari Game Boards on eBay?
Who Would Like a Mil-Spec Audit?
Mr. Laminate Tells All: Where in the Holy Halogens did 900, 900, 1500 Come From?